What is the best taper mill for steel?
Choosing the best taper mill for steel depends on several factors, including the type of steel, the desired finish, and the machining process requirements. Steel, due to its hardness and density, presents unique challenges when it comes to milling. The ideal taper mill for steel must have robust cutting edges, high heat resistance, and the capability to handle a variety of steel grades. A high-quality taper mill should offer precision and efficiency, with features such as coated carbide tips or high-speed steel (HSS) construction, which helps in resisting wear and improving cutting performance during operations.
In addition, it is crucial to select a taper mill that suits the specific steel milling task, whether it’s for finishing, roughing, or creating angled geometries. The best taper mills for steel should balance cutting speed, tool life, and accuracy, ensuring a smooth milling process with minimal wear. Ultimately, the right taper mill enhances productivity, reduces cycle times, and improves the overall quality of the finished steel components.
Factors to Consider When Choosing the Best Taper Mill for Steel
When selecting the best taper mill for steel, several factors must be considered to ensure the tool is well-suited for the specific application. Understanding these elements can make the difference between achieving optimal machining results and encountering issues like excessive tool wear or poor surface finishes.
1. Material Type and Hardness
The first factor to consider is the specific type of steel being machined. Steel comes in various grades, such as carbon steel, stainless steel, and alloy steel, each with different hardness levels. A taper mill designed for machining softer materials may not perform well on harder steel grades. For instance, high-speed steel (HSS) taper mills are generally suitable for lower hardness materials, while carbide-coated taper mills are more appropriate for harder grades of steel. Choosing the right material for your taper mill ensures longer tool life and better performance.
2. Cutting Speed and Feed Rate
The cutting speed and feed rate are key parameters when choosing a taper mill. Steel is a relatively tough material, and selecting a taper mill that can withstand high cutting speeds while maintaining stability is critical. Too high a feed rate can cause the tool to overheat, while too slow a feed rate might result in unnecessary tool wear. A good taper mill should allow for controlled and optimized cutting conditions, depending on the type of steel being used. High-performance carbide or coated taper mills generally perform better under higher speeds and feeds.
3. Tool Coatings
The coating on a taper mill significantly impacts its performance, especially when cutting steel. TiN (Titanium Nitride), TiAlN (Titanium Aluminum Nitride), and diamond-like carbon (DLC) coatings provide additional wear resistance, heat resistance, and improved chip evacuation. Coatings help to prolong tool life, improve surface finishes, and reduce the likelihood of heat-related tool failure. When working with steel, particularly tougher grades, it is essential to choose a taper mill with an appropriate coating to optimize performance and extend tool life.
4. Flute Geometry and Cutting Depth
The geometry of the taper mill’s flute plays an essential role in chip removal and cutting efficiency. For steel, a taper mill with deep flutes and an appropriate helix angle helps ensure smooth chip removal, reducing the risk of tool clogging and improving surface quality. The cutting depth is also crucial, especially when dealing with thicker steel components. A shorter cutting depth often helps maintain better control over the milling process, while deeper cuts require a taper mill capable of withstanding the increased stress.
5. Tool Life and Cost Efficiency
Considering the tool life is crucial when selecting a taper mill for steel, as frequent tool replacements can be costly and time-consuming. Carbide taper mills generally offer a longer tool life compared to high-speed steel tools, making them ideal for heavy-duty operations. However, carbide tools are more expensive. Choosing a taper mill that offers the best balance between tool longevity and cost-efficiency ensures profitability while maintaining high machining standards.
6. Machining Application
Lastly, it is important to determine the specific machining application for which the taper mill is intended. Some taper mills are designed for roughing operations, while others are better suited for finishing cuts. For example, roughing taper mills are often more robust and designed to handle large volumes of material removal, while finishing taper mills offer finer details, smoother finishes, and superior edge quality. Selecting the correct taper mill for the job will help achieve the desired results efficiently and with minimal wear on the tool.
