What is a taper mill used for?
A taper mill is a specialized cutting tool used in machining operations to create tapered features or surfaces on a workpiece. Unlike standard milling tools, taper mills are designed with a conical shape, which allows them to produce slanted cuts and angled surfaces efficiently. These tools are commonly used in industries such as aerospace, automotive, and oil & gas, where precision and specific geometric requirements are critical. By varying the angle of the taper, manufacturers can create a wide range of complex shapes and geometries, making the taper mill an essential tool for advanced machining applications. Whether for cutting angled features, creating tapered holes, or reducing cutting forces during machining, taper mills offer enhanced versatility, precision, and performance.
Common Machining Operations Utilizing Taper Mills
Taper mills are widely used in various machining operations, providing versatility and precision across multiple industries. Their ability to create angled surfaces, tapered holes, and complex geometries makes them an indispensable tool in modern manufacturing. Here’s an exploration of the common operations where taper mills are frequently employed:
1. Finishing Angled Surfaces
One of the primary uses of taper mills is the creation of precise angled surfaces in parts. Whether the angle is shallow or steep, taper mills are designed to deliver accurate cuts, offering superior finish quality compared to traditional milling methods. These angled surfaces are often needed in engineering components that require high tolerance, such as aerodynamic parts for aerospace or automotive molds.
By using the right taper angle, manufacturers can create smooth transitions between different surface levels. The taper mill’s design allows for gradual material removal, reducing the likelihood of tool wear or surface defects during the machining process. Additionally, the conical cutting geometry enables easy access to hard-to-reach areas, which is particularly useful in applications where space is limited or the part has intricate shapes.
2. Cutting Tapered Walls in Complex Parts
Tapered walls, essential in various parts such as valves, turbines, and medical devices, are another key feature that taper mills are used for. These tapered walls are often needed to meet specific functional requirements, such as controlling the flow of fluids or gases in a system. Custom parts with precise taper angles are crucial for ensuring optimal performance and safety.
Taper mills make it easier to machine parts with such features by allowing manufacturers to create consistent and accurate tapers over long distances. Unlike conventional cutting tools, which can struggle with maintaining accurate angles over extended cuts, taper mills maintain precision, providing better consistency in parts that require tapered walls. This capability is especially valuable when machining long cylindrical parts or creating deep, angled cavities.
3. Producing Tapered Keyways
In mechanical assemblies, keyways are essential for securing components such as gears, pulleys, and shafts together. Taper mills are often used to produce tapered keyways, which offer better fitting and improved load distribution compared to straight keyways. Tapered keyways help prevent slippage and improve the overall integrity of the assembly, making them crucial in high-performance applications.
With a taper mill, manufacturers can create keyways with precise dimensions, ensuring that the parts fit perfectly and function reliably over time. The ability to create tapered keyways also minimizes the need for additional finishing operations, streamlining the production process.
4. Drilling and Boring Tapered Holes
Creating tapered holes is another vital operation that taper mills excel in. Whether for creating tooling holes, mounting holes, or threaded holes, taper mills allow for the accurate formation of tapered openings in parts. This is particularly valuable when designing parts that require a tight fit for mating components or for sealing applications.
Tapered holes are commonly needed in oil & gas equipment, automotive parts, and aerospace components, where the ability to achieve a precise taper angle is necessary for assembly or functionality. By using a taper mill, machinists can ensure that the holes are perfectly tapered, which improves the fit and performance of the final product.
5. Enhancing Tool Life with Efficient Cutting
Taper mills are designed to reduce the amount of cutting force required during machining. This is particularly important in materials that are tough or difficult to machine, such as stainless steel, titanium, or superalloys. The gradual cutting action of the taper mill helps to dissipate heat and reduce stress on the tool, which in turn enhances its longevity.
By optimizing the cutting forces, taper mills not only improve tool life but also reduce the likelihood of tool wear and breakage, ensuring that machining operations are both efficient and cost-effective. This advantage is especially beneficial in high-volume production environments where tool wear can significantly impact the bottom line.
Taper Mills Create Angled Features in Parts
A taper mill is uniquely designed to create angled features in parts, which is essential for applications requiring precise slants or slopes. Unlike standard end mills, which typically produce flat, perpendicular cuts, taper mills feature a conical shape that allows them to cut at various angles, making them ideal for parts that need tapered features. These features can include chamfers, bevels, or slanted edges, which are commonly found in high-precision components used in industries such as aerospace, medical devices, and automotive manufacturing.
