How do I choose the suitable taper mill for my application?
Choosing the right taper mill for your application is critical to ensuring the efficiency, precision, and cost-effectiveness of your machining process. The taper mill, designed with a conical cutting edge, plays a vital role in applications requiring precise contouring, chamfering, and tapered hole machining. To select the right taper mill, you must first consider the material to be machined, the specific geometry of the taper needed, and the machine tool capabilities available. Other factors like coating, flute design, and the helix angle also influence the choice of the taper mill.
Typically, a tapered end mill with a small helix angle works well for lighter cuts and finer details, while a steeper angle offers better chip removal and is ideal for roughing operations. Additionally, understanding the rigidity of your machine and the type of material you are working with will guide your decision on the proper taper mill dimensions, coating types, and flute geometry.
What is a Tapered End Mill, and How Does it Work?
A tapered end mill is a type of cutting tool that features a conical shape, with its cutting edge gradually decreasing in diameter from the shank to the tip. This taper is typically used for applications that require angled or contoured cuts. The taper mill can be used for both face milling and side milling, making it versatile for a range of machining operations. The cutting edges are designed to cut at varying depths along the length of the tool, allowing for effective material removal in applications such as machining angled surfaces or creating specific geometric features.
The design of a taper mill can vary, with options available for different taper angles, flute counts, and coatings to suit the material being worked on. The cutting action is achieved by rotating the mill at high speeds, with the tool gradually moving along the material surface. A key feature of the taper mill is its ability to perform both axial and radial cuts, offering precision in parts that require a tapered or angled finish.
Taper mills are used in a variety of industries, including aerospace, automotive, and oil and gas drilling, for applications ranging from mold making to creating keyways or undercuts. Understanding the workings of the taper mill and its different configurations can help you choose the best tool for your specific needs.
Benefits of Using a Tapered End Mill
Tapered end mills offer several significant benefits that make them indispensable in various machining processes. One of the primary advantages is their ability to machine angled or tapered features in a single pass, which eliminates the need for multiple operations. This versatility makes taper mills an efficient tool for tasks like creating drafts on molded parts, machining undercuts, or forming specific chamfer angles on components.
1. Precision and Versatility
Tapered end mills are designed to handle precise machining of angled surfaces, ensuring high-quality finishes with tight tolerances. Their versatility allows them to work on a wide range of materials, from soft metals like aluminum to harder materials such as stainless steel and titanium. Additionally, taper mills can be used in both milling machines and CNC equipment, making them adaptable to various machine setups and production environments.
2. Improved Tool Life and Reduced Tool Changes
Because taper mills can perform complex cuts in one pass, they reduce the need for multiple tool changes. This not only speeds up the machining process but also extends the tool life since fewer tools are being used in the overall process. Furthermore, many taper mills come with specialized coatings that improve wear resistance, reduce heat buildup, and extend the service life of the tool.
3. Better Chip Control and Surface Finish
A tapered end mill's geometry allows for superior chip removal and better control over the cutting process. The design of the taper and flute angles helps to prevent material from clinging to the cutting surface, reducing the chances of tool clogging and allowing for a smoother, cleaner finish. As a result, taper mills are ideal for achieving high-quality surface finishes, particularly in intricate parts where surface imperfections are not acceptable.
4. Ability to Reach Deep or Restricted Areas
In complex machining tasks, especially those involving deep cavities or confined spaces, taper mills shine due to their ability to reach areas that are otherwise difficult to access with standard tools. This is particularly useful in industries like aerospace, where precision and the ability to work within tight spaces are paramount.
With these benefits, tapered end mills are an excellent choice for many industries requiring precision and efficiency, including the oil and gas drilling sector, where complex part geometries are often required.
Types of Material Suitable for Tapered End Mills
Choosing the right material for a tapered end mill is crucial for achieving the desired results in your machining processes. The material of the taper mill directly impacts its performance, longevity, and suitability for specific applications. Different types of materials are suited for various operations depending on the hardness, abrasiveness, and thermal stability needed. Below are the most common materials used for taper mills, along with their benefits and ideal applications.
1. High-Speed Steel (HSS)
High-speed steel (HSS) is a widely used material for taper mills because of its excellent toughness, wear resistance, and ability to withstand high temperatures. HSS taper mills are often chosen for general-purpose machining operations and are effective for cutting softer metals, such as aluminum, brass, and copper. While not as durable as carbide, HSS taper mills offer a lower upfront cost and can be used for a variety of materials, making them a great option for workshops with less specialized needs.
