What is the difference between a tapered and standard end mill?
When it comes to precision machining, the choice of cutting tool can significantly impact the quality and efficiency of the process. One of the most commonly debated topics in milling applications is the difference between tapered and standard end mills. While both tools are used for cutting and shaping materials, they have distinct characteristics that make them suitable for different tasks.
A taper mill, also known as a tapered end mill, features a cutting edge that gradually narrows towards the tip, forming a taper. This unique design allows the taper mill to reach into areas that a standard end mill cannot, making it especially useful for applications that require precise and complex geometries. On the other hand, a standard end mill has a straight profile along its length, with the cutting edges running perpendicular to the shank. While it’s highly versatile and capable of handling a variety of tasks, it lacks the versatility of the taper mill when it comes to accessing angled or contoured surfaces.
Understanding these differences can help you choose the right tool for your application, whether you're working with intricate designs, tight spaces, or standard milling tasks. In this blog, we will explore how tapered and standard end mills differ in terms of design, compatibility, functionality, and optimal use cases.
Design Differences Between Tapered and Standard End Mills
The design of a cutting tool plays a significant role in determining its performance, and when it comes to tapered and standard end mills, the structural differences are quite pronounced.
1. Shape and Cutting Geometry
The most obvious difference between a tapered and a standard end mill is the shape of the cutting edges. A tapered end mill has a conical shape, where the diameter gradually decreases along its length. This tapering provides greater access to hard-to-reach areas, such as deep pockets or angled surfaces, that a standard end mill may struggle to reach. The tapered design is ideal for machining parts with steep walls or for creating features that require precise, angled cuts.
In contrast, a standard end mill has a straight, cylindrical shape, with the cutting edges running perpendicular to the tool’s axis. The primary benefit of this design is its versatility. Standard end mills can perform a variety of tasks, such as slotting, profiling, and face milling, and are suitable for cutting flat surfaces or relatively shallow features. However, they lack the ability to reach into confined or tapered areas.
2. Tool Length and Cutting Depth
The length of a tapered end mill is typically longer than that of a standard end mill to accommodate its ability to reach deeper areas. Tapered mills are often used when the machining depth exceeds what a standard end mill can handle without the risk of tool deflection or excessive wear. The longer length combined with the taper design allows for greater flexibility when working with deep and narrow cavities.
3. Flute Design and Cutting Efficiency
The flute design of both tools also varies. Tapered end mills generally have fewer flutes than standard end mills, as the tapering process can limit the amount of cutting edge available. As a result, tapered mills are often used for finishing operations where a smooth, precise cut is necessary, while standard end mills with more flutes are better suited for roughing operations that demand high material removal rates.
The flute angles and overall geometry of the two tools contribute directly to their cutting efficiency. Standard end mills, with their straighter design, typically offer better chip removal capabilities, allowing for faster material removal in rough milling applications. Tapered mills, however, excel in finishing tasks, providing more control over the cutting process, especially when precise, smooth cuts are needed in complex geometries.
4. Versatility and Use Cases
Tapered end mills are highly specialized tools designed for applications where access to tight spaces, complex angles, or intricate shapes is required. These mills are often used in industries like aerospace, mold-making, and die-casting, where parts have precise contours and specific angles that need to be machined accurately.
In comparison, standard end mills are more versatile and can be used across a wide range of applications, from roughing to finishing. They are more commonly used for general machining tasks, including milling flat surfaces, grooves, slots, and contours in a variety of materials, making them a go-to tool for many machinists.
Compatibility of Tapered and Standard End Mills
When selecting a milling tool for a particular job, understanding the compatibility of the tool with both the material being machined and the machine itself is crucial. The differences in design and functionality between tapered and standard end mills make them suitable for distinct applications. Let's explore how these tools compare in terms of compatibility with materials and machine setups.
1. Material Compatibility
Both tapered and standard end mills are versatile enough to work with a wide range of materials, but their performance can vary based on the material being machined.
Tapered End Mills: The ability to access hard-to-reach areas makes tapered mills particularly useful when machining complex materials, including high-strength alloys, hardened steel, and titanium. Their tapering design allows for precise cuts and finishes in challenging geometries. Taper mills are ideal for applications where the material is difficult to machine using a standard end mill, such as deep cavities or steep angles.
