What are the functions of Float Shoe?
A Float Shoe is a crucial tool in the oil and gas drilling process, serving several key functions that contribute to the overall efficiency and safety of drilling operations. Primarily, a float shoe is installed at the bottom of a casing string and features a one-way valve (check valve) that prevents backflow of fluids from the well. Its main function is to prevent fluid migration, allow for accurate cementing, and protect the well integrity by maintaining pressure control. This vital component ensures that drilling operations remain efficient, secure, and well-managed throughout the process.
Float shoes are essential for both the installation of well casings and the cementing process. They ensure that the casing is properly anchored and that the drilling fluid doesn’t flow backward into the wellbore. The Float Shoe also plays a vital role in controlling pressure during drilling and in preventing fluid loss into the formation, helping maintain the well’s pressure balance.
In the following sections, we will explore the specific functions of the Float Shoe in detail and discuss its role in various drilling applications.
How Does a Float Shoe Prevent Backflow?
The primary function of a Float Shoe is to prevent backflow, which is critical during the drilling and cementing process. Backflow, also known as reverse flow, can occur when drilling fluids or other wellbore fluids move in the wrong direction, leading to contamination, loss of pressure, or even damage to the well structure. The Float Shoe addresses this problem effectively by utilizing a built-in check valve.
When the Float Shoe is properly installed at the bottom of the casing string, the check valve allows fluid to flow into the casing but prevents the reverse flow of fluid back into the wellbore. This one-way valve mechanism is designed to function automatically under pressure. It opens during the pumping of cement or drilling fluids, allowing these fluids to enter the casing. However, when the pressure is reduced or when the pumping stops, the check valve closes tightly, creating a seal that prevents the backflow of fluids back into the well.
This prevention of backflow is critical for several reasons:
Well Integrity: Maintaining the integrity of the well is essential for safe and efficient operations. If drilling fluids were to flow backward, they could compromise the well structure, leading to potential leaks, contamination of surrounding formations, or pressure loss.
Cementing Efficiency: During the cementing process, it is crucial that the cement remains in place while it sets. If backflow occurs, it could disrupt the cementing job, causing poor bonding and leading to possible gaps that could affect well performance.
Pressure Control: Backflow could lead to a sudden loss of pressure in the wellbore, causing instability. By preventing backflow, the Float Shoe helps maintain a stable pressure environment, which is crucial for controlling the drilling process and avoiding potential blowouts or other hazardous situations.
The float valve in the Float Shoe is typically made from high-strength materials designed to withstand the harsh conditions found in oil and gas wells. These materials include high-grade alloys and composites that resist corrosion and wear over time, ensuring the valve remains operational throughout the life of the well.
Advanced Float Shoe Features for Backflow Prevention While the standard Float Shoe is effective at preventing backflow, modern variations of the tool come with advanced features to further improve its performance:
Pressure-activated Check Valves: These advanced float shoes have check valves that are activated by the pressure exerted on the wellbore. This ensures that the valve closes automatically when pressure from the casing is released, further reducing the risk of accidental backflow.
Enhanced Seal Design: Some float shoes incorporate double sealing systems, ensuring a stronger and more secure seal that reduces the chances of fluid leakage and backflow.
Corrosion-Resistant Coatings: To enhance durability and performance in challenging environments, many float shoes are coated with special corrosion-resistant materials. This extends the lifespan of the shoe and ensures that it continues to function effectively, even in harsh offshore or deep-well drilling environments.
Preventing backflow is just one aspect of the Float Shoe's function. This simple yet effective tool plays a key role in maintaining the safety, efficiency, and integrity of drilling operations. By preventing backflow, the Float Shoe helps ensure that fluid migration does not compromise the well, the cementing job is completed successfully, and the well’s pressure is properly controlled.
What Role Does a Float Shoe Play in Cementing?
In drilling operations, the Float Shoe plays a critical role during the cementing process, ensuring the successful placement of cement around the casing to create a strong and stable wellbore. Cementing is vital to securing the casing in place and isolating different zones of the wellbore to prevent unwanted fluid migration. Without a reliable method to control the flow of cement, the integrity of the well could be compromised, leading to operational failures or safety risks.