Top Features of a High-Quality Taper Mill for Steel Milling
When selecting a taper mill for steel milling, it’s crucial to focus on features that enhance the tool’s performance and longevity. High-quality taper mills come with specific design elements that optimize their ability to handle steel, ensuring precision, efficiency, and reduced wear over time. Here are the top features you should look for:
1. Durable and Wear-Resistant Coatings
A taper mill’s coating is one of the most critical features, especially when working with tough materials like steel. Coatings not only protect the tool but also enhance its cutting performance. Titanium Nitride (TiN) and Titanium Aluminum Nitride (TiAlN) are among the most common coatings for taper mills used in steel machining. These coatings provide exceptional wear resistance, making them ideal for prolonged use in harsh conditions. They also help reduce friction, allowing for smoother cutting and better surface finishes.
In addition to improving tool life, these coatings help to dissipate heat more effectively, reducing the risk of heat build-up, which is a common issue when milling hard steels. The right coating can also reduce the likelihood of tool chipping, a common problem when machining steel.
2. Precise Taper Angles
A high-quality taper mill will feature an accurate and consistent taper angle, which is crucial for ensuring precision when cutting steel parts. The taper angle determines the geometry of the cut, which directly affects the fit and functionality of the finished part. Mills with adjustable taper angles are especially versatile, allowing for different cutting applications depending on the specifications of the job.
For steel, a taper mill with an optimal angle will provide cleaner cuts, better surface finishes, and more precise angles, making it suitable for complex applications where accuracy is paramount, such as in aerospace or automotive industries.
3. Helix Angle for Enhanced Chip Removal
The helix angle of a taper mill is another feature that impacts its cutting efficiency. A high helix angle helps increase the cutting speed and ensures efficient chip removal, which is particularly important when machining steel. Steel, being a tough material, tends to generate heat and pressure during the cutting process. A taper mill with a well-designed helix angle will facilitate better chip flow, preventing material build-up and reducing the likelihood of tool wear due to excessive heat.
The cutting edge geometry and the shape of the flute can also affect how well the chips are removed. Mills with wide flutes are generally better for steel, as they provide more room for chips to escape, keeping the tool from becoming clogged and improving the overall machining process.
4. Carbide Material for Enhanced Durability
Carbide is one of the most durable materials used in taper mills. Carbide-tipped taper mills or solid carbide taper mills are particularly well-suited for steel machining due to their high hardness and heat resistance. These tools are capable of handling high-speed operations and maintaining their cutting efficiency over longer periods of use. Carbide’s superior wear resistance means it will last longer and provide better performance compared to high-speed steel (HSS) mills, making it ideal for cutting tougher steel alloys.
Carbide taper mills are especially useful for high-volume machining processes, such as roughing operations, where the tool needs to handle substantial material removal without significant wear.
5. Low Vibration and High Stability
A high-quality taper mill should offer low vibration during operation, which contributes to better cutting accuracy and surface finishes. Vibration can cause chatter, which negatively impacts the machining process and reduces tool life. Taper mills designed with vibration-damping features, such as solid carbide shanks or optimized flute geometry, are essential for maintaining stability and ensuring smooth cuts, especially when machining steel.
Additionally, high stability ensures that the tool maintains its shape and cutting edge, even during challenging tasks like deep cuts or high-feed-rate operations. Stability is also crucial when working with high-tensile-strength steels, as it helps prevent tool deflection, which can lead to inaccurate cuts or damage to the material.
6. High Precision and Tight Tolerances
For steel machining, precision is key. A high-quality taper mill should be designed to meet tight tolerances to achieve the exact dimensions required. Tools that are manufactured with high precision ensure minimal deviation during the cutting process, leading to more accurate and repeatable results. Whether for roughing, finishing, or complex milling operations, the mill should provide consistency in every cut, reducing the need for rework or adjustments.
High-precision taper mills also contribute to the quality of the finished surface, an important factor when machining steel for applications that demand superior surface integrity, such as in the aerospace, automotive, and oil and gas industries.
How to Optimize Taper Milling for Steel Parts?
