What is Float Shoe?
A float shoe is an integral component of the well construction process in the oil and gas industry. Its primary purpose is to facilitate the successful cementing of the wellbore, providing a secure seal and ensuring well integrity. Positioned at the bottom of the casing string, the float shoe is equipped with a non-return valve, which only allows fluids to flow in one direction – into the well. This prevents any backflow of drilling fluids, such as mud, during the cementing process.
The float shoe ensures that when cement is pumped into the wellbore, it stays in place and doesn’t mix with drilling fluids, which could compromise the cement’s strength and bonding. This tool is essential for achieving proper zonal isolation, which is critical for maintaining well integrity and preventing fluid migration between formations.
In summary, the float shoe is designed to provide pressure control during the cementing phase, prevent contamination of cement, and ensure a stable wellbore that can safely house the casing.
Float Shoe Is Made of Durable, High-Strength Materials
The design and functionality of a float shoe depend heavily on the materials used in its construction. Since the float shoe is exposed to extreme downhole conditions, including high pressure, high temperature, and abrasive environments, it must be made from durable, high-strength materials to ensure reliability.
Steel alloys such as chrome-moly steel are commonly used for their ability to resist corrosion, wear, and impact. These materials are strong enough to withstand the mechanical stresses encountered during drilling and cementing. Additionally, the float shoe’s components, such as the non-return valve, are often made of hard-faced carbide or ceramic materials, which offer excellent resistance to wear and damage from harsh chemicals and high temperatures.
Composite materials have also become more popular in modern float shoe designs. These materials provide excellent chemical resistance and are often used when drilling in challenging environments where traditional steel alloys may not provide sufficient protection. These composite float shoes can offer better performance in terms of corrosion resistance, especially when drilling through highly acidic or salty formations.
Furthermore, the thread design and sealing components of the float shoe are made from high-strength materials to ensure a secure fit within the casing string and to prevent fluid leakage. The durable construction guarantees that the float shoe can withstand the harshest drilling conditions, making it a critical component in any successful well construction project.
Float Shoe Is Used in Well Drilling Operations
The float shoe is an essential component in well drilling operations, playing a key role throughout both the drilling and completion phases of well construction. Once a well has been drilled to the desired depth, the next crucial step is to install the casing. The casing is a steel pipe that lines the wellbore, providing structural integrity and preventing the well from collapsing. It also helps isolate different geological formations to prevent contamination. However, for the casing to be securely placed and effective, it must be properly installed and sealed, which is where the float shoe comes in.
The float shoe is positioned at the bottom of the casing string. As the casing is lowered into the wellbore, the float shoe helps to guide it into position, ensuring it aligns correctly with the wellbore. A key feature of the float shoe is its non-return valve, which prevents the flow of well fluids from traveling back up the casing string. This is especially important during the cementing phase, where cement slurry needs to flow downward into the annular space between the casing and the surrounding formation. By preventing backflow of drilling fluids, the float shoe ensures that the cement slurry remains in place and does not interfere with the sealing process.
Another critical function of the float shoe is aiding in proper zonal isolation. Zonal isolation is vital for preventing the migration of fluids between different geological layers or formations. Without this isolation, unwanted fluids or gases could migrate into areas of the well that need to remain sealed. The float shoe helps ensure that the cementing process creates a strong barrier between different formations, maintaining the stability of the well over time and protecting the integrity of the wellbore.
In addition to its role in cementing, the float shoe contributes to the overall structural soundness of the well. By ensuring proper cement flow and preventing contamination, the float shoe ensures that the casing remains securely in place and that the well remains sealed from top to bottom. This makes the float shoe indispensable in well drilling operations, as it supports the well's structural integrity, prevents fluid migration, and guarantees a successful cementing job that is essential for maintaining the well's longevity and safety throughout its life cycle.
Float Shoe Ensures Proper Well Integrity
One of the most crucial functions of the float shoe is ensuring well integrity, which is vital for the long-term safety and success of oil and gas drilling operations. Well integrity refers to the ability of a well to maintain pressure containment and fluid containment within the wellbore while preventing the undesired migration of fluids or gases into surrounding rock formations or to the surface. In the context of drilling, this integrity is essential not only for operational efficiency but also for environmental protection and cost management.