The Float Shoe serves as a key component in the overall cementing system by controlling the cement’s flow and ensuring the casing remains properly placed while the cement cures. Here's how it functions in the cementing process:
1. Controlled Cement Placement
The Float Shoe is designed to allow cement to flow into the casing when it is pumped during the cementing operation. Its check valve, however, prevents backflow once the cementing operation has finished. This ensures that the cement remains in place within the casing, effectively bonding the casing to the formation and preventing fluid migration behind the casing. Without the Float Shoe, cement would be free to flow back out of the casing, disrupting the entire cementing job and leading to weak zones in the wellbore.
Proper cement placement is essential for several reasons:
(1) Isolation of Formations
(2) Support and Strength
(3) Prevention of Wellbore Damage
2. Pressure Management During Cementing
The Float Shoe helps manage pressure during the cementing operation. As the cement is pumped into the casing, it displaces the drilling fluid, which can create an increase in pressure. The Float Shoe’s check valve allows the pressure to remain steady by preventing the backflow of cement, which helps maintain optimal pressure conditions in the wellbore. By controlling the pressure in the system, the Float Shoe ensures that the cement fills the casing uniformly and sets properly.
If pressure were to build up too quickly or unevenly during cement placement, it could lead to a phenomenon known as lost circulation, where the cement leaks into porous rock formations instead of staying inside the casing. The Float Shoe prevents this by regulating the pressure and preventing the escape of the cement slurry.
3. Ensuring Effective Primary Cementing
Primary cementing refers to the initial cement job performed after casing is installed. The success of this operation is critical, as it determines the well's integrity and safety for future drilling. If the cement job fails due to improper flow control, the entire well may be compromised.
Here’s where the Float Shoe makes a significant difference. The shoe’s ability to prevent backflow and ensure that cement stays in place provides the foundation for a successful primary cementing operation. It essentially acts as a sealant, allowing cement to be pumped into the casing and setting it in place while preventing any unwanted flow of fluid. This helps create a permanent seal that enhances the well’s stability and minimizes the risk of leakage over the long term.
4. Float Shoe Variations for Cementing Efficiency
There are various Float Shoe designs available, each optimized for different cementing conditions:
Single-Check Valve Float Shoes: These are the most common, featuring one check valve that prevents backflow during cementing. They are effective in most standard cementing operations.
Double-Check Valve Float Shoes: For more challenging conditions, such as high-pressure or high-temperature environments, a double-check valve design may be used. This provides an extra layer of protection, ensuring that backflow is prevented even in extreme conditions.
Enhanced Flow Control Shoes: Some float shoes come with advanced flow control features, such as adjustable valve settings or larger flow paths, which can accommodate higher cement volumes and pressures. These are used in deepwater or complex well designs where accurate cement placement is especially critical.
By ensuring controlled and efficient cement placement, the Float Shoe enhances the long-term performance and safety of the well, making it an indispensable tool in the cementing process. Whether in offshore or onshore operations, its contribution to wellbore integrity and fluid isolation is essential for successful drilling outcomes.
How Does a Float Shoe Control Pressure During Drilling?
A Float Shoe is not only vital for preventing backflow and assisting with cementing but also plays an essential role in managing pressure during the drilling process. Pressure control is a critical component of drilling operations, as improper pressure management can lead to hazardous situations such as well control issues, blowouts, or equipment failure. The Float Shoe helps regulate pressure by acting as a check valve that prevents unwanted fluid movement, thereby maintaining wellbore stability and safety throughout drilling operations.
1. Pressure Sealing During Drilling Operations
During drilling, a variety of fluids are used, including drilling mud, cement, and completion fluids. These fluids are pumped into the wellbore to facilitate operations, cool the drill bit, and support the casing. However, pressure variations can occur due to changes in the fluid levels, pump rates, or formation conditions. Without proper pressure control, these fluctuations could lead to issues like blowouts, well kicks, or even equipment failure.
The Float Shoe helps to seal the wellbore during drilling operations by providing a barrier to backflow. The one-way valve in the float shoe ensures that pressure from the wellbore cannot escape and that unwanted fluids, such as drilling mud or gas, cannot migrate back into the casing. This helps to stabilize the pressure in the wellbore, creating a safer environment for both the drilling team and the equipment.