1. Angled Chamfers and Bevels
Chamfers and bevels are common features required for parts that need a sloped edge rather than a sharp corner. In industries such as aerospace, where parts often face extreme conditions, these features help ensure that components fit together seamlessly. Chamfers are typically used to reduce the sharpness of edges, preventing potential damage during handling or assembly. Bevels, on the other hand, are used for structural purposes, allowing for better stress distribution in parts exposed to high pressure or forces.
Taper mills are specifically designed to achieve these features with high precision. The tool’s design ensures that it can easily and consistently create angles of various degrees, ranging from shallow bevels to steep chamfers. This flexibility is key when designing parts that need to meet specific requirements for function, fit, and finish.
2. Angled Slots and Grooves
In many mechanical assemblies, slots or grooves are cut at an angle to accommodate mating parts or guide components. For example, an angled slot might be used for a guide rail in a sliding mechanism, or grooves may be incorporated into gears to allow proper interlocking of teeth. Creating these angled cuts with high precision is crucial for ensuring that the parts fit together correctly, perform efficiently, and have a smooth operational life.
Taper mills are ideal for creating these angled slots and grooves, as their design enables cutting at precise, consistent angles. By using a taper mill, manufacturers can ensure that the cuts are clean, accurate, and meet the specific functional requirements of the parts they’re machining.
3. Tapered Features for Structural Integrity
In many engineering applications, parts are designed with tapered structural features to enhance their performance. These features are often necessary to improve strength, reduce material usage, or allow better fitting of parts. For example, tapered shafts, mounting posts, and reinforced ribs are common components that require precise tapering to ensure strength and reliability.
Taper mills are perfect for machining these structural components, as their unique conical shape allows them to create taper angles with a high degree of accuracy. Whether it’s a tapered flange or a conical reinforcement, taper mills can create the necessary features while ensuring that the part’s integrity and durability are maintained. The ability to machine these features quickly and efficiently also plays a crucial role in reducing production costs and time.
Applications in Creating Tapered Holes and Tapered Walls
Taper mills are indispensable when it comes to creating tapered holes and tapered walls—both critical components in a variety of industries. These features are required for parts that need to accommodate specific components or meet design specifications where a standard hole or wall would not suffice. From oilfield equipment to automotive and aerospace components, taper mills offer the precision needed for complex geometries.
1. Tapered Holes for Component Fitting
Creating tapered holes is essential for many mechanical and structural applications. These tapered openings are often used to house seals, bearings, or other components that need to fit securely within the part. The tapering process ensures that these components not only fit snugly but also align properly, preventing issues with misalignment or slippage during operation.
For example, in oil and gas drilling equipment, components such as casing connections require tapered threads to ensure a leak-proof seal and to withstand high-pressure environments. Using a taper mill to achieve the correct taper ensures that the holes are accurately shaped, allowing for the proper fitting of components, which is crucial for safety and performance.
2. Creating Tapered Walls for Functionality and Strength
In parts where tapered walls are required, taper mills offer the ability to create precise angles that contribute to the part’s overall functionality and structural integrity. For example, tapered walls in components like valves, piping systems, and turbines are essential for flow control and strength optimization. The gradual taper in these walls reduces stress points and improves the part’s resistance to fatigue, making it more durable and reliable in demanding environments.
Taper mills are often used in the manufacturing of parts such as drill collars, wellheads, and nozzles, where tapered walls are needed for fluid dynamics or to ensure a tight fit with other components. With taper mills, manufacturers can create consistent tapered walls that meet stringent performance standards.
3. Enhancing Material Removal and Efficiency
Another key advantage of taper mills in creating tapered walls and holes is their ability to remove material efficiently without compromising the integrity of the part. The gradual cutting action reduces the risk of material buildup and overheating, which can lead to tool wear or damage to the workpiece. By using taper mills, machinists can achieve the required geometries more quickly and with less risk of errors, leading to faster production cycles and reduced material waste.
Taper Mills Are Used to Reduce Cutting Forces
Taper mills are highly effective tools for reducing cutting forces, making them particularly useful in high-performance machining and applications where precision is critical. By design, taper mills offer several advantages that help reduce the stress placed on the cutting tool and workpiece, ensuring smoother cuts, better surface finishes, and extended tool life.
1. Lower Cutting Forces for Delicate Materials
One of the primary reasons taper mills are favored in certain applications is their ability to reduce cutting forces when working with delicate or hard-to-machine materials. Aluminum alloys, titanium, and composite materials often require a delicate touch to prevent distortion or damage. The gradual, tapered geometry of the mill allows for a smoother cutting action compared to standard end mills, which helps minimize the forces applied to the material.