Standard End Mills: These mills are equally versatile, able to handle soft metals like aluminum, brass, and copper, as well as harder materials, such as steel and stainless steel. They perform particularly well in applications where surface finish and material removal rate are important, such as roughing, slotting, and profiling operations. However, when it comes to machining complex or tapered parts, standard end mills may fall short due to their inability to access certain areas.
2. Machine Compatibility
While both taper and standard end mills can be used on various types of machining centers, including vertical and horizontal mills, the characteristics of each tool may affect machine performance and setup.
Tapered End Mills: Due to their longer lengths and conical shape, tapered mills require a machining setup that can handle deeper tool penetration without compromising tool stability. In some cases, you may need a toolholder with higher rigidity or tapered toolholders to ensure that the tool remains stable during machining. Furthermore, since the taper mill is often used for precise, finishing cuts, the machine should be capable of fine-tuning feed rates and cutting speeds to prevent tool deflection and ensure accuracy.
Standard End Mills: These mills are generally easier to set up and more forgiving in terms of machine compatibility. They are designed for general-purpose milling, meaning they can be used effectively across a range of machine types and setups. The shorter length and straight profile of standard mills allow them to handle higher material removal rates and accommodate heavier feeds and cuts. However, when working with materials that require more delicate machining, additional care must be taken to avoid tool chatter or excessive wear.
3. Toolholding and Clamping Systems
The clamping and toolholding system used for both taper and standard end mills plays a significant role in their performance. Tapered mills, because of their longer and more delicate geometry, may require specialized toolholders with increased gripping force to ensure precise machining without vibration or tool deflection. Standard mills, on the other hand, have a more straightforward design and can often be used with a wider variety of toolholding systems, including collet chucks and end mill holders.
For both tools, it's crucial to ensure that the machine setup is compatible with the tool's design, as improper toolholding or clamping can lead to inaccuracies, poor surface finishes, and tool wear.
Tapered End Mills Offer Better Access for Complex Geometries
One of the standout advantages of tapered end mills over their standard counterparts is their ability to access and machine complex geometries. The unique design of a tapered mill, with its conical cutting edges, allows for cutting in tight, hard-to-reach areas where standard end mills would struggle to operate. Let’s explore the specific ways in which tapered end mills excel in machining complex geometries.
1. Access to Steep Angles and Deep Features
The tapered design of these mills is particularly beneficial when machining parts that feature steep walls, angled surfaces, or deep cavities. In standard milling operations, where straight cutting edges are necessary for precise, flat cuts, a standard end mill might not be able to access the deeper portions of a part, especially when there is a sharp angle involved.
A tapered mill’s ability to gradually reduce its diameter towards the tip makes it ideal for accessing angled or conical features. Whether you're working on parts for the aerospace, automotive, or mold-making industries, tapered mills allow for the creation of precise cuts in areas that would be impossible for a standard mill to reach. Their flexibility in navigating deep pockets or angled corners helps improve the efficiency and versatility of the machining process.
2. Precision for Intricate Detail
In applications requiring fine details, such as creating profiles, engraving, or contour milling, tapered end mills provide a high level of precision. The gradual taper allows for smooth transitions between different depths and angles in the material, resulting in a cleaner cut with fewer tool marks. These features are especially important in industries like mold-making or die-casting, where intricate features and fine finishes are crucial.
By using tapered end mills, machinists can create a variety of features, including tapered holes, v-shaped cuts, and relief cuts, all of which are vital in producing parts with high-precision dimensions. The flexibility to work on both shallow and deep cuts without the risk of damaging the part or the tool makes these mills indispensable for intricate designs.
3. Enhanced Capability for 3D Milling Applications
With advancements in CNC machining, 3D milling has become an essential part of manufacturing complex, multi-dimensional components. Tapered end mills are often used in conjunction with 3D machining because they provide the ability to access complex, curved surfaces and undercuts that require a tapered geometry.
For example, in industries such as aerospace, where parts often have complex contours and shapes, tapered mills allow for highly accurate cuts to achieve the desired geometry. The tool's ability to machine at varying depths along the taper also makes it useful for operations requiring undercut milling, where the tool needs to cut into areas below the part's surface.
In these cases, a standard end mill simply cannot achieve the same level of precision or access to tight, complex geometries. The versatility of the tapered mill ensures that a wide variety of shapes, from simple sloped cuts to more intricate 3D features, can be efficiently machined.