The Float Shoe maintains pressure in two key ways:
Preventing Backflow: As mentioned earlier, the check valve inside the float shoe prevents fluids from flowing back into the wellbore. This helps maintain the pressure within the well during drilling.
Allowing Pressure Buildup: The shoe allows pressure to build up as necessary during certain stages of drilling. The check valve can hold back fluids, ensuring that pressure is effectively managed throughout the operation.
2. Managing Pressure Surges and Fluctuations
Drilling operations are inherently dynamic, and pressure surges can occur when fluids are rapidly displaced or pumped into the well. These surges can cause instability in the wellbore, resulting in pressure spikes that could lead to equipment failure or other safety risks. The Float Shoe plays a significant role in managing these pressure fluctuations.
When drilling fluids are pumped, the Float Shoe ensures that the pressure is maintained in a controlled and stable manner. If there is an increase in pressure due to a surge, the shoe's check valve closes, preventing any excess fluid from escaping and allowing the pressure to equalize. This helps to minimize the risk of pressure-related issues during drilling.
Additionally, pressure surges are often caused by variations in the drilling mud’s weight, changes in the well's depth, or even geological formations. The Float Shoe helps mitigate these issues by maintaining a seal at the bottom of the casing, where pressure buildup is most critical. By controlling the flow of fluids and preventing backflow, the Float Shoe minimizes the chances of a dangerous pressure spike or uncontrolled release of fluids.
3. Prevention of Well Control Problems
Well control issues, including blowouts and well kicks, can occur when pressure in the wellbore becomes unbalanced. A well kick happens when formation fluids (such as gas or oil) enter the wellbore due to a loss of pressure. Blowouts occur when this uncontrolled pressure leads to the rapid expulsion of fluids from the well. Both scenarios can be dangerous and costly.
The Float Shoe helps prevent well control issues by maintaining wellbore pressure at all times. By ensuring that no backflow occurs during drilling, it prevents the influx of formation fluids into the wellbore. This is especially important when drilling through high-pressure formations, as the Float Shoe ensures that pressure remains stable and the wellbore remains isolated from formation fluids.
Moreover, the Float Shoe can help to balance the wellbore pressure during temporary suspension of drilling operations. For instance, when drilling is paused, the float valve will prevent fluids from moving in or out of the wellbore, maintaining a constant pressure. This is crucial to prevent well control problems and ensure that pressure is restored when drilling resumes.
4. Float Shoe Innovations for Pressure Management
Modern advancements in Float Shoe design have made these tools even more effective in controlling pressure during drilling operations:
Adjustable Flow Valves: Some advanced float shoes allow for more precise control over the pressure by adjusting the size of the check valve or adding multiple valves that can open and close under varying pressure conditions. This allows the float shoe to respond more effectively to different wellbore environments.
Pressure-Activated Valves: These float shoes are equipped with valves that automatically adjust depending on the pressure changes in the wellbore. This dynamic adjustment helps ensure optimal pressure control in fluctuating drilling conditions.
Enhanced Durability and Performance: New materials and coatings have improved the overall durability of the Float Shoe, allowing it to withstand higher pressure conditions. These innovations ensure that the float shoe continues to perform reliably even in extreme drilling environments, such as deepwater or high-temperature wells.
The Float Shoe is a simple yet essential tool in pressure management during drilling. Its ability to seal the wellbore, prevent backflow, and stabilize pressure is key to maintaining safety and operational efficiency. In the next section, we will delve into the specific function of the built-in check valve inside the Float Shoe.
What is the Function of the Built-in Check Valve in a Float Shoe?
The built-in check valve is one of the most important features of a Float Shoe, serving a critical role in the overall function of the tool during drilling and cementing operations. The primary purpose of this valve is to prevent backflow of fluids from the wellbore into the casing, ensuring that the wellbore pressure remains stable and that unwanted fluids do not enter the casing string.
1. One-Way Flow Control
At its core, the check valve inside the Float Shoe is a one-way valve designed to allow fluids to flow in only one direction — into the casing. During cementing operations, cement slurry is pumped into the casing to create a permanent seal. As the cement flows into the casing, the check valve remains open, allowing the slurry to be pumped without obstruction. However, once the pumping stops, the valve automatically closes, preventing the cement from flowing back into the wellbore.