The float shoe plays an indispensable role in ensuring well integrity during the cementing process. Cementing is a critical operation where cement is pumped into the annular space between the casing and the rock formation to create a secure bond. This bond prevents the movement of fluids, such as oil, gas, or water, from migrating between different zones in the wellbore. When cement is properly placed, it ensures that the casing is firmly secured within the wellbore, providing a barrier to fluids and pressure, and maintaining the overall stability of the well.
One of the key features of the float shoe is the non-return valve. This valve prevents backflow of drilling mud, fluids, or other materials that could mix with the cement during the placement process. Without the float shoe, any unwanted backflow could contaminate the cement, compromising its effectiveness. If the cement job is not executed properly due to contamination or improper placement, the integrity of the well would be at risk. A poor cement job could result in fluid leakage into undesired zones, causing potential environmental hazards or even well failure. Furthermore, it could lead to increased operational costs as additional remedial work would be required to fix the problem.
In addition to protecting the cement job from contamination, the float shoe also ensures proper zonal isolation. This is crucial for maintaining the separation of different geological layers, ensuring that fluids are contained within their respective zones. Without proper zonal isolation, unwanted fluid migration could occur, potentially causing production problems or contamination of nearby water supplies or other environmental resources.
By maintaining a secure seal and ensuring proper zonal isolation, the float shoe plays an essential role in the overall success of the well. It helps protect both the well's structural integrity and the surrounding environment. A well with good integrity is more likely to produce oil and gas safely, minimizing environmental risks and reducing the chances of costly repairs or remediation later in the well’s life. Thus, the float shoe is not just a component of the drilling process but a key factor in the safe and efficient operation of oil and gas wells over their entire lifecycle.
Float Shoe Prevents Backflow of Drilling Fluids
A key function of the float shoe is its ability to prevent the backflow of drilling fluids during the cementing process, a critical phase in well construction. Backflow is a phenomenon where fluids, such as drilling mud, are pushed back into the wellbore, potentially contaminating the cement slurry being pumped into the casing. This contamination can severely affect the quality of the cement job, leading to weak bonds and poor zonal isolation. If the cement slurry becomes diluted or mixed with unwanted fluids, it may fail to form a strong, impermeable barrier between the casing and the formation, which is essential for maintaining well integrity.
The float shoe is equipped with a non-return valve that automatically closes once the cement slurry is pumped into the casing. This valve is designed to operate under high-pressure conditions and to prevent any backflow of fluids from the wellbore into the casing. By doing so, it ensures that the cement slurry remains uncontaminated and that it can properly set and form a solid bond to the casing. The non-return valve is critical because it works instantly to block the reverse flow of drilling fluids, which would otherwise interfere with the cement’s ability to perform its job.
Without the float shoe, there would be no mechanism to control the flow of fluids once the cement has been injected into the well. Drilling mud, which is commonly used in the drilling process, could flow back into the casing after cementing, mixing with the slurry and compromising its quality. This could lead to incomplete or ineffective sealing, with consequences like fluid migration between geological formations, which can cause both production problems and environmental concerns. Moreover, inadequate cement bonding could also result in wellbore instability and create risks of well failure in the future.
The non-return valve in the float shoe is designed to handle the extreme pressures encountered during cementing, ensuring it remains functional throughout the entire process. By effectively preventing backflow, the float shoe ensures that the cement slurry is placed as intended, securing the casing in place and isolating different fluid zones in the wellbore. This is essential for the long-term integrity of the well, as it keeps unwanted fluids from migrating between zones, which could lead to costly repairs and environmental damage.
In summary, the float shoe is an indispensable component of the cementing operation. By preventing the backflow of drilling fluids, it ensures that the cement job is executed effectively, maintaining the integrity of the well. This not only protects the wellbore structure but also helps mitigate risks associated with fluid migration, ensuring a safe, stable, and productive well over its lifecycle. The float shoe’s role in sealing and isolating fluid zones is essential for the success and longevity of any drilling operation.
Float Shoe Helps in Cementing the Well
The float shoe plays a critical role in the cementing process, ensuring that the cement slurry is properly placed in the annular space between the casing and the surrounding formation. Cementing is one of the most important steps in well construction because it serves as a barrier, sealing the wellbore and preventing the migration of unwanted fluids, such as gas, oil, or water, between different geological formations. Without effective cementing, the well may experience fluid migration, leading to potential issues like pressure imbalances, contamination, or even well failure.