Tapered End Mills Are Ideal for Finishing Operations
Finishing operations are critical in machining, as they focus on achieving the final surface finish and exact dimensions required for a part. This is where tapered end mills shine. The unique design of tapered end mills makes them especially well-suited for these operations.
1. Precision and Surface Finish
In finishing operations, the primary goal is to achieve a smooth, high-quality surface finish with tight tolerances. Tapered end mills excel in this regard due to their gradual tapering geometry. The cutting action of a tapered mill allows it to produce fine cuts and smooth finishes, especially in areas where surface quality is paramount, such as in mold making, aerospace components, and medical devices. The shape of the tool helps to reduce tool marks, and the precise control over cutting depth ensures that the final product meets the required surface standards.
By using a tapered end mill, machinists can achieve a consistent and even surface finish, even on complex geometries or when working with materials that are challenging to machine, like hardened steels or titanium alloys. The ability to make detailed cuts with minimal vibration or tool deflection results in cleaner surfaces and reduced post-processing time.
2. Reduced Tool Wear in Finishing Cuts
One of the challenges in finishing operations is minimizing tool wear while still achieving the desired results. Since tapered end mills are specifically designed to handle finer, more delicate cuts, they experience less wear during finishing operations compared to standard mills. This is particularly important when working with high-precision parts that require multiple finishing passes.
The reduced cutting forces of tapered end mills also contribute to extending tool life. The cutting edge engages gradually with the material, which helps to reduce the stress on the tool. This means that machinists can expect a longer lifespan from tapered mills, making them a cost-effective option for finishing tasks that require high repeatability and accuracy.
3. Access to Tight Tolerances
Finishing operations often require the machining of parts with tight tolerances—sometimes in the range of thousandths of an inch. Tapered end mills are ideal for these types of tasks because their unique geometry allows for precise control over the cutting process. Whether you're working with complex curved surfaces or need to create small, intricate features, the taper mill ensures that every pass results in a precise cut that adheres to the specified tolerance.
Additionally, tapered end mills are often used to create undercuts or reach into areas that would be inaccessible for standard tools. This makes them invaluable for finishing the inner contours or angled surfaces of parts, ensuring that the final product meets the required specifications.
4. Versatility in Finishing Different Materials
Tapered end mills also demonstrate versatility when used in finishing operations across various materials. Whether machining metals, plastics, or composites, tapered mills can be optimized for different materials to achieve the best possible finish. Their ability to handle both soft and hard materials—such as aluminum, stainless steel, or titanium—makes them a go-to tool for shops that work with a diverse range of materials.
This flexibility in material compatibility, combined with the precision of the tapered design, allows machinists to maintain high surface quality across various job requirements without the need to switch tools frequently.
5. Toolpath Optimization for Finishing
When it comes to finishing operations, optimizing the toolpath is just as important as selecting the right tool. With tapered end mills, machinists can take advantage of advanced toolpath strategies, such as adaptive clearing, spiral milling, and zig-zag finishing, to minimize cutting time and maximize efficiency. These toolpaths help achieve a consistent finish across the entire part while minimizing the wear on the tool and the machine.
Tapered mills are highly adaptable to different toolpath strategies, providing flexibility in machining processes. Whether you are finishing flat surfaces, complex contours, or angled features, tapered end mills can be tailored to the needs of the job.
Tapered End Mills Reduce Material Build-Up
One of the significant advantages of using tapered end mills is their ability to reduce material build-up during machining. Material build-up, or built-up edge (BUE), occurs when the material being cut adheres to the cutting edges of the tool, resulting in poor cutting performance, excessive wear, and reduced tool life. Tapered mills are specifically designed to address this issue, making them a preferred tool for many applications.
1. Efficient Chip Removal
Tapered end mills excel in chip evacuation, which is a critical factor in preventing material from adhering to the cutting edges. The geometry of the tapered tool—especially in combination with its helix angle—promotes effective chip flow, ensuring that chips are quickly cleared away from the cutting zone. This efficient chip removal prevents the accumulation of material on the cutting edges, which can otherwise cause tool clogging or BUE.
When material builds up on the tool, it not only affects the surface finish of the part but can also result in tool wear and overheating. Tapered end mills, by reducing chip re-circulation, allow for cleaner cuts and extended tool life, which helps to maintain machining efficiency over longer periods.
