How does Float Shoe work?
A float shoe is a crucial component in the well construction process, particularly during drilling operations. It serves as a one-way valve, designed to control fluid flow and prevent backflow during drilling or cementing processes. Essentially, the float shoe is placed at the bottom of the casing string before it is lowered into the well. Its primary function is to allow drilling mud or cement to flow in one direction—down the casing string—while preventing any unwanted fluids from flowing back up. This mechanism is critical for maintaining the integrity of the well and ensuring smooth operations.
The float shoe features a valve system that operates when the casing is set into position. During drilling or cementing, pressure from the well forces the valve to remain closed, preventing the fluid from returning up the casing. As soon as the casing is cemented and pressure is equalized, the float shoe allows for the release of cement or drilling fluid, aiding in the sealing process.
How Is the Float Shoe Installed in the Casing String?
The installation of a float shoe within a casing string is a precise operation that requires attention to detail and careful planning. Typically, the float shoe is placed at the bottom of the casing string, just before the casing is lowered into the well. It is usually positioned at the lower end of the casing to ensure that it serves its purpose effectively during drilling or cementing operations.
The installation process begins with selecting the appropriate float shoe that matches the well's specifications, including the diameter, pressure rating, and type of valve. Once selected, the float shoe is attached to the casing using a casing collar. This ensures a secure connection between the shoe and the casing string, preventing any disconnections during the installation process.
After the float shoe is securely attached, the casing string is lowered into the wellbore. As the casing reaches the desired depth, the float shoe performs its primary function by preventing any backflow of drilling fluid or cement. It does so by utilizing its built-in one-way valve, which is activated by pressure from the wellbore. The float shoe remains closed under normal conditions, but if the pressure in the casing exceeds a certain threshold, it allows fluids to flow through, typically for cementing operations.
The proper installation of the float shoe is essential for the overall success of the cementing operation. If the shoe is not positioned correctly or if it fails to function as intended, it can lead to complications such as fluid backflow, poor cement bonding, or even well control issues.
What Role Does a Float Shoe Play in Controlling Pressure?
A float shoe plays an indispensable role in maintaining wellbore pressure during both drilling and cementing operations. It functions as a crucial pressure regulator, ensuring the casing string remains pressurized while preventing the backflow of fluids into the wellbore. This pressure control is vital for preventing formation fluid influx, which, if not controlled, can lead to wellbore instability, kickbacks, or even blowouts—dangerous outcomes that can severely affect the safety and efficiency of the operation.
Pressure Regulation During Drilling Operations
During drilling operations, the float shoe ensures that the casing string remains filled with drilling mud, which is essential for maintaining consistent hydrostatic pressure. The drilling fluid, or mud, provides a counteracting force against the natural pressure of the surrounding formations. This prevents unwanted formation fluids from entering the wellbore, which could otherwise cause dangerous situations such as kicks or wellbore instability. The float shoe is equipped with a one-way valve that regulates the flow of drilling mud into the casing string, ensuring that only the necessary amount flows in. At the same time, any potential pressure buildup or backflow is prevented by the shoe’s mechanism, which closes tightly to maintain well control.
Importance in Cementing Operations
The float shoe also plays a critical role during cementing operations. As cement is pumped into the casing to create a seal between the casing and the wellbore, the float shoe regulates the pressure to ensure that the cement is distributed correctly. By managing the flow of cement into the annular space between the casing and wellbore, the float shoe ensures that the proper amount of cement is placed, and that the pressure is evenly distributed throughout the well. This is particularly important when cementing at deeper depths, where pressure fluctuations can be significant. If the pressure exceeds safe limits, the float shoe momentarily opens to release excess pressure, restoring balance to the well before closing again once normal conditions are regained.
Preventing Contamination and Maintaining Pressure Gradient
Beyond controlling pressure, the float shoe helps to maintain a stable and consistent pressure gradient throughout the operation. This ensures that wellbore integrity is preserved and prevents contamination of the wellbore fluids. By regulating the pressure, the float shoe helps avoid any fluctuations that could disturb the cement placement or mud circulation. Its reliable operation is a key factor in achieving a successful cementing or drilling operation and ensuring the safety and efficiency of the wellbore.
In conclusion, the float shoe is an essential component in the drilling and cementing process, offering both safety and operational efficiency. Its ability to control pressure, prevent fluid backflow, and ensure accurate cement placement makes it indispensable for maintaining well integrity and avoiding hazardous incidents in deepwater and high-pressure environments.
How Does a Float Shoe Prevent Fluid Backflow During Drilling?
A float shoe is a critical component in preventing fluid backflow during drilling operations, a crucial function that helps avoid a variety of complications that could jeopardize both the safety and efficiency of the well. Fluid backflow, if not properly controlled, can lead to issues such as contamination of the wellbore, loss of well control, and compromised well integrity, which could potentially result in dangerous consequences such as blowouts, equipment failure, or costly delays. The float shoe plays a pivotal role in maintaining wellbore stability by using a sophisticated one-way valve system that ensures fluids can only flow downward through the casing string, while blocking any upward flow from the wellbore.
