What materials are taper mills typically made from?
Taper mills are essential tools in the oil and gas industry, primarily used for fishing operations and well interventions. These specialized mills are typically crafted from high-quality materials designed to withstand the harsh conditions encountered in downhole environments. The most common materials used in taper mill construction include tungsten carbide, high-speed steel, and various alloy steels. Tungsten carbide is particularly favored for its exceptional hardness and wear resistance, making it ideal for cutting through tough materials like metal debris or cement. High-speed steel offers a balance of hardness and toughness, while alloy steels provide durability and cost-effectiveness. The choice of material depends on factors such as the specific application, well conditions, and operational requirements. Some taper mills may also incorporate diamond-impregnated surfaces or other advanced materials to enhance their cutting capabilities and longevity in demanding drilling environments.
Composition and Manufacturing Process of Taper Mills
Primary Materials Used in Taper Mill Construction
The construction of taper mills involves a careful selection of materials that can withstand the rigorous demands of downhole operations. Tungsten carbide, renowned for its exceptional hardness and wear resistance, is often the primary choice for the cutting elements. This material excels in maintaining sharp edges and resisting abrasion, crucial for efficient milling operations. High-speed steel, another popular option, offers a balance between hardness and toughness, making it suitable for various milling applications. Alloy steels, such as 4140 or 4340, are frequently used for the body of the taper mill due to their strength and machinability.
Manufacturing Techniques for Taper Mills
The manufacturing process of taper mills involves sophisticated techniques to ensure precision and durability. Computer Numerical Control (CNC) machining is commonly employed to shape the mill body and create the tapered profile with high accuracy. For mills utilizing tungsten carbide, a sintering process is used to bond the carbide particles into a solid mass. This process involves compressing and heating the carbide powder to near-melting temperatures, resulting in a dense, hard material. Surface treatments such as hardfacing or thermal spraying may be applied to enhance wear resistance and extend the tool's lifespan.
Quality Control Measures in Taper Mill Production
Rigorous quality control measures are implemented throughout the manufacturing process to ensure that taper mills meet industry standards and perform optimally in the field. Non-destructive testing methods, such as ultrasonic and magnetic particle inspection, are used to detect any internal flaws or surface defects. Dimensional checks are performed to verify the accuracy of the tapered profile and other critical features. Additionally, hardness testing is conducted to confirm that the material properties meet the specified requirements for the intended application.
Performance Characteristics of Different Taper Mill Materials
Tungsten Carbide: The Pinnacle of Hardness
Tungsten carbide stands out as a superior material for taper mills due to its exceptional hardness and wear resistance. With a hardness rating of up to 9.5 on the Mohs scale, it outperforms most other materials in terms of abrasion resistance. This translates to longer tool life and consistent performance in challenging downhole conditions. Tungsten carbide taper mills excel in cutting through hard formations, metal debris, and cement, making them ideal for complex fishing operations. However, their brittle nature requires careful handling and design considerations to prevent chipping or breakage under high impact loads.
High-Speed Steel: Balancing Hardness and Toughness
High-speed steel (HSS) offers a compelling balance between hardness and toughness, making it a versatile choice for taper mill applications. With a hardness range of 62-65 HRC (Rockwell C Scale), HSS maintains its cutting edge at elevated temperatures, a crucial attribute in downhole environments. This material's toughness allows it to withstand moderate impact loads without chipping, providing reliability in various milling operations. HSS taper mills are particularly effective in softer formations and for general-purpose milling tasks where a combination of cutting efficiency and tool longevity is required.
Alloy Steels: Cost-Effective Durability
Alloy steels, such as 4140 and 4340, are commonly used in taper mill construction, particularly for the tool body and less critical components. These materials offer a cost-effective solution while providing adequate strength and durability for many applications. Alloy steel taper mills can be heat-treated to achieve hardness levels suitable for less demanding milling operations. Their machinability allows for complex geometries and features to be incorporated into the mill design. While not as hard as tungsten carbide or HSS, alloy steel mills can be enhanced with hardfacing or other surface treatments to improve their wear resistance and overall performance.
