What are the components of Float Shoe?
A float shoe is a vital piece of equipment used in the oil and gas industry, especially during the cementing process of well construction. It’s designed to control the flow of cement and other fluids within the wellbore, ensuring that they are properly displaced during drilling operations. A Float Shoe is typically attached to the bottom of a casing string and serves as an essential component in preventing backflow, thus providing a secure and controlled environment for cement placement.
The primary components of a Float Shoe include the nose or tip, float valve, check valve, and valve seat. These parts work together to perform specific functions that contribute to the efficiency and safety of the cementing process. The nose or tip is the leading part that helps guide the shoe through the wellbore and ensures that the shoe’s body remains intact. The float valve is a crucial part, as it regulates the flow of fluids and prevents backflow, keeping the cement slurry inside the casing. The check valve is designed to prevent reverse flow after the cement is pumped, ensuring that the pressure within the casing remains stable. Finally, the valve seat is responsible for sealing the valve, ensuring a secure closure when cementing operations are completed.
In the next sections, we'll dive deeper into the function of each of these components and explain their role in enhancing the overall performance of the Float Shoe.
What Are the Key Structural Elements of a Float Shoe?
The float shoe’s structural integrity is essential for its performance in the oil and gas cementing process. Its design incorporates several key components that are specifically engineered to provide maximum efficiency during the casing operations. Understanding the float shoe’s structural elements helps professionals in the drilling industry optimize its usage, ensuring secure cement placement and reducing the likelihood of operational issues. The key structural elements of a Float Shoe include the nose, body, valve seat, and threads.
Nose: The nose or tip of the Float Shoe plays a critical role in the float shoe's design, acting as the front-facing component that encounters the wellbore first. The nose is typically streamlined and reinforced to ensure smooth navigation through the casing and to prevent any potential damage. Its primary function is to guide the float shoe through the wellbore and allow the efficient displacement of fluids.
Body: The body of the float shoe serves as the casing connection point and houses the internal components like the valve seat and check valve. Made of durable materials, typically steel or high-grade alloys, the body is designed to withstand high pressures and extreme temperatures. It ensures that the internal components are securely positioned and protected during the drilling process.
Valve Seat: The valve seat plays a pivotal role in sealing the check valve and controlling the flow within the float shoe. When cementing operations are complete, the valve seat ensures that no cement or fluid leaks back into the wellbore, thus maintaining the stability of the cemented casing. It is usually made of materials that are resistant to corrosion and wear, providing longevity to the float shoe.
Threads: The threads are used to connect the float shoe to the casing string. These threaded connections are highly durable and are precision-engineered to provide a secure, tight seal. The threads must be carefully maintained and inspected to ensure that they maintain their integrity throughout the drilling process.
These structural elements must work in tandem for the float shoe to function effectively. By ensuring that each component is made from high-quality materials and designed for optimal performance, operators can rely on the float shoe to perform under demanding conditions.
What Is the Function of the Built-in Check Valve in a Float Shoe?
The built-in check valve in a float shoe is a crucial component that plays an essential role in maintaining wellbore integrity and safety during drilling and cementing operations. The check valve, also known as a non-return valve, serves as a one-way valve that only allows fluids to flow in one direction, which is essential in the prevention of unwanted fluid migration.
One of the main functions of the built-in check valve is to prevent the backflow of drilling mud or other fluids during the cementing process. When cement is pumped into the wellbore, the check valve ensures that the cement remains in place, preventing it from being displaced by the fluids inside the well. Without this function, fluids could potentially flow back into the wellbore, destabilizing the well's pressure and potentially causing a blowout or other hazardous events. By stopping backflow, the check valve helps maintain the required pressure in the wellbore, ensuring that the cementing process proceeds smoothly.
Additionally, the check valve aids in maintaining the proper wellbore pressure during drilling and completion. By preventing the return of fluids, it ensures that the pressure is stabilized, reducing the risk of pressure fluctuations that could harm the wellbore or equipment. The valve also ensures that pressure from the cement slurry is effectively managed, preventing any disruption during the curing phase of the cement.
Another important aspect of the check valve is its contribution to the efficiency of the drilling and cementing process. With the valve in place, there is less need for manual pressure control and monitoring, as the built-in mechanism provides automatic regulation. This reduces human error and improves overall operational safety. Additionally, the check valve contributes to reducing the potential for contamination of the cement slurry by isolating the casing from the surrounding fluids.