2. Better Heat Dissipation
Excessive heat is one of the leading causes of material build-up, particularly when machining tough materials such as stainless steel or titanium. As the tool comes into contact with the material, friction generates heat, and if the chips are not efficiently evacuated, they can cause heat to accumulate at the cutting edges.
The tapered geometry of the end mill assists with better heat dissipation, as the cutting edges engage the material at more controlled angles. By promoting a smoother cutting action and ensuring that heat is distributed more evenly across the tool, tapered mills help prevent localized heat build-up, which would otherwise lead to material sticking to the tool.
3. Increased Cutting Efficiency
Tapered end mills can be used at higher cutting speeds without the risk of material build-up. Thanks to their design, these tools maintain a consistent cutting action, which allows for faster material removal rates without compromising tool performance. When standard tools are used, especially in difficult-to-machine materials, excessive heat and chip re-circulation can cause premature wear and poor finishes.
In contrast, tapered end mills maintain cutting efficiency even during extended machining operations. The constant chip removal and lower heat generation contribute to consistent performance, reducing the chances of workpiece damage and tool failure. As a result, shops using tapered end mills can achieve greater productivity and better-quality results without the frequent interruptions caused by tool wear or material build-up.
4. Reduced Tool Deflection
Tool deflection, especially when machining at high speeds, can cause uneven cutting forces and contribute to material build-up. Tapered end mills, with their unique geometry, provide better stability compared to standard end mills. This stability allows the tool to engage the material more evenly, preventing sudden deflections that might otherwise result in a buildup of material on the tool.
The reduced deflection leads to a more precise cutting action, which is especially important when working with delicate or complex parts. By minimizing material build-up, the tool is able to perform consistently, producing high-quality results over a longer period without the need for frequent adjustments or tool changes.
5. Enhanced Surface Finish
Material build-up not only affects the tool but also directly impacts the surface finish of the part. As the material adheres to the tool’s cutting edges, it can leave undesirable marks or imperfections on the workpiece. Tapered end mills, by reducing material build-up, ensure a cleaner cut and a smoother surface finish. This is particularly valuable in industries where surface quality is critical, such as in aerospace, medical device manufacturing, or automotive components.
With reduced material build-up, tapered end mills help produce parts with improved dimensional accuracy and surface integrity, reducing the need for secondary finishing operations.
Best Practices for Using Tapered End Mills
To achieve the best results with tapered end mills, it’s essential to follow best practices that optimize tool life, surface finish, and machining efficiency. Using these mills effectively requires careful consideration of factors such as cutting parameters, tool selection, and machine settings. Let’s explore some best practices to help you get the most out of your tapered end mills.
1. Optimize Cutting Speeds and Feeds
One of the most important aspects of using a tapered end mill effectively is optimizing cutting speeds and feeds. Since tapered end mills are typically used for delicate and precise operations, running them at improper speeds can result in tool wear, material build-up, or poor surface finish. The right cutting speed ensures efficient chip removal and minimizes heat generation, while the correct feed rate ensures that the tool engages the material at an appropriate rate, reducing the risk of vibration or chatter.
For high-speed machining (HSM), it's essential to balance the surface speed and feed per tooth to achieve optimal cutting conditions. Experimenting with different speeds and feeds for your specific material and application is key. Many manufacturers provide cutting guidelines for tapered end mills that can help you start with a good baseline.
2. Choose the Right Tool for the Job
Choosing the right tapered end mill for your specific application is critical. Tapered mills come in different angles (ranging from shallow to steep tapers), flute designs, and coatings. For example, shallow taper mills are ideal for finishing operations where surface finish is critical, while steeper taper mills are suited for applications that require deeper cuts or machining of angled features.
Additionally, selecting the right tool coating can enhance tool performance by providing heat resistance, wear resistance, and lubrication during the cutting process. For example, TiAlN coatings are effective in reducing friction and extending tool life when machining tough materials like stainless steel or titanium. When selecting a tapered end mill, it’s important to consider the material being machined, the required geometry, and the desired surface finish.
3. Use Proper Toolpath Strategies
The success of your tapered end mill depends not only on the tool itself but also on the toolpath strategy. 3D toolpaths, such as spiral milling, adaptive clearing, or zig-zag finishing, are ideal for complex geometries that require gradual engagement with the material. These strategies allow for better chip removal, smoother cuts, and less deflection on the tool.