The float shoe’s one-way valve mechanism operates effectively by maintaining the valve in a closed position when drilling fluid or mud is pumped into the casing. The pressure exerted by the fluid keeps the valve sealed, preventing any backflow of the fluid into the wellbore. This is particularly important because uncontrolled fluid movement can cause dangerous pressure surges that might lead to significant well control problems, such as a blowout, which poses both safety and environmental risks. In this way, the float shoe ensures that the pressure within the casing remains stable and does not exceed safe operational limits.
In deep wells or areas where the surrounding formation pressure is high, the float shoe's role becomes even more crucial. The tool helps to contain the pressures within the casing, ensuring that fluids remain securely sealed within the casing string. This prevents the migration of unwanted fluids into the wellbore, which could lead to contamination of the well or even compromise the integrity of the drilling process. When the casing string is lowered into the wellbore, the float shoe maintains a sealed environment, ensuring the wellbore’s stability, even in challenging conditions such as high-pressure zones.
Furthermore, the float shoe often works in conjunction with other essential pieces of equipment, such as the float collar, to guarantee complete isolation of the wellbore from backflow. Together, these tools form a double layer of protection against the risks of fluid contamination and pressure imbalances. The float shoe, being positioned at the bottom of the casing, acts as the last line of defense to ensure the well is kept safe from unwanted fluids like formation water, oil, or gas that could otherwise infiltrate the wellbore. By preventing the upward migration of these fluids, the float shoe ensures that the drilling operation remains safe, efficient, and controlled throughout the entire process.
Overall, the float shoe’s primary function of preventing backflow is vital to ensuring the safety, integrity, and success of drilling operations. It helps manage fluid movement and wellbore pressure, ensuring that both the wellbore and the surrounding formation remain protected. Without the float shoe, the risks of contamination, loss of well control, and equipment damage would significantly increase, potentially leading to catastrophic outcomes.
How Does a Float Shoe Assist in Well Cementing Operations?
During well cementing operations, the float shoe is an essential component that plays a critical role in ensuring the proper placement of cement and maintaining the integrity of the wellbore. Cementing is a vital step in the well construction process, as it secures the casing in place and forms a reliable barrier between the wellbore and the surrounding formations. Without a proper cement job, issues such as fluid migration, compromised well integrity, and uncontrolled pressure can arise, leading to significant operational challenges and safety risks.
Float Shoe’s Role in Cement Flow Regulation
The float shoe assists in cementing by controlling the flow of cement into the casing, ensuring it is placed accurately in the annular space between the casing and the wellbore. Once the casing string reaches the desired depth in the well, the float shoe is positioned at the bottom of the casing, allowing the cement slurry to be pumped into the wellbore. The float shoe contains a one-way valve that prevents the cement from flowing back into the casing once it has been pumped into the annular space. This feature ensures that the cement remains in place, providing a solid and continuous barrier between the wellbore and the surrounding geological formations.
Achieving a Proper Cement Seal
One of the key advantages of using a float shoe in cementing operations is its role in achieving a proper cement seal. This seal is necessary to prevent the migration of gas, oil, or water between different formations, which could otherwise lead to contamination or wellbore instability. The float shoe helps ensure that the cement fills the gap between the casing and the wellbore evenly, forming a reliable barrier that isolates various well zones. By creating a solid seal, the float shoe ensures the structural integrity of the well and minimizes the risk of crossflow or the unwanted movement of fluids.
Preventing Backflow and Managing Pressure
The float shoe also plays a critical role in preventing backflow of drilling mud or cement during the displacement phase. When the cement slurry is being pumped into the well, the float shoe remains closed, preventing any unwanted fluids from flowing back into the casing. Once the cement has been successfully placed, the valve in the float shoe opens to release any excess pressure that may have built up during the pumping process. This controlled release of pressure is crucial for ensuring the cement is placed optimally, especially in deep wells where pressure variations can be significant and challenging to manage.
Ensuring Efficient Cement Placement and Wellbore Stability
The float shoe's contribution to well cementing extends beyond just preventing backflow. By regulating the pressure and fluid flow, it helps ensure that the cement is placed efficiently and uniformly throughout the annular space. This precise placement of cement is crucial for maintaining wellbore stability and achieving long-term well performance. In deep wells or high-pressure environments, where fluctuations in pressure can be extreme, the float shoe’s ability to manage these variations ensures that the cement forms a reliable and consistent seal, contributing to the overall integrity of the well.
How Does the Float Shoe Release Cement After Drilling?
After drilling operations have been completed and the casing string is in place, the float shoe plays an important role in the cementing process, specifically in releasing the cement into the wellbore. The float shoe’s one-way valve is designed to remain closed during the drilling process to prevent fluid backflow. However, once drilling is finished and the casing is set, the float shoe allows for the release of the cement slurry that has been prepared for wellbore sealing.