2. Carbide
Carbide is a popular choice for taper mills due to its superior hardness, high wear resistance, and ability to withstand extreme temperatures. Carbide taper mills can maintain sharpness for longer periods, making them ideal for high-speed machining and applications involving harder materials, such as stainless steel, titanium, and nickel alloys. Carbide taper mills are particularly effective when high precision and long tool life are required. However, they are more brittle compared to HSS, which means they are less forgiving when subjected to excessive stress or shock.
3. Cobalt
Cobalt taper mills, a subcategory of HSS, are known for their enhanced wear resistance and ability to operate at higher temperatures. These taper mills are a good choice for applications where HSS might not perform adequately, such as in the machining of hardened steels, cast iron, and high-temperature alloys. Cobalt’s ability to resist heat and wear makes it an ideal material for demanding machining conditions in industries like aerospace and oil and gas drilling.
4. Ceramic
Ceramic taper mills are used in applications that require extreme hardness and wear resistance. They are typically employed in the machining of very hard materials, such as hardened tool steels, cast iron, and composites. Ceramic mills are capable of maintaining sharp cutting edges at high temperatures, but they are more fragile and require careful handling. These mills are often used for specific high-performance tasks, such as in the aerospace industry, where precision in hard materials is paramount.
5. Polycrystalline Diamond (PCD)
Polycrystalline diamond (PCD) taper mills are among the hardest tools available and are used primarily for machining non-ferrous metals, composite materials, and abrasive materials like carbon fiber and fiberglass. The primary advantage of PCD taper mills is their ability to provide an exceptionally smooth finish and withstand extreme wear, making them ideal for industries such as automotive, electronics, and semiconductor manufacturing. Although expensive, PCD taper mills offer unrivaled performance in certain high-precision applications.
Choosing the right material for your taper mill depends on the specifics of your machining project, including the material being machined, the required precision, and the operating conditions. Selecting the appropriate taper mill material will not only improve the efficiency of the process but also enhance the tool's lifespan and the quality of the finished product.
Effects of Coatings on Tapered End Mill Performance
The coatings applied to tapered end mills play a critical role in enhancing their performance, durability, and ability to withstand challenging machining conditions. These coatings are designed to reduce wear, lower friction, improve heat resistance, and increase the tool's overall life. Depending on the material being cut and the type of operation, the right coating can make a significant difference in the machining process.
1. Improved Wear Resistance
One of the most significant benefits of coatings is enhanced wear resistance. Coatings such as Titanium Nitride (TiN) or Titanium Aluminum Nitride (TiAlN) increase the hardness of the taper mill's surface, which helps to prevent premature tool wear caused by abrasive materials. In industries like oil and gas drilling, where hard metals and composites are often machined, coatings help maintain the tool’s cutting efficiency over extended periods.
2. Heat Resistance and Reduced Friction
Certain coatings, such as TiAlN and Diamond-Like Carbon (DLC), are designed to withstand extreme heat conditions. These coatings help to dissipate heat generated during high-speed machining, reducing the risk of tool failure due to thermal stress. In addition to heat resistance, coatings like TiN help lower friction between the taper mill and the material being cut, allowing for smoother cuts and reduced wear. The ability to maintain cutting performance at higher speeds translates to improved productivity and better surface finishes.
3. Enhanced Surface Finish and Chip Removal
Coatings can also enhance the quality of the surface finish and aid in chip removal. For example, coatings such as PVD (Physical Vapor Deposition) provide a smooth surface on the taper mill, reducing friction and allowing for more efficient chip evacuation. This is particularly important when machining materials like stainless steel and titanium, which can produce sticky chips. A smoother surface also ensures a better finish on the workpiece, which is crucial for industries requiring high-quality surfaces, such as aerospace and automotive manufacturing.
4. Corrosion Resistance
In industries where the milling process involves exposure to moisture or chemicals, such as marine, oil, and gas sectors, coatings like TiCN (Titanium Carbonitride) and other corrosion-resistant materials are essential. These coatings protect the taper mill from rust and corrosion, thus extending the tool's lifespan and reducing the frequency of tool changes. Corrosion resistance is particularly important when working with materials that are prone to chemical reactions, such as aluminum alloys and certain steels.
5. Cost-Efficiency Over Time
While coated taper mills often come at a higher initial cost, they can offer substantial savings in the long run due to their extended tool life and improved performance. By reducing tool wear and the need for frequent tool replacements, coating taper mills contribute to lowering overall machining costs. Additionally, coated tools allow for faster cutting speeds, which leads to increased production rates and more efficient machining.
When selecting a tapered end mill coating, it’s important to consider the specific requirements of your application. Factors such as the material being machined, the cutting speed, and the type of environment (dry, wet, or high-temperature) all influence the choice of coating. By selecting the right coating for your taper mill, you can optimize its performance and achieve better results while reducing operational costs.
