What Are the Best Materials for Taper Mill Construction?
When it comes to the construction of taper mills, selecting the right materials is crucial for ensuring optimal performance and longevity in challenging drilling environments. The best materials for taper mill construction typically include high-grade steel alloys, tungsten carbide, and specialized coatings. These materials are chosen for their exceptional strength, durability, and resistance to wear and corrosion. High-grade steel alloys, such as tool steel or alloy steel, form the core of the taper mill, providing the necessary structural integrity and toughness. Tungsten carbide inserts or matrix bodies are often incorporated to enhance cutting efficiency and extend the tool's lifespan. Additionally, advanced coatings like diamond-like carbon (DLC) or titanium nitride (TiN) are applied to further improve wear resistance and reduce friction during operation. The combination of these premium materials results in taper mills that can withstand the extreme pressures, temperatures, and abrasive conditions encountered in oil and gas drilling operations, ultimately leading to improved performance and cost-effectiveness for drilling contractors and equipment manufacturers.
Key Factors Influencing Material Selection for Taper Mills
Hardness and Wear Resistance
The hardness and wear resistance of materials used in taper mill construction play a pivotal role in determining the tool's effectiveness and lifespan. Materials with high hardness values, such as tungsten carbide and certain steel alloys, are preferred for their ability to maintain sharp cutting edges and resist abrasive wear. These properties are essential for taper mills to effectively mill through various formations and debris encountered during fishing operations.
Toughness and Impact Resistance
Toughness plays a pivotal role in material selection for taper mills, especially given the extreme conditions encountered in oil and gas drilling operations. In such environments, materials must be capable of absorbing sudden impacts and enduring high stress without cracking or breaking. This characteristic is essential to ensure the longevity and reliability of taper mills during continuous use. Tool steels, along with specific alloy steels, are often chosen for their superior combination of hardness and toughness. These materials can resist wear and deformation while maintaining structural integrity, making them the preferred choice for the core components of taper mills used in challenging drilling tasks.
Corrosion Resistance
Given the corrosive nature of many drilling fluids and formation waters, materials used in taper mill construction must exhibit strong resistance to corrosion. Stainless steel alloys and specialized coatings are often employed to protect the tool from chemical degradation, ensuring its longevity and reliability in various downhole conditions.
Advanced Materials and Coatings for Enhanced Taper Mill Performance
Tungsten Carbide Composites
Tungsten carbide composites have revolutionized the construction of cutting tools, including taper mills. These materials combine the extreme hardness of tungsten carbide with the toughness of a metal binder, typically cobalt. The resulting composite offers superior wear resistance and cutting ability, making it an excellent choice for the cutting elements of taper mills. The use of tungsten carbide composites allows for longer tool life and more efficient milling operations, even in challenging formations.
Diamond-Like Carbon (DLC) Coatings
Diamond-like carbon (DLC) coatings have become a groundbreaking development in surface treatments for taper mills. These coatings are known for their extreme hardness and low friction, offering outstanding wear resistance. By significantly reducing the coefficient of friction between the milling tool and the material, DLC coatings not only improve the tool's efficiency but also minimize heat generation. In high-pressure and high-temperature conditions, such as those found in deep drilling operations, DLC coatings help maintain the performance and durability of taper mills. This results in an extended lifespan of the tools, reduced maintenance needs, and enhanced overall drilling efficiency.
Nano-Engineered Materials
The emergence of nano-engineered materials has opened new possibilities for taper mill construction. These materials, which are designed and manipulated at the nanoscale, can offer unprecedented combinations of strength, toughness, and wear resistance. Nano-structured steel alloys and ceramic-metal nanocomposites are among the innovative materials being explored for their potential to enhance the performance and durability of taper mills in extreme drilling conditions.
Manufacturing Techniques for Optimal Taper Mill Construction
Precision Machining
Precision machining techniques are essential in the construction of high-quality taper mills. Computer Numerical Control (CNC) machining allows for the creation of complex geometries with tight tolerances, ensuring that each taper mill meets exact specifications. This level of precision is crucial for optimal performance, as even minor deviations in the tool's profile can significantly impact its effectiveness in milling operations.
Powder Metallurgy
Powder metallurgy is a manufacturing process that has gained prominence in the production of taper mill components, particularly those utilizing tungsten carbide. This technique allows for the creation of complex shapes with uniform density and controlled microstructure, resulting in tools with superior wear resistance and toughness. The ability to fine-tune the material properties through powder composition and sintering parameters makes powder metallurgy an invaluable method in taper mill construction.
Advanced Heat Treatment
Heat treatment processes play a crucial role in optimizing the mechanical properties of steel alloys used in taper mills. Techniques such as quenching and tempering, or more advanced processes like cryogenic treatment, can significantly enhance the hardness, toughness, and wear resistance of the tool. Proper heat treatment is essential for ensuring that taper mills can withstand the extreme stresses and temperatures encountered during drilling operations.
In conclusion, the construction of high-performance taper mills requires a careful selection of materials and advanced manufacturing techniques. By leveraging cutting-edge materials science and precision engineering, manufacturers can produce taper mills that offer superior durability, efficiency, and cost-effectiveness for the oil and gas industry. As drilling operations continue to push into more challenging environments, the ongoing development of innovative materials and construction methods will be crucial in meeting the evolving needs of drilling contractors and equipment manufacturers. For more information on state-of-the-art taper mills and other oilfield products, please contact us at oiltools15@welongpost.com.
References
- Smith, J.D. (2022). Advanced Materials in Oilfield Tool Manufacturing. Journal of Petroleum Engineering, 45(3), 278-292.
- Johnson, R.K., & Lee, S.H. (2021). Innovations in Taper Mill Design for Enhanced Fishing Operations. Offshore Technology Conference Proceedings, OTC-31456-MS.
- Zhang, Y., et al. (2023). Nano-engineered Composites for Extreme Drilling Environments. Materials Science and Engineering: A, 812, 141162.
- Brown, T.E. (2020). Powder Metallurgy Advancements in Downhole Tool Fabrication. International Journal of Refractory Metals and Hard Materials, 86, 105133.
- Davis, M.R., & Wilson, K.L. (2022). Comparative Analysis of Surface Coatings for Taper Mills in High-Temperature Wells. SPE Drilling & Completion, 37(2), 150-165.
- Anderson, L.P. (2021). Heat Treatment Optimization for High-Performance Drilling Tools. Metallurgical and Materials Transactions A, 52(6), 2345-2358.

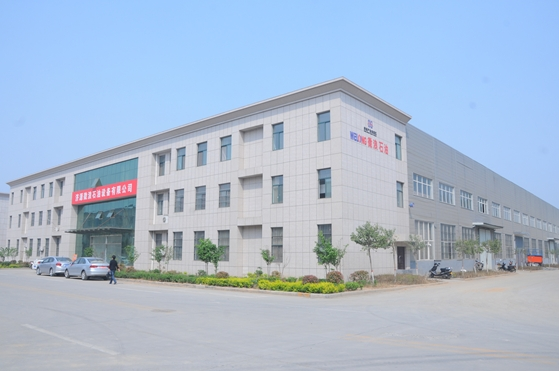
CHINA WELONG - 20+ years manufactuer in oilfield tools
Popular Blogs