This one-way flow mechanism is essential because it:
Maintains Wellbore Integrity: The check valve ensures that fluids, especially cement, stay in place inside the casing, effectively isolating different formations and preventing unwanted fluid migration.
Preserves Pressure: By preventing backflow, the valve helps maintain pressure in the wellbore, reducing the risk of well control issues, such as pressure surges or formation influx.
2. Automatic Operation Under Pressure
The check valve operates automatically under varying pressures. As the fluid is pumped through the casing, the pressure forces the valve to open, allowing the cement or other fluids to flow into the casing. Once the pumping ceases and pressure in the system drops, the valve seals tightly, preventing backflow. This ensures that the cement remains where it is needed and does not escape, ensuring the success of the cementing job.
3. Preventing Contamination and Pressure Loss
By preventing backflow, the check valve ensures that contaminants, such as drilling mud or formation fluids, cannot flow into the casing. This is particularly important in preventing contamination of the cement slurry and ensuring that the casing is properly sealed. Furthermore, the valve helps to avoid pressure loss during drilling, which could otherwise lead to well control problems.
In summary, the built-in check valve in a Float Shoe is an essential component that helps control fluid flow, maintains pressure, and ensures the integrity of the wellbore. Its automatic function under pressure conditions makes it a reliable and critical part of the drilling and cementing process.
Why is a Float Shoe Installed at the Bottom of the Casing?
The installation of a Float Shoe at the bottom of the casing string serves several important purposes that are essential for the stability, efficiency, and safety of the drilling operation. By positioning the Float Shoe at the bottom, it ensures that key processes such as cementing and pressure control are carried out effectively, protecting both the wellbore and the casing.
1. Prevents Backflow at the Deepest Point
One of the main reasons for installing the Float Shoe at the bottom of the casing is to prevent backflow of fluids from the wellbore into the casing string at its deepest point. This is crucial because the bottom of the casing is where fluid pressures are highest, and any uncontrolled flow of fluids could compromise the integrity of the wellbore. The Float Shoe's check valve ensures that, as cement or other fluids are pumped into the casing, no fluids can flow backward, preventing contamination or damage to the wellbore.
By installing the Float Shoe at the bottom, the check valve can effectively seal the casing from the wellbore, preventing pressure fluctuations or the risk of unwanted fluid migration.
2. Supports Efficient Cementing
The Float Shoe plays a pivotal role during cementing operations, which are essential for securing the casing in place and isolating formations. When cement is pumped into the casing, the Float Shoe allows the cement to flow in while preventing backflow when the pumping stops. By placing the Float Shoe at the bottom, it ensures that the cement will flow evenly throughout the casing, creating a strong bond between the casing and the wellbore.
The Float Shoe also helps to prevent the backflow of cement slurry into the wellbore, ensuring that the cementing job is completed successfully and effectively. If the Float Shoe were not placed at the bottom of the casing, there could be an uneven distribution of cement, leading to weak spots that might compromise the well’s structural integrity.
3. Helps with Pressure Control
The Float Shoe is also important for controlling pressure during drilling and cementing. When placed at the bottom of the casing, it acts as a barrier that helps to maintain pressure in the wellbore. As drilling fluids and cement are pumped into the casing, the Float Shoe’s check valve prevents pressure loss by preventing backflow. This helps ensure the wellbore remains stable, reducing the risk of pressure surges, well control problems, and blowouts.
In deeper wells or high-pressure environments, the Float Shoe is essential for preventing pressure imbalances that could lead to dangerous situations.
4. Simplifies Casing Running and Job Completion
The placement of the Float Shoe at the bottom of the casing also simplifies the overall casing running process. The float shoe acts as a guide during the casing’s descent, ensuring it settles properly in the wellbore. Furthermore, it eliminates the need for additional tools or operations to prevent backflow or manage fluid pressure. This simplifies the workflow and reduces the number of steps needed to complete the job.
How Does a Float Shoe Contribute to Efficient Drilling Operations?