Optimizing taper milling for steel involves understanding the specific requirements of steel machining and leveraging the right strategies to enhance tool performance, precision, and efficiency. Whether you are working with high-carbon steels, stainless steels, or alloys, optimizing the milling process will help you achieve superior results while prolonging the life of the taper mill.
1. Choosing the Right Cutting Parameters
One of the most important factors in optimizing taper milling for steel is selecting the correct cutting parameters. This includes feed rate, spindle speed, and depth of cut. These parameters should be adjusted based on the type of steel you’re machining, its hardness, and the specific operation you're performing.
Feed Rate: For steel milling, a moderate to high feed rate is often recommended, as it helps increase material removal rates. However, too high of a feed rate can cause tool wear, chatter, or overheating. It's important to find a balance based on your mill's capabilities.
Spindle Speed: When cutting steel, maintaining the correct spindle speed is essential. A higher spindle speed allows for faster cuts and helps to prevent tool wear. However, for harder steels, it’s often better to reduce the spindle speed to avoid excessive heat generation.
Depth of Cut: Adjusting the depth of cut is critical in taper milling. Shallow cuts reduce tool wear and heat generation, but deeper cuts allow for faster material removal. For steel, taking multiple shallow passes can help prevent tool failure while ensuring smooth, accurate cuts.
2. Utilizing the Right Cutting Tools
Using the right cutting tools is essential to achieve optimal performance in steel taper milling. High-quality carbide taper mills with specialized coatings and geometries, as discussed earlier, offer superior wear resistance and heat tolerance, which are crucial when working with tough materials like steel.
Moreover, selecting the right type of taper mill for the specific operation can help maximize efficiency. For example:
Roughing Mills: These are designed to remove material quickly and are ideal for initial cuts. They usually have fewer teeth and a larger chip space, which allows them to cut aggressively without clogging.
Finishing Mills: When a finer surface finish is needed, a finishing taper mill with more teeth and finer geometry can provide smooth cuts and excellent precision.
Ball Nose Mills: These mills, which feature a rounded tip, are ideal for milling curved surfaces, making them perfect for creating complex geometries or parts with intricate tapered features.
By using the right tool for the job, you can improve both the quality and efficiency of your milling operation.
3. Optimizing Coolant and Lubrication
Coolant and lubrication play a significant role in taper milling, particularly when working with steel. Steel can generate substantial heat during the cutting process, which can cause tool wear and material deformation. To optimize the milling process, use high-performance cutting fluids that can provide adequate cooling and lubrication.
Flood Cooling: This method involves applying a large amount of coolant to the cutting area, which helps dissipate heat and keeps the taper mill cool. This is particularly effective for heavy cuts or high-feed milling operations.
Through-Spindle Coolant: For better precision and more efficient heat dissipation, using tools with through-spindle coolant capabilities is ideal. This allows coolant to flow directly to the cutting area, keeping the tool cool and flushing away chips to prevent clogging.
By maintaining an appropriate coolant system, you ensure that your taper mill operates at optimal temperatures, minimizing the risk of damage to the tool or the steel part.
4. Maintaining Tool Condition and Sharpness
Tool maintenance is another essential factor in optimizing taper milling. Over time, taper mills can experience wear, leading to dull cutting edges. This wear can increase friction, heat, and vibration, resulting in lower cutting performance and poorer surface finishes. Regular inspection and maintenance of your taper mills are crucial.
Resharpening: When the cutting edges begin to dull, it's advisable to resharpen the taper mill. Keeping the tool sharp ensures that it maintains its cutting efficiency, improves the quality of the finished part, and reduces the chances of tool failure.
Tool Inspection: Regularly inspect your taper mills for signs of damage, such as cracks or chips on the cutting edges. Early detection of wear can help prevent significant tool failure during milling operations.
Additionally, consider using tool life management strategies to track when tools need to be replaced or resharpened. Using a worn-out tool can result in longer cycle times, increased tool wear, and reduced accuracy.