In conclusion, the built-in check valve in a float shoe is indispensable for the success of drilling and cementing operations. It ensures that the well remains stable and pressure-controlled, preventing backflow and safeguarding the integrity of the cement job and the wellbore. This component is key to reducing the risk of blowouts, fluid migration, and other wellbore instability issues, making it a vital part of any drilling operation.
What Materials Are Used in the Construction of a Float Shoe?
The materials used in the construction of a float shoe are crucial in determining its strength, durability, and performance under extreme conditions. Since float shoes are exposed to high pressures, temperatures, and abrasive environments during cementing operations, the selection of materials is critical to ensure reliability and efficiency. The materials chosen must be resistant to corrosion, wear, and damage, ensuring that the float shoe performs optimally throughout the cementing process.
Steel Alloys: The body and structural components of a float shoe are typically made from high-strength steel alloys. Steel is favored for its ability to withstand high pressures and harsh environments, making it ideal for use in deep wells and other challenging drilling scenarios. Steel alloys are also highly resistant to wear and fatigue, ensuring that the float shoe maintains its structural integrity even under the most demanding conditions. Stainless steel, in particular, is commonly used because of its superior resistance to corrosion.
High-Grade Ceramics: In some float shoes, ceramic materials are incorporated into the design, especially in areas that are exposed to abrasive conditions. High-grade ceramics are known for their hardness and resistance to wear, which makes them an excellent choice for parts of the float shoe that experience high friction, such as the valve seat or the tip. These materials can help extend the lifespan of the float shoe and improve its overall performance.
Rubber Seals: Rubber is used in the construction of seals within the float shoe. The seals are essential for ensuring a tight, leak-proof fit between the various components of the float shoe, particularly around the check valve and the valve seat. Rubber materials are chosen for their elasticity, flexibility, and ability to maintain a secure seal under varying pressures. In addition, rubber seals are resistant to a wide range of chemicals and temperatures, making them suitable for use in the oil and gas industry.
Composite Materials: Some float shoes may also incorporate composite materials, which combine the advantages of different materials, such as strength, lightness, and resistance to corrosion. These materials are often used in the construction of the valve seat and other critical components to enhance their performance and durability. Composites can also provide a cost-effective alternative to traditional materials without sacrificing reliability.
Ceramic-Coated Components: Some float shoes feature ceramic coatings on key components such as the valve seat, the float valve, and the body. These coatings help protect against wear and corrosion, extending the life of the float shoe and ensuring consistent performance over time. Ceramic coatings are especially useful in high-abrasion zones, where the float shoe may come into contact with sand, rock particles, or other abrasive materials.
The choice of materials for a float shoe is essential in determining its ability to perform under the conditions of a specific well. By selecting the appropriate materials, manufacturers ensure that the float shoe can withstand the high pressures, temperatures, and abrasive environments typical in the oil and gas industry.
How Does the Float Valve in a Float Shoe Work?
The float valve is a critical component of the float shoe, performing a key role in managing the flow of cement slurry during the cementing process. It is designed to regulate the fluid flow into the casing while preventing backflow once the cement has been pumped. The float valve is a one-way valve, and its operation is essential for ensuring that cement slurry remains in the casing and that no reverse flow contaminates the wellbore. Understanding how the float valve works helps operators ensure the efficiency and safety of cementing operations.
One-Way Flow Mechanism: The float valve is designed to allow fluid to flow in only one direction. During the cementing operation, as cement is pumped into the casing, the valve opens to allow the slurry to enter the casing. The valve operates under differential pressure, meaning it opens when the pressure from the cement pump is greater than the pressure from the wellbore. Once the desired amount of cement has been pumped, the pressure from the pump decreases, causing the valve to close, effectively sealing the casing and preventing any cement or other fluids from flowing back into the wellbore.
Prevents Reverse Flow: One of the float valve's primary functions is to prevent reverse flow of cement slurry and other fluids. After the cementing is completed, the valve closes tightly, ensuring that no backflow occurs. This is vital in maintaining wellbore stability and ensuring that the cement remains in place, creating a secure seal in the casing. The absence of reverse flow also prevents contamination of the wellbore with cement, which could interfere with subsequent operations.
