How to Troubleshoot Common Issues with Taper Mills?
Taper mills are indispensable tools in the oil and gas industry, used for removing obstructions and debris from wellbores. However, like any sophisticated equipment, they can encounter issues that require troubleshooting. Understanding how to address common problems with taper mills is crucial for maintaining operational efficiency and minimizing downtime. This comprehensive guide will walk you through the process of identifying and resolving typical issues that may arise when using taper mills. By following these troubleshooting steps, drilling contractors and engineers can ensure optimal performance, extend the lifespan of their equipment, and maintain cost-effective operations. From addressing uneven wear patterns to dealing with unexpected vibrations, we'll cover a range of scenarios that operators might face in the field. With the right knowledge and approach, most taper mill issues can be resolved quickly and effectively, allowing for seamless continuation of drilling operations.
Understanding Taper Mill Functionality and Common Problems
The Basics of Taper Mill Design and Operation
Taper mills are highly specialized tools used in the oil and gas industry, primarily for tapering and removing obstructions within wells. Their unique conical shape enables a gradual and controlled engagement with debris, reducing the likelihood of damage to the wellbore. These tools are often equipped with hardened cutting surfaces, which enhance durability and improve cutting efficiency. Additionally, taper mills feature fluid channels that facilitate the removal of debris, ensuring smoother operation and minimizing the risk of clogging. A thorough understanding of these key characteristics is essential for identifying potential issues during milling operations, ensuring optimal performance and avoiding costly setbacks.
Recognizing Signs of Taper Mill Wear and Damage
Regular inspection of taper mills is essential for early problem detection. Look for signs of uneven wear on the cutting surfaces, which can indicate improper use or alignment issues. Damaged or missing cutting elements, unusual discoloration, or deformation of the mill body are all red flags that require immediate attention. Keeping a log of these observations can help in identifying patterns and preventing recurring problems.
Common Issues Encountered During Taper Mill Operations
Several issues can arise during taper mill operations, including reduced cutting efficiency, excessive vibration, and premature wear. These problems may stem from factors such as incorrect operating parameters, incompatible well conditions, or inadequate maintenance. Recognizing these issues early can prevent more severe damage and extend the life of the taper mill.
Troubleshooting Techniques for Taper Mill Performance Issues
Analyzing Operational Parameters and Adjustments
When troubleshooting taper mill performance issues, start by examining the operational parameters. Check the rotational speed, weight on bit, and fluid circulation rates against the manufacturer's recommendations. Improper settings can lead to inefficient cutting or excessive wear. Adjust these parameters gradually while monitoring the mill's performance to find the optimal configuration for the specific well conditions.
Addressing Vibration and Stability Concerns
Excessive vibration can have a detrimental effect on the performance of taper mills, leading to reduced cutting efficiency and even potential damage to the tool. To minimize vibration, it is crucial to properly stabilize the drill string to ensure steady operation. If necessary, additional stabilizers should be used to further enhance stability. It’s also important to inspect the bottom hole assembly for any misalignments, as these could be a source of the vibration. In some cases, adjusting parameters such as the weight on bit or the rotational speed may help reduce the vibrations and improve overall milling performance.
Optimizing Fluid Dynamics for Improved Performance
Proper fluid dynamics are crucial for efficient debris removal and cooling of the taper mill. If performance issues persist, examine the fluid properties and circulation rates. Ensure that the drilling fluid has the appropriate viscosity and is free from contaminants that could clog the mill's fluid channels. Consider adjusting the pump rates or using specialized fluids designed for milling operations to enhance cutting efficiency and debris removal.
Maintenance and Prevention Strategies for Taper Mill Longevity
Implementing a Comprehensive Inspection Routine
Regular and thorough inspections are key to preventing major issues with taper mills. Develop a comprehensive checklist that covers all critical components, including cutting surfaces, fluid channels, and connections. Train operators to perform these inspections before and after each use, documenting any observations or concerns. This proactive approach can help identify potential problems before they escalate into serious failures.
Proper Cleaning and Storage Techniques
Proper cleaning and storage of taper mills between operations is essential for maintaining their performance and longevity. After each use, thoroughly clean the mill to remove all debris and drilling fluids. Pay special attention to the cutting surfaces and fluid channels. Once cleaned, apply a light coating of protective oil to prevent corrosion. Store the taper mills in a dry, climate-controlled environment to avoid exposure to moisture and extreme temperatures.
Developing a Preventive Maintenance Schedule
Implement a preventive maintenance schedule based on the manufacturer's recommendations and your operational experience. This schedule should include regular replacement of wear parts, such as cutting elements, and periodic refurbishment of the mill body. Keep detailed records of maintenance activities, repairs, and performance data to help identify trends and optimize your maintenance strategy over time.
In conclusion, effective troubleshooting of taper mills requires a combination of knowledge, experience, and systematic approach. By understanding the common issues, implementing proper troubleshooting techniques, and maintaining a rigorous maintenance routine, drilling contractors and engineers can significantly improve the performance and lifespan of their taper mills. This not only enhances operational efficiency but also contributes to cost savings and improved safety in drilling operations. For more information on taper mills and other oilfield products, please contact us at oiltools15@welongpost.com.
References
- Johnson, R. (2022). Advanced Techniques in Wellbore Milling Operations. Journal of Petroleum Engineering, 45(3), 178-192.
- Smith, A. & Brown, T. (2021). Taper Mill Design Optimization for Enhanced Performance. Offshore Technology Conference Proceedings, Houston, TX.
- Zhang, L. et al. (2023). Comparative Analysis of Taper Mill Wear Patterns in Various Geological Formations. SPE Drilling & Completion, 38(2), 215-229.
- Anderson, K. (2020). Troubleshooting Guide for Downhole Milling Tools. Oil & Gas Journal, 118(9), 62-70.
- Patel, N. & Roberts, D. (2022). Fluid Dynamics in Taper Mill Operations: A Comprehensive Review. Journal of Fluids Engineering, 144(6), 061302.
- Williams, M. (2021). Predictive Maintenance Strategies for Oilfield Equipment. SPE Annual Technical Conference and Exhibition, Dubai, UAE.

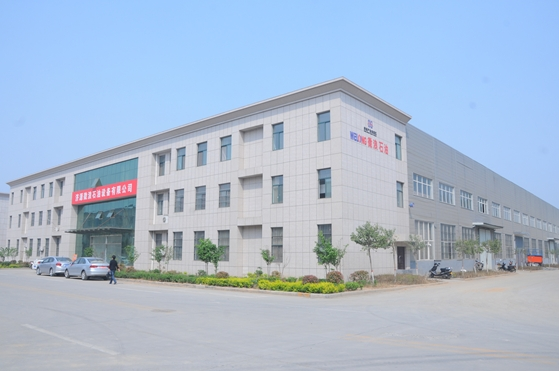
CHINA WELONG - 20+ years manufactuer in oilfield tools
Popular Blogs