5. Minimizing Vibration and Chatter
Vibration and chatter can significantly affect the efficiency of taper milling, especially when working with steel. These issues not only lead to poor surface finishes but can also cause tool deflection, leading to inaccurate cuts and increased tool wear. To minimize vibration:
Use Rigid Tool Holders: Ensure the taper mill is securely mounted with the correct tool holder. A rigid tool holder minimizes vibration, providing stability during milling operations.
Optimize Cut Depth and Feed Rate: As mentioned earlier, using moderate depths of cut and balanced feed rates can reduce the chances of vibration and chatter. Take smaller cuts to avoid overstressing the tool and workpiece.
Proper Machine Setup: Make sure that your milling machine is properly calibrated and that the workpiece is securely fixtured. A stable setup helps prevent unnecessary vibrations during the cutting process.
6. Leveraging Advanced Technology
Modern CNC milling machines come equipped with advanced features that help optimize taper milling operations. Utilizing features such as adaptive machining and real-time tool condition monitoring can improve the precision and efficiency of the milling process.
Adaptive machining allows the machine to adjust cutting parameters in real-time based on the material and cutting conditions. This ensures that the tool is always performing at its best, even when cutting tough materials like steel.
In addition, tool condition monitoring systems provide real-time feedback on the tool’s performance, alerting operators when the tool is wearing out or when adjustments need to be made to the cutting parameters.
Comparing Taper Mills: Which One is Best for Steel?
When selecting the best taper mill for steel, it is crucial to compare various options based on performance, durability, and precision. Steel is a versatile yet tough material, and using the right taper mill for the job can significantly improve machining efficiency and part quality. Below, we compare different taper mills to help you make an informed decision.
1. Carbide Taper Mills vs. High-Speed Steel Taper Mills
The choice between carbide taper mills and high-speed steel (HSS) taper mills is one of the most fundamental decisions when selecting a taper mill for steel.
Carbide Taper Mills: These mills are known for their excellent hardness, wear resistance, and ability to withstand high cutting temperatures. Carbide mills are ideal for machining harder steels, such as stainless steel or tool steel, because they maintain their sharpness longer than HSS mills. They also provide superior precision and a better surface finish, making them a top choice for high-performance applications. However, carbide mills are more brittle than HSS, which means they are more prone to breakage if not handled properly.
HSS Taper Mills: HSS taper mills are more flexible than carbide tools, making them less likely to chip or break under heavy cutting conditions. While they have lower wear resistance than carbide mills, they are often more cost-effective for general-purpose milling. HSS mills are suitable for softer steels or less demanding machining tasks. They also perform better under shock loading due to their toughness, making them a good choice for rough milling or intermittent cuts.
In general, for steel machining, carbide taper mills are the preferred choice for their long-term cost-effectiveness in terms of tool life and overall performance. However, for smaller-scale or more economical operations, HSS taper mills may be sufficient.
2. Coated vs. Uncoated Taper Mills
Another key factor in selecting the best taper mill for steel is the choice between coated and uncoated mills. Coatings enhance the performance of the taper mill by providing additional protection against wear, heat, and corrosion.
Coated Taper Mills: Coatings like TiN (Titanium Nitride), TiAlN (Titanium Aluminum Nitride), and AlTiN (Aluminum Titanium Nitride) are commonly applied to carbide taper mills. These coatings increase the tool's surface hardness and improve wear resistance, which is crucial when milling tough materials like steel. Coated mills can also withstand higher cutting temperatures, reducing the chances of tool failure and prolonging the tool’s life. For steel milling, a coated carbide taper mill can deliver outstanding performance and cost savings over time.
Uncoated Taper Mills: Uncoated mills may offer lower initial costs and are suitable for less demanding operations or softer steels. However, they are more prone to wear and require more frequent tool changes compared to coated mills. If you’re machining relatively soft steel or working on less abrasive tasks, an uncoated taper mill could be a suitable option.
For steel milling, particularly when precision, durability, and high cutting speeds are essential, coated taper mills generally offer the best performance and value.
3. Single-Flute vs. Multi-Flute Taper Mills
The number of flutes on a taper mill directly influences its cutting performance, chip removal capacity, and the type of operation it's suited for.