Pressure Control: The float valve also plays a significant role in controlling the pressure inside the casing. By preventing the cement from flowing backward into the wellbore, the valve helps maintain the required pressure within the casing during the cementing process. Proper pressure control is essential to ensure that the cement sets properly and that the casing remains stable. Any pressure fluctuations caused by backflow could compromise the integrity of the wellbore and result in failed cementing.
Design Variations: Float valves come in various designs, with some using spring-loaded mechanisms to control the opening and closing of the valve. Others may operate using differential pressure, depending on the specific needs of the cementing operation. Regardless of the design, the core function remains the same: to regulate fluid flow and prevent reverse flow into the wellbore, ensuring that the cement job is completed efficiently and securely.
Durability and Maintenance: Since the float valve is subjected to high pressures, temperatures, and corrosive environments, it is designed to be durable and long-lasting. The valve’s materials are selected for their ability to withstand extreme conditions, and regular maintenance is necessary to ensure that it continues to function properly. Operators must inspect the float valve periodically for any signs of wear or damage, as a malfunctioning valve can result in failed cementing jobs and costly repairs.
The float valve is a simple yet highly effective mechanism that plays a pivotal role in ensuring the success of cementing operations. By preventing backflow and maintaining pressure control, the float valve contributes significantly to the overall efficiency and safety of the drilling process.
What Is the Purpose of the Nose or Tip of a Float Shoe?
The nose or tip of a float shoe plays a vital role in guiding the float shoe through the wellbore and ensuring a smooth and effective cementing process. Although it may seem like a simple part of the float shoe, the nose is an essential component that helps maintain the integrity of the well and ensures that the cement slurry is properly placed. Its design is crucial in preventing damage to the float shoe and minimizing operational risks during drilling and cementing operations.
Guiding the Float Shoe: The primary purpose of the nose is to guide the float shoe as it moves through the wellbore. The nose is the leading edge of the float shoe, and it helps ensure that the shoe moves smoothly through the casing while minimizing friction and damage to the wellbore. Its streamlined design enables the float shoe to navigate through narrow sections of the casing and any irregularities within the wellbore, reducing the risk of operational delays and ensuring that the float shoe remains intact during the cementing process.
Protection of Internal Components: The nose also helps protect the internal components of the float shoe, such as the check valve, valve seat, and float valve, from potential damage. By absorbing the initial impact as the float shoe enters the wellbore, the nose minimizes the wear and tear on these sensitive components. This is especially important in deep wells where high pressures and abrasive conditions can place strain on the equipment.
Ensuring Fluid Displacement: The nose is designed to facilitate the proper displacement of fluids, such as cement slurry, during the cementing process. As the float shoe enters the casing, the nose ensures that the cement is displaced efficiently into the annular space between the casing and the wellbore. A well-designed nose helps prevent the formation of channels or gaps in the cement, ensuring that the entire casing is securely sealed and that there is no possibility of fluid migration or wellbore instability.
Reducing Friction and Erosion: In addition to guiding the float shoe and protecting internal components, the nose is designed to reduce friction between the float shoe and the wellbore. This is crucial in preventing erosion and wear on both the float shoe and the casing. A well-designed nose helps maintain the structural integrity of the casing and float shoe, preventing unnecessary damage and increasing the overall lifespan of the equipment.
Material Considerations: The nose is typically made from durable materials, such as high-strength steel alloys or composite materials, to ensure that it can withstand the high pressures and abrasive conditions found in oil and gas wells. The materials must be resistant to corrosion, erosion, and wear, ensuring that the nose performs consistently throughout the cementing process.
The nose of the float shoe is much more than just a protective covering; it plays a crucial role in ensuring the smooth operation of cementing activities and the overall success of the drilling process. By guiding the float shoe, protecting internal components, and ensuring efficient fluid displacement, the nose contributes to the long-term efficiency and safety of the wellbore.
What Is the Importance of the Valve Seat in a Float Shoe?
The valve seat in a float shoe is an integral component that ensures the proper functioning of the check valve and float valve during cementing operations. It provides a secure, stable base for the sealing mechanism and ensures that the fluid flow is controlled accurately. The importance of the valve seat cannot be overstated, as it directly impacts the effectiveness of the float shoe and the overall success of the cementing process.
Sealing Function: The primary role of the valve seat is to provide a tight seal between the check valve and the float shoe’s internal components. When the check valve closes to prevent backflow of cement slurry, it does so by sealing against the valve seat. This ensures that there is no leakage of cement or other fluids back into the wellbore, maintaining wellbore integrity and preventing contamination. A properly seated valve ensures that the cement remains in place and does not flow back, which is essential for the success of the cementing job.