Optimized toolpaths can also help reduce cutting forces, which are essential when working with delicate parts or hard materials. Some CNC machines come with specific toolpath options designed for tapered end mills, and utilizing these can help increase machining efficiency while reducing wear on the tool and workpiece.
4. Monitor Tool Wear and Replace When Necessary
While tapered end mills are designed for longevity, it’s important to regularly monitor tool wear to ensure that performance remains consistent. Even with optimal cutting conditions, tools can wear out over time, especially when machining tough materials or when subjected to extended cutting times. Indicators of tool wear include increased cutting forces, poor surface finish, and excessive tool deflection.
Checking the tool for signs of wear and replacing it before it becomes too worn can help maintain the quality of your work. Additionally, tool regrinding can extend the life of the tapered mill, although it’s essential to maintain the original geometry for best results.
5. Maintain Proper Machine Setup and Rigidity
To get the most out of your tapered end mills, it’s essential to ensure that your CNC machine is set up correctly. Proper toolholder selection and machine rigidity are vital factors for achieving consistent results. A stable machine setup reduces the risk of tool deflection, which can negatively affect surface finish and dimensional accuracy.
Ensure that the machine is equipped with high-quality toolholders that maintain the taper angle and cutting forces during operation. If the toolholder is not rigid enough or if it has too much runout, it could lead to poor performance and premature tool wear. Also, make sure the workpiece is securely clamped to avoid movement during the cutting process, which could affect the precision of the tapered end mill.
6. Implement Proper Coolant Strategies
Using the right coolant can significantly impact the performance of your tapered end mills, particularly in challenging applications like high-speed machining or when cutting hard materials. Coolants help dissipate heat, reduce friction, and prevent material build-up on the tool. For tapered end mills, high-pressure coolant systems are especially effective in flushing chips away from the cutting area and keeping the tool cool.
It’s important to choose a coolant that’s compatible with the material being machined and the tool’s coating. For instance, water-based coolants are often preferred for aluminum and soft metals, while oil-based coolants might be better for tougher materials like stainless steel or titanium.
Conclusion
In summary, tapered end mills offer numerous advantages over standard end mills, particularly when precision, versatility, and surface finish are paramount. These tools provide distinct benefits in machining complex geometries, finishing operations, and reducing material build-up. By selecting the right tapered mill for your specific application and following best practices for its use, you can significantly enhance machining efficiency, extend tool life, and achieve superior results across various materials. With their unique design and superior performance, tapered end mills are an invaluable tool for manufacturers in industries such as aerospace, automotive, and medical device production.
At Welong, we offer a wide range of customized oilfield products, including taper mills designed to meet the highest standards of quality and performance. Our tools are ISO 9001-2015 & API 7-1 certified, ensuring reliable and timely delivery.
For more information or inquiries, please contact us at oiltools15@welongpost.com. We are here to help you select the perfect tapered end mill for your specific needs.
References
1. "The Design and Application of Tapered End Mills," Journal of Manufacturing Processes.
2. "Tool Selection for Milling Operations," International Journal of Machine Tools and Manufacture.
3. "Optimizing Cutting Parameters for Precision Milling," International Journal of Precision Engineering and Manufacturing.
4. "End Mill Selection and Machining Guidelines," Practical Machinist.
5. "Cutting Tool Materials and Applications," ASM Handbook.
6. "Improved Performance of Tapered End Mills in Complex Machining," Journal of Materials Processing Technology.

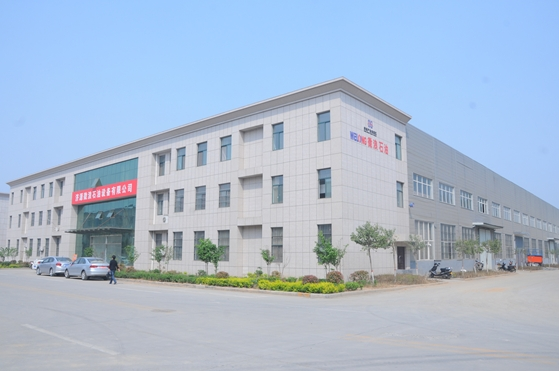
CHINA WELONG - 20+ years manufactuer in oilfield tools
Popular Blogs