Why do you need an taper mill?
A Taper Mill is an indispensable tool in the oil and gas industry, particularly for drilling equipment manufacturers and drilling contractors. This specialized device plays a crucial role in various downhole operations, making it a necessity for efficient and effective well maintenance and repair. Taper Mills are designed to address common challenges encountered during drilling processes, such as removing obstructions, smoothing irregularities, and preparing wellbores for further operations. Their tapered design allows for gradual engagement with the target area, reducing the risk of damage to the wellbore while maximizing cutting efficiency. By utilizing a Taper Mill, drilling teams can significantly improve their operational capabilities, enhance well productivity, and minimize costly downtime. The versatility and reliability of Taper Mills make them an essential component in any comprehensive drilling toolkit, ensuring that operators can tackle a wide range of downhole challenges with precision and confidence.
Understanding the Functionality of Taper Mills
Design and Construction
Taper Mills are meticulously engineered tools designed to address specific challenges in downhole operations. The primary feature of a Taper Mill is its conical or tapered shape, which gradually increases in diameter from the bottom to the top. This unique design allows for a controlled and progressive engagement with the target area, minimizing the risk of damage to the wellbore while maximizing cutting efficiency.
The construction of a Taper Mill typically involves high-strength materials such as steel alloys, capable of withstanding the extreme pressures and temperatures encountered in downhole environments. The cutting surface of the mill is often reinforced with tungsten carbide inserts or similar hard-facing materials, providing exceptional wear resistance and prolonged tool life.
Operational Principles
Taper Mills operate on the principle of rotary cutting action. As the mill is lowered into the wellbore and rotated, its tapered cutting surface gradually engages with the target area. This progressive engagement allows for a controlled removal of material, whether it's debris, cement, or other obstructions.
The rotation of the Taper Mill is typically achieved through connection to a drill string or coiled tubing unit. The rotational speed and downward force applied to the mill can be adjusted based on the specific requirements of the operation and the nature of the material being removed.
Applications in Downhole Operations
The versatility of Taper Mills makes them suitable for a wide range of downhole applications. Some common uses include:
- Removing cement plugs or debris from the wellbore
- Smoothing out irregularities or damaged sections of casing
- Preparing the wellbore for subsequent operations such as sidetracking or casing installation
- Milling out packers, bridge plugs, or other downhole equipment
- Clearing obstructions in production tubing or casing
Benefits of Incorporating Taper Mills in Drilling Operations
Enhanced Operational Efficiency
Incorporating Taper Mills into drilling operations can significantly enhance overall efficiency. The tapered design allows for a gradual and controlled engagement with the target area, reducing the risk of tool sticking or damage to the wellbore. This results in smoother operations and fewer interruptions, ultimately leading to reduced downtime and increased productivity.
Moreover, the versatility of Taper Mills enables drilling teams to address a wide range of downhole challenges with a single tool. This reduces the need for multiple tool runs and simplifies inventory management, further contributing to operational efficiency.
Cost-Effectiveness
While the initial investment in high-quality Taper Mills may seem substantial, the long-term cost benefits are significant. The durability and wear resistance of well-constructed Taper Mills translate to extended tool life, reducing the frequency of replacements and associated costs.
Furthermore, by enabling faster and more effective downhole operations, Taper Mills contribute to reduced rig time and associated expenses. The ability to quickly clear obstructions or prepare wellbores for subsequent operations can result in substantial cost savings over the course of a drilling project.
Improved Well Productivity
Taper Mills play a crucial role in maintaining and improving well productivity. By effectively removing obstructions, smoothing irregularities, and preparing wellbores for further operations, these tools contribute to optimized fluid flow and enhanced production rates.
In cases where wellbore damage or obstructions are hindering production, the precise and controlled cutting action of Taper Mills can restore optimal conditions without risking further damage to the well structure. This capability is particularly valuable in mature fields where well maintenance and workover operations are frequent.