Positioned at the bottom of the casing string, the float shoe is a specially designed tool that allows for the proper placement of cement. During cementing, the cement slurry is pumped down through the casing, and the float shoe enables it to flow into the wellbore in a controlled manner. The key feature of the float shoe is its built-in non-return valve, which prevents the backflow of fluids from the wellbore into the casing once the cement is in place. This ensures that the cement slurry remains in the correct position and prevents it from being diluted or contaminated by the fluids in the well.
A successful cementing job is essential for maintaining wellbore stability. The cement provides a solid seal that isolates different fluid zones in the well, ensuring that gas, oil, or water from one formation does not migrate into another. This helps to maintain the integrity of the well and prevents potential environmental hazards. In addition to sealing the wellbore, proper cementing also supports the casing string, helping to prevent collapse and providing the structural stability needed for the well’s long-term operation.
Ultimately, the float shoe ensures that the cementing process is completed effectively and without contamination. By preventing backflow and ensuring proper cement placement, the float shoe guarantees that the well is securely sealed and ready for its intended use, whether for production or storage. This makes the float shoe a vital component in ensuring the safety, efficiency, and longevity of the well throughout its operational life.
Float Shoe Helps Control Pressure During Drilling
Controlling wellbore pressure is one of the most critical aspects of drilling operations, as it ensures the safety and stability of the well. Proper pressure management is essential to prevent accidents such as blowouts, which occur when uncontrolled pressure forces fluids or gases to suddenly escape from the well. In this context, the float shoe plays a crucial role during the cementing phase by helping to regulate well pressure and maintain control.
The float shoe is equipped with a non-return valve that prevents the backflow of drilling fluids into the casing. This feature is particularly important during the cementing process because, without it, there could be a significant risk of destabilizing the well pressure. If drilling fluids were to flow back into the wellbore, it could lead to a loss of pressure control, which might trigger dangerous events like a blowout or fluid migration. The non-return valve in the float shoe ensures that once cement is pumped into the well, it stays in place, maintaining the desired pressure and preventing any backward flow of fluids.
By maintaining a stable pressure environment, the float shoe enables the cementing operation to proceed without complications. The controlled pressure also reduces the risk of creating weak spots or fractures in the wellbore during cement placement. Ultimately, the float shoe helps ensure that the cement job is completed successfully and that the well remains safe and stable throughout drilling and completion. Its role in pressure control is essential for safeguarding the well from potentially catastrophic events and ensuring the integrity of the well over time.
Conclusion
The float shoe is an essential tool for ensuring the successful construction of a well, helping to control pressure, prevent backflow, and ensure proper cementing. With its durable materials, innovative non-return valve, and ability to support well integrity, the float shoe plays a critical role in maintaining the stability of the wellbore, preventing fluid migration, and supporting zonal isolation. Its use ensures that the well is safely and efficiently sealed, protecting the environment and allowing for long-term, successful production.
Choosing the right taper mill for your drilling operation depends on factors such as the well’s depth, formation hardness, and the specific conditions of your project. At WELONG, we specialize in providing high-quality drilling equipment that meets your needs. Our taper mills are designed for durability and efficiency, ensuring you can tackle tough drilling conditions with ease.
For more information or personalized assistance, feel free to contact us at oiltools15@welongpost.com. We’re here to support your drilling operations with top-notch products and reliable service.
References
1. Cementing Operations Handbook – Society of Petroleum Engineers
2. The Role of Float Shoes in Well Construction – Journal of Petroleum Technology
3. Materials and Design for Downhole Tools – Oil and Gas Journal
4. Well Integrity and Pressure Control in Drilling – Offshore Technology Conference
5. Comprehensive Guide to Well Completion and Cementing – SPE Technical Paper Series
6. Float Shoes: Design, Applications, and Performance – International Journal of Drilling Technology

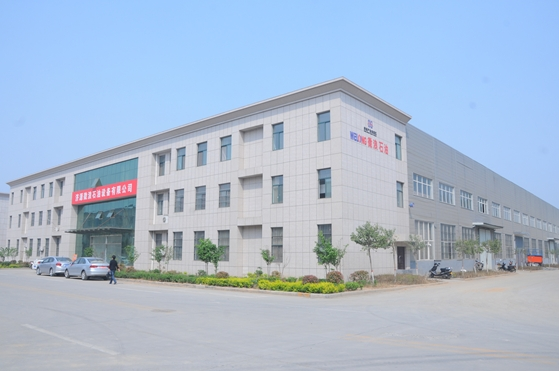
CHINA WELONG - 20+ years manufactuer in oilfield tools
Popular Blogs