Considering Flute and Helix Geometry of Taper Mill
The flute and helix geometry of a tapered end mill significantly influence its cutting performance, chip removal efficiency, and overall surface finish. Understanding the impact of these features on your taper mill is essential for selecting the right tool for your specific application. Let’s take a closer look at how flute design and helix angles can affect the efficiency and quality of your machining processes.
1. Flute Design and Its Impact on Cutting Performance
The flute design of a tapered end mill refers to the grooves or channels that run along the tool’s length, which facilitate the removal of chips from the cutting area. The number of flutes and their configuration play a key role in determining the cutting speed and the type of finish achieved. Common flute numbers range from 2 to 4 or more, with each offering distinct advantages depending on the material being machined and the specific task.
Two-Flute Tapered End Mills: These are ideal for applications that require fast chip removal and deep cuts. With fewer flutes, there is more space for the chips to evacuate, reducing the risk of clogging. This design is especially useful when working with softer materials like aluminum or when high material removal rates are needed.
Three- or Four-Flute Tapered End Mills: These mills offer better surface finishes and are preferred for precision work or when cutting harder materials like stainless steel or titanium. The additional flutes provide more cutting edges, which results in smoother cuts and better control over the machining process. However, with more flutes, chip removal becomes more challenging, so they may not be ideal for deep cuts in softer materials.
2. Helix Angle and Its Effect on Cutting Efficiency
The helix angle of the tapered end mill refers to the angle at which the flutes are twisted along the tool’s length. The helix angle plays a crucial role in the tool’s ability to cut effectively and evacuate chips from the cutting zone. Typically, helix angles range from 15° to 45°, with different angles offering various advantages depending on the application.
Low Helix Angles (15° - 30°): These angles are often used in roughing operations, where higher radial forces are required for efficient material removal. A lower helix angle allows for more aggressive cuts, making it suitable for heavy-duty operations where the material is being removed rapidly. The lower angle also results in less heat buildup, improving tool life during prolonged machining.
High Helix Angles (30° - 45°): High helix angles are preferred for finishing operations where precision and surface finish are paramount. The increased angle provides smoother cuts and a more gradual entry into the material, leading to a cleaner finish. High helix angles are especially effective in cutting harder materials, such as tool steels and alloys, because they help to distribute the cutting forces more evenly across the tool.
3. Balancing Flute Design and Helix Angle for Optimal Performance
When selecting the right taper mill for your application, it’s essential to balance the flute design and helix angle to meet the specific needs of your machining task. For example, if you are performing light finishing cuts in hard materials, a taper mill with a higher helix angle and more flutes will give you a better surface finish. On the other hand, if you are working with softer materials or need to remove material quickly, a tool with a lower helix angle and fewer flutes may be more effective.
Additionally, considering the rigidity and stability of your machine tool is important. High helix angles can be more sensitive to vibrations and may require a machine with higher rigidity to achieve optimal results. For deeper cuts, a more robust flute design with fewer flutes can help in managing chip removal more effectively.
By understanding how flute and helix geometries influence cutting performance, you can select a tapered end mill that will improve both the efficiency of your process and the quality of your finished parts.
How to Optimize Tapered End Mill Performance for Different Conditions?
Optimizing the performance of a tapered end mill is essential for maximizing efficiency, tool life, and overall machining quality. Several factors, such as cutting conditions, material properties, and tool settings, must be carefully considered to achieve the best results. Below are some key considerations to optimize taper mill performance for various applications.
1. Adjusting Cutting Speeds and Feeds
One of the most effective ways to optimize taper mill performance is by adjusting the cutting speeds and feeds. The cutting speed refers to the speed at which the tool moves through the material, while the feed rate determines how fast the material is fed into the tool. Both factors directly affect the surface finish, tool wear, and material removal rate.
For harder materials like titanium, stainless steel, and nickel alloys, it's essential to reduce the cutting speed to prevent excessive heat buildup, which could lead to premature tool wear. Slower feed rates will help manage the forces exerted on the tool and reduce the risk of damaging the tapered end mill.
For softer materials like aluminum, brass, and plastic, higher cutting speeds and feed rates can be used to increase material removal rates. However, it's still crucial to maintain a balance to avoid vibration, which could compromise the surface finish.
2. Maintaining Proper Coolant and Lubrication
The use of coolant or lubrication is critical in maintaining the temperature stability of the taper mill during machining. Coolants help reduce heat buildup, flush away chips, and prevent the tool from overheating, which can lead to faster wear. There are different types of coolants to choose from, such as flood coolant, mist coolant, or air blast, depending on the application and material being machined.