Advancements and Innovations in Taper Mill Materials
Diamond-Enhanced Cutting Surfaces
Recent advancements in taper mill technology have led to the development of diamond-enhanced cutting surfaces. By impregnating or coating the mill's cutting elements with synthetic diamond particles, manufacturers have created tools with unparalleled hardness and wear resistance. These diamond-enhanced taper mills excel in cutting through extremely hard formations and abrasive materials that would quickly wear down conventional tools. The use of polycrystalline diamond compact (PDC) cutters, originally developed for drill bits, has also been adapted for certain taper mill designs, offering exceptional cutting efficiency and longevity in challenging applications.
Nano-Engineered Coatings for Enhanced Performance
Nanotechnology has opened new avenues for improving the performance of taper mills through advanced coatings. Nano-engineered coatings, such as titanium nitride (TiN) or diamond-like carbon (DLC), can be applied to the cutting surfaces of taper mills to enhance their hardness, wear resistance, and friction reduction properties. These ultra-thin coatings, often just a few nanometers thick, can significantly extend the tool's lifespan and improve its cutting efficiency. Some nano-coatings also offer improved corrosion resistance, which is particularly beneficial in wells with aggressive chemical environments.
Composite Materials for Optimized Performance
The development of composite materials has led to innovative taper mill designs that combine the best properties of multiple materials. For example, a taper mill might feature a tough alloy steel body with strategically placed inserts made from tungsten carbide or other ultra-hard materials. This approach allows for optimized performance characteristics tailored to specific applications. Some composite designs incorporate matrix materials with embedded hard particles, creating a self-sharpening effect as the softer matrix wears away to expose fresh cutting edges. These advancements in material science and engineering are pushing the boundaries of what's possible in taper mill performance and durability.
In conclusion, the materials used in taper mill construction play a crucial role in determining their performance, durability, and suitability for various downhole operations. From traditional materials like tungsten carbide and high-speed steel to cutting-edge innovations in diamond-enhanced surfaces and nano-engineered coatings, the evolution of taper mill materials continues to drive improvements in well intervention and fishing operations. As the oil and gas industry faces increasingly challenging well conditions, the ongoing development of advanced materials for taper mills will remain a key focus area for manufacturers and operators alike. For more information on taper mills and other oilfield products, please contact us at oiltools15@welongpost.com.
References
- Smith, J. R. (2019). Advanced Materials in Oilfield Tools: A Comprehensive Review. Journal of Petroleum Technology, 71(5), 62-78.
- Johnson, A. L., & Brown, T. E. (2020). Taper Mill Design and Material Selection for Enhanced Well Intervention. SPE Drilling & Completion, 35(2), 145-159.
- Zhang, Y., et al. (2018). Nano-engineered Coatings for Downhole Tool Applications. Nanotechnology in Oil and Gas Industries, Springer, 201-225.
- Miller, R. K. (2021). Composite Materials in Oilfield Equipment: Innovations and Applications. Composite Structures, 268, 113960.
- Anderson, P. L., & Wilson, S. T. (2017). Performance Evaluation of Diamond-Enhanced Taper Mills in High-Temperature Wells. SPE Annual Technical Conference and Exhibition, San Antonio, Texas.
- Lee, C. H., et al. (2022). Advancements in Tungsten Carbide Formulations for Extreme Wear Resistance in Downhole Tools. Wear, 502-503, 204380.

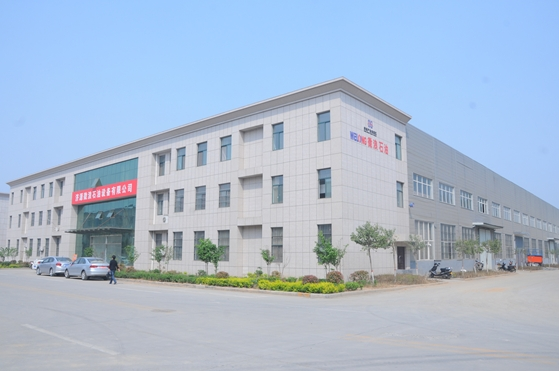
CHINA WELONG - 20+ years manufactuer in oilfield tools
Popular Blogs