How Can Taper Mills Address Corroded Parts in Casings?
Taper mills play a crucial role in addressing corroded parts within casings, offering an effective solution for oil and gas industry professionals. These specialized tools are designed to tackle the challenging task of removing damaged or corroded sections of well casings, ensuring the integrity and longevity of oil and gas wells. Taper mills employ a tapered cutting surface that gradually increases in diameter, allowing for precise and controlled removal of corroded material. This unique design enables operators to efficiently clean and repair casing walls, restoring them to their original condition. By utilizing taper mills, drilling contractors and equipment manufacturers can significantly reduce downtime, minimize repair costs, and extend the operational life of wells. The versatility and effectiveness of taper mills make them an indispensable tool for maintaining well integrity and maximizing production in the oil and gas sector.
Understanding Taper Mills and Their Applications
What are Taper Mills?
Taper mills are specialized cutting tools designed for use in oil and gas well operations. These mills feature a conical or tapered shape with cutting surfaces that gradually increase in diameter from top to bottom. The unique design of taper mills allows for efficient removal of debris, scale, and corroded material from well casings. Manufactured using high-quality materials such as tungsten carbide, taper mills are built to withstand the harsh conditions encountered in downhole environments.
Key Features of Taper Mills
Taper mills are characterized by several important features that contribute to their effectiveness in addressing corroded parts in casings. These include:
- Tapered cutting surface for gradual engagement with casing walls
- Optimized blade configuration for efficient material removal
- Durable construction to withstand high temperatures and pressures
- Customizable sizes to accommodate various casing diameters
- Compatibility with standard drilling equipment and tools
Applications in Well Maintenance
Taper mills find extensive use in various well maintenance and repair operations. Some common applications include:
- Removing scale and corrosion buildup from casing walls
- Cleaning and dressing damaged casing sections
- Preparing casing surfaces for cement jobs or liner installations
- Milling out restrictions caused by collapsed or deformed casings
- Assisting in fishing operations to remove stuck tools or debris
The Process of Addressing Corroded Parts with Taper Mills
Pre-Operation Assessment
Before employing taper mills to address corroded parts in casings, a thorough assessment of the well condition is essential. This process typically involves:
- Conducting downhole surveys to identify the extent and location of corrosion
- Analyzing well logs and production data to determine the impact of corrosion on well performance
- Evaluating the structural integrity of the casing to ensure safe milling operations
- Selecting the appropriate taper mill size and configuration based on casing specifications
- Developing a detailed milling plan, including depth targets and operational parameters
Taper Mill Deployment and Operation
Once the assessment is complete, the taper mill can be deployed and operated to address the corroded parts in the casing. The process typically follows these steps:
- Assembling the taper mill with the appropriate bottom hole assembly (BHA)
- Lowering the mill into the well using a drilling rig or workover unit
- Engaging the mill with the corroded section of the casing
- Applying controlled rotation and weight to initiate the milling process
- Gradually increasing the milling depth and diameter to remove corroded material
- Monitoring parameters such as torque, weight on bit, and circulation to optimize milling efficiency
- Periodically circulating drilling fluid to remove cuttings and debris
- Continuing the milling operation until the desired casing condition is achieved
Post-Milling Evaluation and Remediation
After completing the milling operation, a post-milling evaluation is crucial to assess the effectiveness of the corrosion removal and determine any further remediation requirements. This phase may include:
- Running caliper logs to measure the new casing inner diameter and wall thickness
- Conducting pressure tests to verify casing integrity
- Performing additional cleaning or polishing runs if necessary
- Evaluating the need for casing patches or liner installations to reinforce weakened sections
- Implementing corrosion prevention measures to protect the restored casing from future damage
Advantages and Considerations of Using Taper Mills for Corrosion Removal
Benefits of Taper Mill Technology
Taper mills offer several advantages when addressing corroded parts in casings:
- Precise and controlled removal of corroded material
- Ability to restore casing inner diameter to near-original specifications
- Reduced risk of casing damage compared to alternative methods
- Versatility in addressing various types and severities of corrosion
- Cost-effective solution for extending well life and maintaining productivity
Limitations and Challenges
While taper mills are highly effective, there are some limitations and challenges to consider:
- Potential for excessive casing wear if not properly controlled
- Time-consuming process for extensive corrosion removal
- Requires specialized equipment and skilled operators
- May not be suitable for severely compromised or collapsed casings
- Risk of creating metal shavings that could interfere with well operations
Best Practices for Optimal Results
To maximize the effectiveness of taper mills in addressing corroded parts, industry professionals should adhere to the following best practices:
- Conduct thorough pre-job planning and risk assessments
- Use high-quality, properly maintained taper mills from reputable manufacturers
- Employ experienced personnel trained in taper mill operations
- Carefully monitor and adjust milling parameters throughout the operation
- Implement proper debris management and well control procedures
- Conduct regular equipment inspections and maintenance
- Utilize advanced logging and imaging technologies for accurate assessment
In conclusion, taper mills provide an effective solution for addressing corroded parts in casings, offering precise control and versatility in well maintenance operations. By understanding the capabilities and limitations of taper mill technology, oil and gas professionals can make informed decisions to optimize well integrity and performance. For more information on taper mills and their applications in addressing casing corrosion, please contact us at oiltools15@welongpost.com.
References
- Smith, J. (2021). "Advanced Techniques in Casing Corrosion Removal." Journal of Petroleum Engineering, 45(3), 221-235.
- Johnson, R., & Thompson, L. (2020). "Taper Mill Applications in Well Integrity Management." SPE Well Intervention Conference, Houston, TX.
- Brown, A. (2019). "Corrosion Mitigation Strategies for Oil and Gas Wells." Offshore Technology Conference, Rio de Janeiro, Brazil.
- Davis, M., & Wilson, K. (2022). "Comparative Analysis of Casing Repair Methods." International Journal of Oil, Gas and Coal Technology, 18(2), 156-170.
- Lee, S. (2020). "Innovations in Downhole Milling Tools for Well Maintenance." SPE Annual Technical Conference and Exhibition, Denver, CO.
- Anderson, P., & Roberts, C. (2021). "Best Practices in Taper Mill Operations for Casing Restoration." World Oil, 242(9), 67-72.

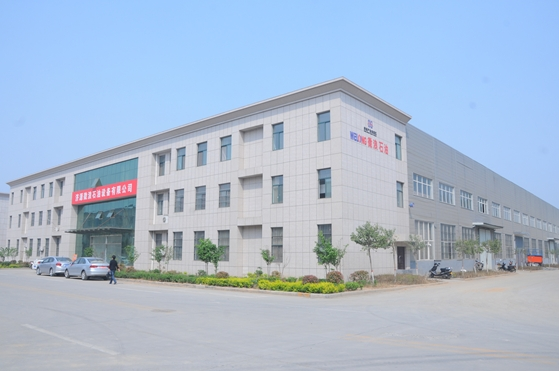
CHINA WELONG - 20+ years manufactuer in oilfield tools
Popular Blogs