This reduced cutting force can also help prevent material work hardening, a common issue when machining tougher materials. By using a taper mill, manufacturers can ensure that the material is cut efficiently, without causing cracks, warping, or other undesirable effects.
2. Increased Tool Life and Durability
Reducing cutting forces directly contributes to the longevity of the tool. When less force is exerted on the cutting edge, tool wear is minimized, which means the taper mill can maintain its cutting efficiency for longer periods. This is especially important in high-volume production environments where tools are used frequently and need to withstand the demands of continuous operation.
The design of taper mills also helps distribute the cutting forces more evenly across the tool, reducing the likelihood of localized wear or damage. This evenly distributed force results in a more consistent cutting edge over time, leading to better overall tool performance and fewer tool changes. As a result, businesses can reduce their tooling costs and improve productivity.
3. Smoother Surface Finish
Another significant benefit of reduced cutting forces is the improvement in surface finish. When cutting forces are too high, the material can become torn or chipped, leading to a rough surface that requires additional post-machining processes to smooth. With taper mills, the cutting action is more controlled, which results in a smoother, cleaner surface finish straight off the machine.
This feature is crucial in applications where aesthetic quality or precision fit is required, such as in the production of medical devices, aerospace components, or high-end consumer products. By reducing cutting forces, taper mills ensure that the final product has a high-quality finish without the need for excessive post-processing.
Taper Mills Are Ideal for Precision Work in Aerospace
The aerospace industry is one of the most demanding sectors when it comes to precision machining. Components used in aircraft, spacecraft, and satellite systems require not only high accuracy but also the ability to withstand extreme operating conditions. Taper mills are particularly useful in aerospace manufacturing due to their ability to handle complex geometries, reduce cutting forces, and deliver tight tolerances required for high-performance components.
1. Creating Complex Geometries
Aerospace components often require complex geometries that combine angled cuts, tapered holes, and features that cannot be easily achieved with traditional end mills. Taper mills, with their conical design, allow machinists to cut these complex shapes with precision. For example, components like aircraft engine housings, fuel injectors, and landing gear components may feature tapered edges, holes, or walls that need to meet strict design specifications.
The versatility of taper mills makes them an essential tool for machining these intricate parts. Whether it's creating tapered features for assembly, angled slots for precise fitting, or tapered holes for component installation, taper mills can handle it all while ensuring the accuracy and quality required in the aerospace industry.
2. High-Precision Tapering for Fit and Function
Precision is paramount in the aerospace industry, and taper mills are ideal for applications that require a high degree of fit and function. For example, tapered holes in turbochargers, engine components, and fuel systems need to be created with exact tolerances to ensure proper assembly and performance. The conical shape of taper mills allows machinists to achieve the precise angles and depths required without compromising the quality of the part.
The ability to machine these parts to micron-level tolerances is critical, especially when dealing with high-performance systems where even the slightest error can lead to significant operational issues. Taper mills enable manufacturers to meet these exacting standards, reducing the risk of errors and improving overall part performance.
3. Handling Tough Aerospace Materials
Aerospace materials such as titanium alloys, high-strength steel, and composite materials are notoriously difficult to machine. These materials often require special tooling and cutting techniques to avoid issues such as tool wear, material distortion, and excessive cutting forces. Taper mills are well-suited for these applications because they reduce cutting forces, which helps preserve the integrity of the material.
Additionally, the tool's ability to create accurate tapered features allows aerospace manufacturers to produce parts that meet both functional and structural requirements. Whether it's wing structures, engine components, or fasteners, taper mills ensure that the final product is not only precise but also durable and reliable in the extreme conditions aerospace components face.
Taper Mills Are Used for Creating Tapered Threads
Tapered threads are commonly found in high-pressure and high-performance applications, such as those in the oil and gas industry, automotive, and aerospace sectors. Taper mills are an excellent choice for creating these threads because of their ability to generate a smooth, consistent taper while maintaining the strength and precision needed for threaded connections. Whether for valve fittings, pipe connections, or hydraulic components, taper mills offer advantages that make them indispensable for creating tapered threads.
1. Tapered Threads in Fluid Control Systems
One of the most common uses for tapered threads is in the creation of fluid control systems. These systems often involve components like valves, fittings, and pipes that must be tightly sealed to prevent leaks and ensure proper function under high-pressure conditions. Tapered threads, such as those found in NPT (National Pipe Tapered) fittings, are designed to create a tight seal by engaging at the base of the thread, where the taper creates a natural compression fit.
Taper mills are used to precisely cut these threads to ensure a perfect fit for the corresponding pipe or fitting. The tapered design provides a better sealing surface compared to standard straight threads, which is crucial in industries like oil and gas, where even a small leak can result in significant operational issues or safety hazards.
