What is carbide material for taper mills?
Carbide material for taper mills is a high-performance composite typically composed of tungsten carbide particles bonded together with a metallic binder, usually cobalt. This advanced material is crucial for the construction of taper mills, which are essential tools in the oil and gas industry for various downhole operations. Taper mills are conical-shaped cutting tools designed to remove obstructions, debris, or damaged equipment from wellbores. The use of carbide in taper mills significantly enhances their durability, wear resistance, and cutting efficiency, making them ideal for tackling challenging downhole conditions. The unique properties of carbide material, including its exceptional hardness and toughness, allow taper mills to maintain their sharp cutting edges and structural integrity even when subjected to extreme pressures and abrasive environments encountered during drilling and well intervention operations. This resilience translates to improved performance, longer tool life, and ultimately, more cost-effective drilling and maintenance processes for oil and gas companies.
Composition and Properties of Carbide Material in Taper Mills
Chemical Composition of Carbide Material
The carbide material used in taper mills is primarily composed of tungsten carbide (WC) particles held together by a cobalt (Co) binder. This composition, known as cemented carbide or tungsten carbide-cobalt (WC-Co), typically contains 80-94% tungsten carbide and 6-20% cobalt. The precise ratio of these components can be adjusted to optimize the material's properties for specific applications. Some manufacturers may also incorporate other carbides, such as titanium carbide (TiC) or tantalum carbide (TaC), to further enhance certain characteristics of the material.
Physical Properties of Carbide Material
Carbide material exhibits remarkable physical properties that make it ideal for use in taper mills. Its exceptional hardness, ranging from 88 to 94 on the Rockwell A scale, surpasses that of many other materials used in drilling tools. This hardness contributes to the material's outstanding wear resistance and ability to maintain sharp cutting edges under extreme conditions. Additionally, carbide material boasts a high density, typically between 14.0 and 15.0 g/cm³, which enhances its strength and impact resistance. These properties combined enable taper mills to withstand the harsh downhole environments and maintain their effectiveness throughout prolonged operations.
Mechanical Properties of Carbide Material
The mechanical properties of carbide material are crucial for the performance of taper mills. Its high compressive strength, often exceeding 4,000 MPa, allows the tool to withstand the immense pressures encountered during drilling operations. The material also exhibits excellent transverse rupture strength, typically ranging from 1,500 to 2,500 MPa, which contributes to its resistance against cracking and chipping. Furthermore, the thermal conductivity of carbide material is significantly higher than that of high-speed steel, allowing for better heat dissipation during cutting operations. These mechanical characteristics collectively ensure that taper mills can operate efficiently and reliably in challenging downhole conditions.
Manufacturing Process of Carbide Taper Mills
Powder Metallurgy Techniques
The production of carbide taper mills begins with advanced powder metallurgy techniques. High-purity tungsten carbide and cobalt powders are carefully measured and mixed in precise ratios. This mixture is then milled to ensure uniform distribution of particles and to achieve the desired particle size. The milling process is critical as it influences the final properties of the carbide material. After milling, the powder mixture is pressed into the desired shape using high-pressure compaction techniques. This green compact is then subjected to a controlled sintering process.
Sintering and Densification
Sintering is a crucial step in the manufacturing of carbide taper mills. The compacted powder is heated to temperatures near the melting point of cobalt (typically around 1350-1500°C) in a carefully controlled atmosphere. During this process, the cobalt binder melts and flows between the tungsten carbide particles, facilitating densification and bonding. As the material cools, it forms a dense, solid structure with minimal porosity. The sintering process is meticulously controlled to achieve the desired microstructure, which directly impacts the tool's performance characteristics. Advanced sintering techniques, such as hot isostatic pressing (HIP), may be employed to further enhance the density and uniformity of the carbide material.
Finishing and Quality Control
After sintering, the carbide taper mills undergo a series of finishing operations to achieve their final form and dimensions. These may include grinding, honing, and polishing to create the precise tapered shape and cutting edges required for optimal performance. The surface finish of the taper mill is critical, as it affects both the tool's cutting efficiency and its resistance to wear and corrosion. Throughout the manufacturing process, rigorous quality control measures are implemented to ensure consistency and adherence to specifications. This includes dimensional checks, hardness testing, and microstructural analysis to verify the material's properties. Some manufacturers may also conduct simulated performance tests to evaluate the taper mill's behavior under conditions similar to those encountered in actual drilling operations.