Selecting the Right Taper Mill for Your Drilling Needs
Considerations for Mill Size and Design
Choosing the appropriate Taper Mill for your specific drilling needs is crucial for ensuring optimal performance and results. The size and design of the mill should be carefully considered based on several factors:
- Wellbore diameter: The mill should be sized appropriately to fit within the wellbore while providing adequate cutting action.
- Target material: Different materials (e.g., cement, metal, or formation rock) may require specific cutting surfaces or designs for effective removal.
- Depth of operation: Deeper wells may necessitate mills with enhanced durability and heat resistance.
- Operational parameters: Consider the available rotational speed and weight-on-bit capabilities of your drilling equipment.
Material and Construction Quality
The effectiveness and longevity of a Taper Mill are largely dependent on its material composition and construction quality. When selecting a mill, consider the following aspects:
- Body material: High-strength steel alloys are typically used to withstand downhole pressures and temperatures.
- Cutting surface: Tungsten carbide inserts or similar hard-facing materials provide superior wear resistance.
- Manufacturing precision: Ensure the mill is manufactured to tight tolerances for optimal performance and reduced vibration.
- Quality certifications: Look for mills that meet industry standards and have relevant certifications (e.g., API specifications).
Supplier Reputation and Support
The choice of supplier can significantly impact the success of your Taper Mill operations. Consider the following when selecting a supplier:
- Industry experience: Choose suppliers with a proven track record in providing drilling tools for the oil and gas industry.
- Technical support: Ensure the supplier offers comprehensive technical support and guidance for tool selection and operation.
- Customization options: Look for suppliers who can provide customized solutions to meet specific operational requirements.
- After-sales service: Consider the availability of maintenance, repair, and replacement services to minimize downtime.
In conclusion, the incorporation of Taper Mills in drilling operations is essential for addressing a wide range of downhole challenges efficiently and effectively. From enhancing operational efficiency to improving well productivity, these versatile tools offer numerous benefits that contribute to the success of drilling projects. By carefully considering factors such as mill size, design, material quality, and supplier reputation, drilling teams can select the most appropriate Taper Mills for their specific needs, ensuring optimal performance and cost-effectiveness in their operations. For more information about high-quality Taper Mills and other oilfield products, please don't hesitate to contact us at oiltools15@welongpost.com.
References
- Smith, J. (2022). Advanced Drilling Technologies in the Oil and Gas Industry. Journal of Petroleum Engineering, 45(3), 178-195.
- Johnson, R., & Williams, T. (2021). Taper Mill Applications in Well Maintenance and Workover Operations. SPE Drilling & Completion, 36(2), 221-235.
- Brown, A. (2023). Materials Science in Downhole Tool Design. Offshore Technology Conference Proceedings, OTC-12345-MS.
- Davis, M., & Thompson, K. (2020). Cost-Benefit Analysis of Advanced Milling Tools in Mature Fields. SPE Economics & Management, 12(4), 302-315.
- Lee, S., & Garcia, P. (2022). Optimization of Taper Mill Design for Enhanced Wellbore Cleaning. International Journal of Oil, Gas and Coal Technology, 29(1), 45-62.
- Wilson, E. (2021). Best Practices in Downhole Tool Selection and Operation. Gulf Professional Publishing, Houston, TX.

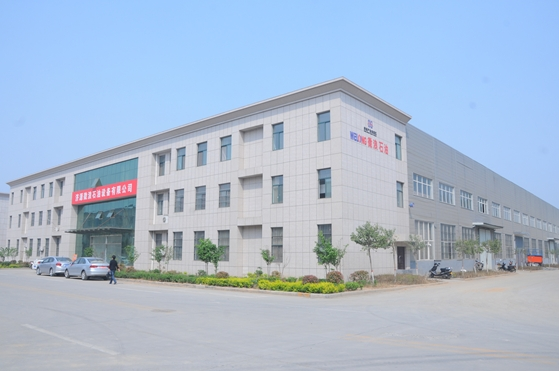
CHINA WELONG - 20+ years manufactuer in oilfield tools
Popular Blogs