The primary function of the float shoe during this phase is to facilitate the controlled release of cement. When the casing is in place and pressure is applied, the float shoe’s valve opens, allowing cement to flow into the annular space between the casing and the wellbore. The float shoe ensures that the cement flows in a controlled and directed manner, allowing the operator to manage the placement of the cement slurry.
This step is crucial because it seals the wellbore and prevents the migration of formation fluids into the well, ensuring the integrity of the well. The float shoe’s controlled release function helps ensure that the cement is placed at the correct depth and that no unwanted fluid is allowed to enter or escape the wellbore. This creates a stable, sealed environment that supports the overall long-term health of the well.
Once the cement has been placed and the float shoe is no longer needed, the valve typically remains open, allowing the cement to set and cure properly. This action prevents excessive pressure buildup, ensuring that the cement job is successful and that there is no fluid backflow once the cement sets.
In conclusion, the float shoe's ability to release cement after drilling is critical for maintaining wellbore integrity, sealing the well, and preventing unwanted fluid migration. Its role in cementing operations ensures that the well is safely sealed and can withstand the pressures encountered in the wellbore over time.
How Does a Float Shoe Work to Isolate Different Well Zones?
One of the critical functions of a float shoe is its ability to help isolate different well zones during drilling and cementing operations. Wellbore zonal isolation is essential for maintaining the integrity of the well and preventing unwanted fluid migration between different geological formations. The float shoe plays a vital role in ensuring that the cementing process creates a reliable barrier between these zones, protecting both the wellbore and the surrounding formations.
When a casing is installed, the float shoe at the bottom of the casing string allows for the effective sealing of the annular space. This sealing process ensures that fluids such as water, oil, or gas do not flow from one formation to another, which could compromise well control and productivity. By preventing fluid migration between different well zones, the float shoe helps ensure that the well remains stable, and that each zone is properly isolated from the others.
The float shoe operates by maintaining pressure control, preventing backflow, and allowing the controlled release of cement. Once the casing is positioned at the desired depth, cement is pumped into the annular space, and the float shoe’s one-way valve ensures that the cement forms a solid barrier between the casing and the wellbore. This barrier isolates the well zones, allowing each zone to be controlled independently and preventing any crossflow of fluids between them.
Additionally, the float shoe plays a role in preventing any undesirable pressure fluctuations during the cementing process. By controlling the flow of cement, it ensures that the well zones are isolated under the right conditions. If the pressure in one zone is higher than the other, the float shoe can prevent any unwanted fluid or gas migration, which could jeopardize the well’s stability or safety.
In summary, the float shoe’s ability to isolate different well zones during drilling and cementing operations is essential for maintaining well integrity, controlling fluid migration, and ensuring the long-term success of the wellbore. It is a crucial tool in the well construction process, ensuring that each zone remains properly sealed and isolated from the others.
Conclusion
The float shoe is an integral component in the drilling and cementing process, providing essential pressure control, backflow prevention, and zonal isolation. By ensuring the proper placement of cement, regulating fluid flow, and protecting the wellbore from unwanted fluid migration, the float shoe contributes to the overall integrity and safety of the well. Its role in both the drilling and cementing phases of well construction is critical to ensuring successful and efficient operations.
At Welong, we offer a range of high-quality taper mills tailored to meet your operational needs. Our products are designed to provide the best value while maintaining cost-effectiveness and high-quality standards. We offer customization based on your requirements, ensuring that your taper mill is suitable for even the most demanding applications.
For further information about float shoes or any other oilfield products, feel free to contact us at oiltools15@welongpost.com.
References
1. Smith, J. (2020). Casing and Cementing in Well Construction. Journal of Petroleum Engineering.
2. Jones, A., & Williams, L. (2019). Innovative Solutions for Wellbore Integrity. Oil and Gas Technology.
3. Anderson, M., & Taylor, R. (2021). The Role of Float Equipment in Cementing Operations. International Journal of Drilling.
4. Peterson, D. (2018). Pressure Control during Drilling: Equipment and Techniques. Journal of Well Engineering.
5. Harris, B., & Lee, K. (2022). Zonal Isolation and Cementing in Deepwater Wells. Offshore Technology Conference Proceedings.
6. Turner, H., & Martin, P. (2020). Best Practices in Float Shoe and Cementing Equipment Selection. SPE/IADC Drilling Conference.

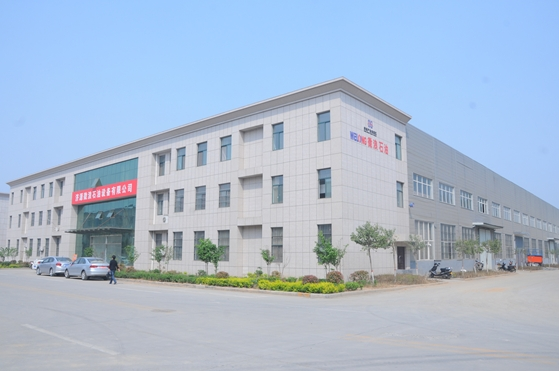
CHINA WELONG - 20+ years manufactuer in oilfield tools
Popular Blogs