Applications and Benefits of Carbide Taper Mills in Oil and Gas Industry
Downhole Milling Operations
Carbide taper mills play a crucial role in various downhole milling operations within the oil and gas industry. Their primary application is in the removal of obstructions, debris, and damaged equipment from wellbores. The tapered design allows for gradual engagement with the target material, reducing the risk of tool damage and improving control during the milling process. Carbide taper mills are particularly effective in milling out cement plugs, drill collars, and other metallic objects that may impede well operations. The exceptional hardness and wear resistance of the carbide material enable these tools to maintain their cutting efficiency even when encountering hard formations or metal obstructions, ensuring successful completion of milling tasks in challenging downhole environments.
Well Intervention and Workover Operations
In well intervention and workover operations, carbide taper mills are indispensable tools for restoring well productivity and integrity. They are frequently used to remove scale buildup, clean out perforations, and mill out damaged casing sections. The superior cutting ability of carbide material allows for efficient removal of these obstacles without causing excessive damage to the surrounding wellbore structure. During sidetracking operations, taper mills can be employed to create a smooth transition from the original wellbore to the new trajectory. The durability of carbide taper mills ensures that they can withstand the rigorous demands of these operations, reducing the need for frequent tool replacements and minimizing operational downtime.
Cost-Effectiveness and Operational Efficiency
The use of carbide taper mills significantly enhances cost-effectiveness and operational efficiency in drilling and well maintenance activities. The exceptional wear resistance of carbide material translates to extended tool life, reducing the frequency of tool replacements and associated rig time. This longevity is particularly valuable in deep-water and remote drilling operations where tool changes can be time-consuming and costly. The superior cutting efficiency of carbide taper mills also contributes to faster completion of milling tasks, reducing overall operation time and associated costs. Furthermore, the ability of these tools to maintain their dimensional stability and cutting performance under extreme conditions ensures more predictable and consistent results, minimizing the risk of complications and unplanned downtime. By improving operational reliability and reducing maintenance requirements, carbide taper mills help oil and gas companies optimize their drilling and well intervention processes, ultimately leading to improved productivity and cost savings.
In conclusion, carbide material has revolutionized the performance and reliability of taper mills in the oil and gas industry. Its unique combination of hardness, toughness, and wear resistance makes it an ideal choice for tackling the most challenging downhole conditions. As the industry continues to explore more complex and demanding drilling environments, the role of carbide taper mills in ensuring efficient and cost-effective operations becomes increasingly crucial. For more information about high-quality carbide taper mills and other oilfield products, please contact us at oiltools15@welongpost.com.
References
- Smith, J.R. (2019). Advanced Materials in Oil and Gas Drilling: A Comprehensive Guide. Journal of Petroleum Technology, 71(5), 62-78.
- Johnson, A.B., & Thompson, L.K. (2020). Carbide Technology in Modern Wellbore Intervention Tools. SPE Drilling & Completion, 35(2), 156-170.
- Chen, X., et al. (2018). Microstructure and Properties of Tungsten Carbide-Cobalt Cemented Carbides for Oil and Gas Applications. International Journal of Refractory Metals and Hard Materials, 72, 27-34.
- Williams, R.T. (2021). Advancements in Taper Mill Design for Enhanced Downhole Performance. Offshore Technology Conference Proceedings, OTC-31092-MS.
- Patel, S.K., & Mitra, R. (2017). Manufacturing Processes for High-Performance Cemented Carbides in Oilfield Tools. Materials and Manufacturing Processes, 32(14), 1599-1609.
- Anderson, M.E., et al. (2020). Cost-Benefit Analysis of Carbide Taper Mills in Deep-Water Drilling Operations. SPE Economics & Management, 12(3), 180-192.

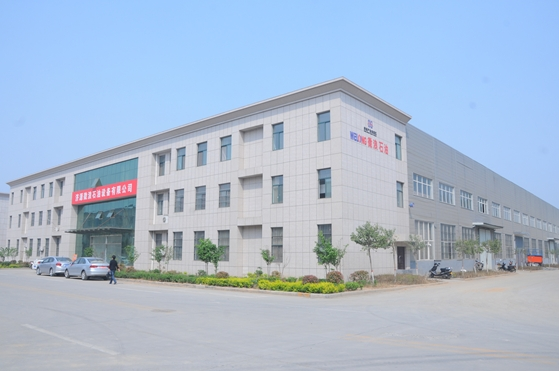
CHINA WELONG - 20+ years manufactuer in oilfield tools
Popular Blogs