Pressure Control: The valve seat plays a crucial role in controlling the pressure within the casing during the cementing operation. When the check valve closes, it prevents reverse flow, ensuring that the pressure within the casing remains stable. If the valve seat is damaged or worn, the seal could fail, allowing pressure fluctuations that could compromise the cement job and the stability of the casing. The valve seat helps maintain a consistent pressure, which is vital to achieving a successful and stable cement job.
Wear Resistance: The valve seat is subjected to significant wear and tear during cementing operations, particularly in high-pressure and high-temperature environments. Therefore, it is made from durable, wear-resistant materials such as hardened steel, composite materials, or ceramics. These materials help prevent premature damage to the valve seat, ensuring that the float shoe operates reliably throughout the cementing process. A well-made valve seat reduces maintenance needs and extends the life of the float shoe.
Preventing Cement Contamination: The valve seat also helps prevent contamination of the cement slurry during placement. When the valve is properly seated, it ensures that no fluids other than the cement are allowed into the casing, maintaining the purity of the cement and ensuring that it bonds effectively to the casing. This is particularly important in wells where the integrity of the cement bond is critical to preventing fluid migration and ensuring a long-term, stable seal.
Ensuring Long-Term Functionality: Given that the valve seat is a key part of the sealing mechanism, its proper functioning is essential for the long-term success of the float shoe. If the valve seat becomes damaged or worn over time, it can cause sealing failures, leading to cementing issues such as leakage or improper fluid placement. Regular inspections and maintenance of the valve seat are crucial to ensuring that the float shoe continues to perform as expected, especially in demanding and high-pressure environments.
The valve seat is a small but highly significant component of the float shoe that directly impacts the overall efficiency and success of cementing operations. By providing a secure sealing surface, ensuring pressure stability, and preventing cement contamination, the valve seat contributes to the safety and reliability of the drilling process.
Conclusion
In conclusion, the components of a float shoe work together to ensure efficient, safe, and effective cementing operations. Each part, from the structural elements and check valve to the valve seat and the nose, serves a specific purpose in protecting the wellbore, maintaining pressure, and preventing fluid backflow. Understanding the function and importance of these components is crucial for selecting the right float shoe and ensuring the success of cementing jobs in the oil and gas industry.
Selecting the right taper mill for your application is crucial to the efficiency and success of your drilling and cementing operations. When considering a taper mill, it's important to take into account factors such as the specific well conditions, the type of casing, and the pressures and temperatures expected in the well. Welong offers a range of high-quality taper mills designed to handle tough well conditions and provide reliable performance. With our extensive experience in the oil and gas industry, we can help you choose the most suitable mill for your project, ensuring optimal performance and cost-effectiveness.
For more information on how to select the right float shoe or to inquire about any of our other oilfield products, please feel free to contact us at oiltools15@welongpost.com.
References
1. "Float Shoe Design and Functionality in Cementing Operations" – Journal of Petroleum Engineering
2. "The Role of Valve Seats in Oilfield Equipment" – SPE Journal
3. "Advanced Materials for Oilfield Tools" – International Journal of Materials Science
4. "Cementing Technology and Its Impact on Well Integrity" – Oil and Gas Industry Review
5. "Understanding the Check Valve and Float Valve Mechanisms in Float Shoes" – Drilling Engineering Handbook
6. "Durability and Performance of Float Shoes in Harsh Drilling Conditions" – Oilfield Equipment Technology Reports

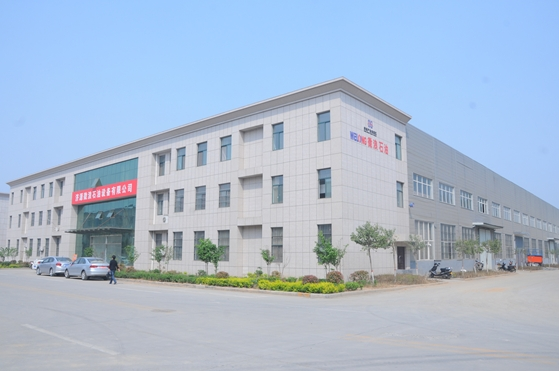
CHINA WELONG - 20+ years manufactuer in oilfield tools
Popular Blogs