Single-Flute Taper Mills: These mills have one cutting edge, which is advantageous for high-speed cutting and chip removal in specific operations, such as finishing or when cutting through soft or thin materials. They excel at preventing chip clogging, which is a common problem when milling steel. However, they typically provide a rougher finish and may not be as suitable for applications requiring high precision.
Multi-Flute Taper Mills: Multi-flute taper mills (with two, three, or more flutes) are commonly used for steel milling, as they provide a better finish and are more efficient for high-precision applications. The increased number of flutes allows for more cutting edges to engage the material, which increases the tool’s longevity, produces smoother finishes, and reduces cutting forces. Multi-flute taper mills are ideal for tasks such as finishing or creating accurate taper angles, making them the go-to option for high-performance steel machining.
For steel milling, a multi-flute taper mill is generally the best choice, especially for precision operations and smooth finishes.
4. End Mill Geometry and Taper Angle
The geometry of a taper mill’s cutting edges and the taper angle can significantly affect its performance and suitability for specific steel milling applications.
General-Purpose Taper Mills: These mills have standard geometries and angles, making them versatile tools suitable for a wide range of applications. They are excellent for general-purpose milling of steel, from roughing to finishing tasks.
Specialized Taper Mills: For specific applications, such as deep cavities, tapered holes, or features that require high precision, specialized taper mills with custom geometries are available. These mills may have specific rake angles or cutting-edge shapes designed for enhanced performance with steel. Some taper mills are optimized for helical cutting, which can improve chip evacuation and reduce cutting forces.
When working with steel, customized taper mills with specialized geometry may be needed for highly demanding or precision-dependent tasks. For general-purpose milling, a standard general-purpose taper mill will usually suffice.
5. Size and Reach
The size and reach of a taper mill also play an important role in choosing the right tool for your steel milling operations. A taper mill with an extended reach may be necessary for deep or hard-to-reach cavities, while a shorter tool can provide better rigidity and precision for shallow cuts.
Short-Reach Taper Mills: These mills provide increased rigidity and are better for high-precision applications where minimal deflection is needed. They are ideal for smaller parts or situations where accuracy is the primary concern.
Long-Reach Taper Mills: For applications that require accessing deep holes or other hard-to-reach areas, long-reach taper mills are necessary. However, these mills can be less rigid and may experience more deflection, which could affect the finish and precision. They are best used in operations where access is more important than absolute precision.
For steel milling, short-reach taper mills are generally the best option for ensuring precise cuts and long tool life, while long-reach taper mills should only be used when access to deep areas is required.
How Does a Taper Mill Improve Steel Machining Efficiency?
The efficiency of machining steel can be greatly influenced by the type of milling tool used. A taper mill is designed to not only create tapered features but also to improve overall machining productivity, especially when working with hard materials like steel. Here’s how taper mills contribute to improving machining efficiency for steel parts:
1. Improved Chip Removal and Cooling
One of the primary challenges when machining steel is the removal of chips and the cooling of the cutting zone. As steel is a tough material, it generates a significant amount of heat during the milling process, which can quickly lead to tool wear and reduced machining efficiency. Taper mills are specifically designed with flute geometry that facilitates better chip removal. Their helix angles and flute design allow for smoother cutting paths and more effective evacuation of chips, ensuring that the cutting zone stays cooler and preventing overheating.
With more efficient chip removal, the cutting edges of the taper mill stay cleaner, which reduces the risk of re-cutting chips. This allows for continuous, uninterrupted machining without the need for frequent tool changes, thereby improving efficiency and reducing downtime.
2. Minimized Cutting Forces
When machining steel, the cutting forces involved can be significant, leading to increased tool wear, vibration, and even damage to the workpiece. Taper mills are designed to reduce cutting forces, particularly in challenging operations like finishing or deep milling. The geometry of the taper mill's cutting edge, along with its tapered form, allows for more controlled cutting and helps distribute forces more evenly across the cutting surface.
By minimizing cutting forces, taper mills reduce the likelihood of tool deflection and vibration, which can negatively affect part quality and machining efficiency. As a result, you can achieve better precision while using less power and maintaining longer tool life. This efficiency directly translates into reduced operational costs and higher throughput.