Flood coolant is often used for high-speed machining of harder metals, as it provides continuous cooling to prevent heat distortion and protect the tool from excessive wear.
Mist coolant or air blast may be preferable when machining softer materials, as it helps with chip removal and reduces the risk of clogging in the flutes.
In some cases, dry machining can be used, particularly when working with materials that are sensitive to coolant contamination. In these situations, selecting a tool with a coating that can handle high temperatures and friction is essential.
3. Ensuring Proper Tool Alignment and Stability
The rigidity and alignment of your machine tool are crucial factors in optimizing taper mill performance. If the machine lacks rigidity or proper alignment, it can lead to vibrations during machining, which can result in poor surface finishes, increased tool wear, and inaccurate cuts. Ensuring the machine is stable and that the taper mill is properly aligned will help achieve smoother, more precise cuts.
Additionally, the toolholder and clamping system should be checked to ensure that the taper mill is securely held in place, minimizing movement during cutting. Vibration-damping systems and high-precision toolholders can help further reduce the risk of tool deflection and improve the overall machining process.
4. Choosing the Right Tool Path and Strategy
Selecting the appropriate cutting strategy and tool path is essential for optimizing taper mill performance. For example, using a climb milling approach, where the tool rotates in the direction of the feed, can reduce cutting forces and result in a smoother finish. Alternatively, conventional milling, where the tool rotates against the direction of the feed, can provide better results for certain types of materials, especially when surface finish is critical.
5. Regular Tool Maintenance and Inspection
Regular maintenance and inspection of the tapered end mill are vital to ensuring consistent performance. Inspecting the tool for signs of wear, such as chipped or dull cutting edges, helps identify when a tool change is necessary. Additionally, keeping track of the number of machining hours and operational conditions can help schedule tool changes before tool failure occurs.
For extended tool life, performing regular tool reconditioning or sharpening can improve cutting performance and reduce the need for frequent tool replacements. Reconditioning is particularly useful for taper mills with high-quality coatings, as it can restore the tool's cutting edge without compromising its performance.
Conclusion
Choosing the right taper mill for your application involves understanding several key factors, including material type, tool geometry, coating selection, and machining conditions. By selecting the optimal taper mill based on these criteria and optimizing cutting parameters such as speed, feed, and lubrication, you can achieve higher productivity, improved surface finishes, and longer tool life. Implementing the correct maintenance practices also ensures that your taper mills continue to perform at their best, reducing operational costs in the long run.
When selecting a taper mill, it’s essential to work with a reliable supplier who can provide high-quality tools tailored to your specific needs. WELONG is your trusted partner in supplying premium oilfield and customized products, including high-performance taper mills for a variety of machining applications. To learn more about how we can help optimize your machining operations, contact us at oiltools15@welongpost.com.
References
1. Choudhury, I. A., & Choudhury, R. (2017). "Selection of appropriate taper mill for machining applications." International Journal of Advanced Manufacturing Technology, 88(5-8), 1899-1910.
2. Li, W., & Xu, H. (2015). "Factors influencing the choice of taper mills in precision machining." Journal of Materials Processing Technology, 220, 58-64.
3. Jain, P., & Agrawal, R. (2018). "Understanding the selection criteria for taper milling cutters in CNC applications." Procedia CIRP, 70, 333-337.
4. Xu, L., & Huang, Z. (2016). "A study on the optimal taper mill design for high-performance machining." International Journal of Machine Tools and Manufacture, 102, 42-49.
5. Wang, S., & Zhang, X. (2019). "Effect of taper angle on the performance of taper mills for complex part manufacturing." Journal of Manufacturing Science and Engineering, 141(6), 061012.
6. Lee, C., & Park, H. (2020). "Optimal selection of taper mills based on material and machining conditions." Materials and Manufacturing Processes, 35(9), 1021-1029.

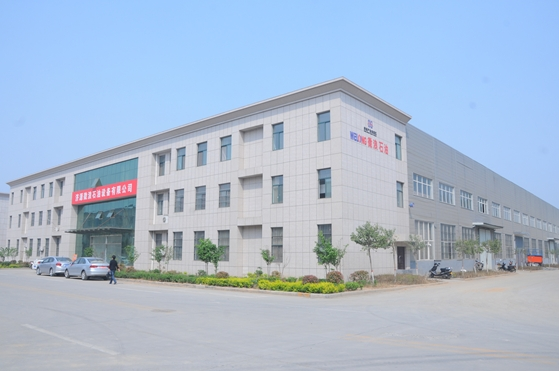
CHINA WELONG - 20+ years manufactuer in oilfield tools
Popular Blogs