The Float Shoe plays a significant role in enhancing the efficiency of drilling operations. By ensuring smooth and controlled pressure management, reducing operational risks, and simplifying the cementing process, the Float Shoe contributes directly to a more streamlined and cost-effective drilling operation. Here’s how it helps in increasing efficiency:
1. Facilitates a Smooth Cementing Process
Cementing is a critical part of drilling, ensuring well integrity and formation isolation. The Float Shoe plays a key role in this process by preventing backflow of fluids and ensuring that the cement stays where it is needed. Its one-way check valve ensures that once cement is pumped into the casing, it cannot escape back into the wellbore. This helps in preventing cement contamination and avoids the need for costly rework. Efficient cement placement helps prevent formation damage, maintains pressure control, and creates a solid bond between the casing and the formation, all of which are essential for the stability of the well.
By preventing backflow and ensuring proper cement placement, the Float Shoe reduces the chances of well integrity issues, which could lead to costly delays, equipment failures, or the need for additional interventions.
2. Minimizes Risk of Well Control Problems
One of the most significant risks in drilling operations is the potential for well control issues, such as blowouts or well kicks, which occur when pressure imbalances cause unwanted fluids to enter the wellbore. The Float Shoe helps to mitigate this risk by maintaining pressure in the wellbore and preventing backflow during both cementing and drilling operations.
By preventing fluid migration, the Float Shoe ensures that pressure fluctuations are minimized, and pressure is maintained at safe levels. This reduces the risk of a well kick or blowout, both of which can cause major disruptions to the drilling process and incur significant costs in terms of time, resources, and safety.
3. Reduces Operational Complexity
Drilling operations can be complex, with numerous variables and tools involved. The Float Shoe simplifies the cementing process and reduces the need for multiple equipment pieces or tools. Its ability to manage backflow, control pressure, and assist with cement placement ensures that these tasks are handled efficiently and effectively with just one tool. This reduces the number of operations required, saving time and reducing the risk of operational errors.
Furthermore, its design allows for faster casing runs, which can expedite the drilling process and lead to overall time savings.
4. Enhances Wellbore Integrity
The Float Shoe is integral in maintaining the structural integrity of the wellbore. By ensuring that cement is placed properly around the casing and preventing backflow, it helps create a strong, stable bond between the casing and the formation. This is crucial for isolating different geological formations, preventing fluid migration, and preventing the casing from shifting during later phases of drilling or production.
A well-maintained casing, with properly placed cement, reduces the need for costly interventions or repairs, saving both time and resources in the long run.
Conclusion
The Float Shoe is an indispensable tool in the drilling and cementing processes, playing a critical role in maintaining wellbore integrity, controlling pressure, and ensuring the success of cementing operations. By preventing backflow, facilitating smooth cement placement, and simplifying the overall drilling workflow, the Float Shoe significantly enhances operational efficiency and reduces the risk of costly delays or well control issues. Its design ensures that the casing remains securely in place, pressure is properly maintained, and fluid migration is prevented, making it essential for safe and successful drilling operations.
For more information or inquiries about Float Shoes and other oilfield products, please reach out to us at oiltools15@welongpost.com.
References
1. Schramm, L. L. (2014). Drilling Fluid Processing Handbook. Schlumberger.
2. Vázquez, A., & Orozco, J. (2010). Oilwell Cementing. Gulf Professional Publishing.
3. Mitchell, R. L., & Devereux, P. A. (2016). Fundamentals of Drilling Engineering. SPE Textbook Series.
4. Carroll, S. R., & Andrawes, R. S. (2009). Advanced Cementing: Technology, Analysis, and Design. SPE/IADC Drilling Conference.
5. Sattar, A., & Ali, M. (2017). Cementing Technology for Oil and Gas Well Construction. Springer.
6. Halliburton (2012). Well Cementing: Principles and Practices. Halliburton.

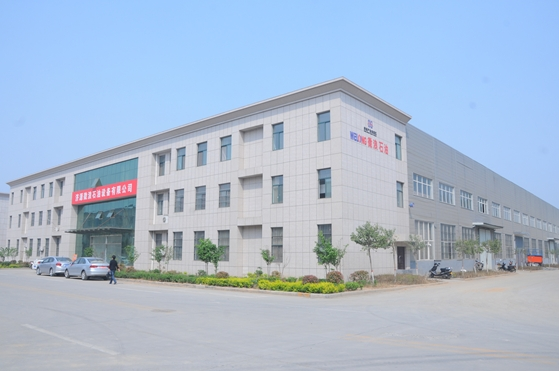
CHINA WELONG - 20+ years manufactuer in oilfield tools
Popular Blogs