3. Precision and Accuracy for Complex Geometries
Steel parts often require precise, intricate shapes, including angled features, slots, or tapered holes. Taper mills are built with the ability to produce precise tapered angles, which is a vital feature in applications such as aerospace, automotive, and tooling industries. The mill’s tapered design and multi-flute construction ensure that these features are machined with a high degree of accuracy.
Additionally, taper mills offer enhanced control over depth of cut and angle precision, ensuring that the milled parts adhere strictly to the desired tolerances. This high level of precision eliminates the need for secondary operations, reducing the overall time required for machining and improving the efficiency of production lines.
4. Ability to Tackle Multiple Operations Simultaneously
In many steel machining applications, multiple operations (e.g., roughing, finishing, and tapering) need to be performed on the same part. Taper mills are versatile enough to handle these different operations, reducing the need for multiple tools. For example, multi-flute taper mills can perform both roughing and finishing cuts, saving time by eliminating the need to change tools mid-operation. This versatility allows for more continuous, efficient milling, leading to increased throughput.
In addition, taper mills’ ability to create both tapered features and straight cuts makes them suitable for a wide range of tasks, from cavity milling to edge trimming and everything in between. This multi-functionality leads to a more streamlined workflow and fewer tool changes, improving machining efficiency in steel production.
5. Enhanced Surface Finish
Achieving a high-quality surface finish on steel parts is crucial in many industries, particularly those where precision and aesthetics matter. Taper mills are designed to produce smoother, more consistent finishes compared to conventional end mills. The combination of sharp cutting edges, smooth chip flow, and optimized cutting paths results in a better surface finish with fewer imperfections.
By improving the surface quality, taper mills reduce the need for post-machining operations, such as polishing or sanding, which further enhances machining efficiency. In sectors like aerospace or medical device manufacturing, where surface integrity is essential, taper mills offer a clear advantage in terms of both quality and productivity.
Common Issues When Using a Taper Mill for Steel Milling
While taper mills offer several advantages in terms of efficiency, precision, and cost savings, they are not without their challenges. Steel, as a material, presents unique difficulties in machining, and taper mills must be carefully selected and maintained to avoid common issues. Below, we will explore the primary issues encountered when using taper mills for steel milling and provide solutions to mitigate these challenges.
1. Tool Wear and Fatigue
Steel is a hard, abrasive material, which makes it highly demanding on cutting tools. Taper mills are particularly prone to wear due to the sustained high-pressure contact between the tool and the steel during milling. Over time, this wear can lead to tool fatigue, where the mill becomes less effective at cutting and may even cause part defects or damage.
Solution:
To mitigate tool wear, it’s essential to use taper mills made from materials designed to withstand harsh conditions, such as carbide or coated carbide. These materials are not only harder but also resistant to high temperatures, which are common in steel milling. Additionally, it’s important to monitor the cutting speed and feed rates to ensure they are optimized for steel. Reducing the tool load and using coolant to manage temperature can also extend tool life.
2. Vibration and Chatter
Vibration, or chatter, is one of the most common problems in machining operations, and it can be especially problematic when using taper mills on steel. Chatter occurs when the cutting tool oscillates during milling, creating poor surface finishes and reducing the precision of the part. It is often caused by issues such as incorrect cutting parameters, tool wear, or unstable workpiece setups.
Solution:
To minimize chatter, make sure that the workpiece is securely clamped and that the spindle speed and feed rates are set correctly. Lower speeds combined with appropriate feed rates often help reduce vibrations. Using dampening tools or vibration-absorbing fixtures can also reduce the impact of chatter. Additionally, taper mills with variable helix angles can help alleviate this issue by improving the cutting action and reducing the likelihood of resonant frequencies that lead to vibrations.
3. Tool Deflection
Tool deflection occurs when the cutting forces are too high for the tool to maintain rigidity during the milling process, causing the tool to bend or flex. This is particularly problematic when milling steel parts that require high precision, as deflection can lead to dimensional inaccuracies. The geometry of the taper mill itself, including the length of the tool, can exacerbate this issue.