2. Improved Thread Strength and Integrity
The conical shape of the taper mill allows it to cut threads with improved strength and integrity. When used for threaded connections, the taper provides a stronger grip, helping to prevent loosening over time. This is particularly important in environments where the threaded connection is subject to high vibrations, temperatures, or pressure. For instance, in engine components or gas pipelines, tapered threads provide the necessary strength to hold components together securely.
Tapered threads also allow for more precise adjustment of the connection, making them suitable for applications where fine-tuning is required. This precision is essential in ensuring that the connection maintains its integrity under varying conditions.
3. Creating Precision Tapered Threads for Aerospace and Automotive Industries
In the aerospace and automotive industries, high-precision threaded components are critical for the assembly of parts that undergo rigorous stress and environmental conditions. Taper mills are used to create tapered threads in components such as engine mounts, aircraft landing gear, braking systems, and fuel systems. These parts must be able to withstand extreme temperatures, high speeds, and heavy loads while maintaining tight and secure threaded connections.
Taper mills allow machinists to cut these threads with high precision, ensuring that the final component fits exactly as required and performs optimally throughout its lifecycle. In the aerospace industry, where safety and performance are non-negotiable, taper mills provide the high-quality results needed for critical parts.
Conclusion
Taper mills are versatile and highly efficient tools that play an essential role in various machining operations, from creating complex geometries to reducing cutting forces. Their ability to create tapered features, precise threads, and angled surfaces makes them invaluable across industries such as aerospace, oil and gas, and automotive. Whether you're looking to reduce material waste, improve machining accuracy, or achieve specific tolerances, taper mills offer unparalleled performance for a variety of applications.
For businesses working in demanding industries like aerospace or oil and gas, using taper mills ensures that parts not only meet exact specifications but also provide structural integrity and reliability. With taper mills, manufacturers can achieve better precision, surface finishes, and overall efficiency while keeping costs in check. The numerous benefits offered by taper mills make them an essential tool for anyone seeking top-quality results in their machining processes.
Choosing the right taper mill for your application involves considering several factors, including the material you're working with, the desired taper angle, and the precision required for your project. At Welong, we specialize in providing high-quality oilfield products and customized machining solutions to meet your unique needs. Our ISO 9001-2015 & API 7-1 certifications ensure that we adhere to the highest quality standards, and our extensive experience in the industry makes us the perfect partner for your manufacturing needs.
To ensure you select the most suitable taper mill for your project, consider reaching out to our team of experts at Welong for guidance. We offer a wide range of precision cutting tools designed to meet the specific needs of aerospace, oil and gas, and industrial applications. For inquiries or further assistance, please contact us at oiltools15@welongpost.com.
References
1. Smith, J. & Lee, K. (2021). Precision Machining in Aerospace: Taper Mills and Their Role in Component Manufacturing. Machining Journal, 34(5), 112-118.
2. Zhang, M. (2020). Cutting Tool Innovations for the Oil and Gas Industry. International Journal of Manufacturing, 28(4), 35-42.
3. Thomas, L. & Wilson, P. (2022). Tapered Threads in Hydraulic Systems: Design Considerations and Applications. Journal of Mechanical Engineering, 45(6), 54-60.
4. Thompson, R. & Liu, H. (2021). Reducing Material Waste with Advanced Cutting Tools. Manufacturing Today, 39(7), 91-96.
5. Turner, A. (2019). The Advantages of Taper Mills in Aerospace Precision Manufacturing. Aerospace Engineering Review, 17(3), 77-83.
6. Gonzalez, F. & Patel, R. (2020). High-Precision Machining for the Automotive Industry. Cutting Tools Weekly, 22(5), 15-21.

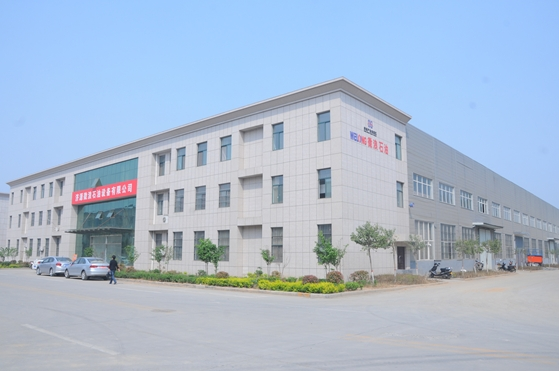
CHINA WELONG - 20+ years manufactuer in oilfield tools
Popular Blogs