Solution:
To avoid tool deflection, ensure that the taper mill selected is appropriate for the depth and complexity of the cut. Shorter taper mills or mills with stiffer shanks provide more rigidity and are less prone to deflection. Additionally, using the right toolpath strategies, such as climb milling instead of conventional milling, can help distribute cutting forces more evenly and reduce the risk of deflection.
4. Inadequate Chip Removal
Steel milling generates a significant amount of chips, and poor chip removal can cause them to recirculate back into the cutting zone, leading to re-cutting, tool wear, and overheating. A clogged cutting zone can significantly reduce the milling efficiency and quality of the steel part being machined.
Solution:
Flute design plays a crucial role in chip removal. Choosing a taper mill with the right number and shape of flutes for steel is essential. A tool with more flutes provides better chip evacuation but may reduce the overall cutting efficiency at lower speeds. Using high-pressure coolant or air jets can help clear the cutting zone more effectively and prevent chip recirculation. Regularly checking the chip removal system to ensure it is functioning optimally is another key step in preventing this issue.
5. Heat Generation and Tool Overheating
Steel machining generates substantial heat, and without proper temperature management, overheating can occur. When taper mills become overheated, it not only accelerates tool wear but can also distort the material, leading to inaccuracies in the machined part. Tool overheating is especially problematic when using high-speed steel (HSS) taper mills or when operating at high cutting speeds.
Solution:
Using high-performance coatings on the taper mill, such as TiAlN or AlTiN, can improve heat resistance and prevent premature tool failure due to excessive temperatures. Additionally, ensuring that the cooling system is working properly and using flood coolant or through-tool coolant systems can keep the tool and workpiece at a manageable temperature. Choosing the right cutting speeds and feeds for steel also helps in balancing heat generation and tool longevity.
Conclusion
Choosing the right taper mill for steel milling is critical to optimizing both the quality and efficiency of your machining operations. A high-quality taper mill can provide significant benefits, including improved precision, reduced cutting forces, and the ability to create angled features and tapered holes. However, common challenges such as tool wear, vibration, and chip removal must be addressed proactively. By selecting the appropriate taper mill, using optimal machining parameters, and maintaining the tools properly, you can overcome these issues and achieve the desired outcomes in steel machining.
The ideal taper mill for your steel applications will depend on various factors, such as the type of steel, the part geometry, and the specific machining requirements. With careful consideration and the right tooling, taper mills can significantly enhance your machining processes and deliver excellent results.
For more information or to find the best taper mill for your steel machining needs, feel free to contact us at at oiltools15@welongpost.com. Our team of experts is ready to assist you in choosing the right tools to meet your specific needs.
References
1. Fundamentals of Milling – Engineering Materials Handbook, ASM International
2. The Practical Guide to Milling and Machining – SME Technical Paper Series
3. Machining Steel: Techniques and Best Practices – Modern Machine Shop
4. Tooling for Steel: Innovations and Improvements – Cutting Tool Engineering
5. Advanced Milling Techniques for Steel Parts – Manufacturing Engineering Journal
6. The Impact of Tool Wear in Steel Machining – International Journal of Precision Engineering

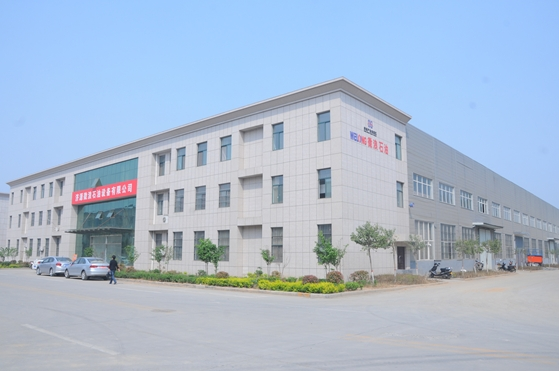
CHINA WELONG - 20+ years manufactuer in oilfield tools
Popular Blogs