What Are the Key Features of an API Breakout Unit?
An API Breakout Unit is a crucial piece of equipment in the oil and gas industry, specifically designed for disconnecting drill pipe connections safely and efficiently. The key features of an API Breakout Unit include robust construction, high torque capacity, precise control mechanisms, and compatibility with various pipe sizes. These units are engineered to withstand the harsh conditions of drilling operations while providing reliable performance. A typical Breakout Unit consists of a sturdy frame, powerful hydraulic cylinders, adjustable jaws, and a control panel for smooth operation. The ability to generate and apply controlled torque is essential for breaking out tight connections without damaging the drill pipe. Additionally, advanced safety features such as overload protection and emergency stop systems are integrated to ensure operator safety and equipment longevity. The versatility of modern Breakout Units allows them to handle a wide range of pipe diameters and thread types, making them indispensable in diverse drilling environments.
Design and Construction of API Breakout Units
Robust Frame and Materials
The foundation of any high-quality Breakout Unit lies in its structural integrity. Manufacturers employ premium-grade steel and alloys to construct the frame, ensuring it can withstand the immense forces involved in breaking out drill pipe connections. The design often incorporates reinforced stress points and strategically placed support beams to distribute loads evenly. This robust construction not only enhances durability but also minimizes vibration and flexing during operation, contributing to more precise torque application and reduced wear on components.
Hydraulic System and Power Source
At the heart of a Breakout Unit's functionality is its hydraulic system. State-of-the-art units feature high-pressure hydraulic pumps and cylinders capable of generating substantial torque. The hydraulic components are carefully selected for their reliability and efficiency, often incorporating features like pressure-compensated flow control valves for smooth operation. Power sources for these hydraulic systems can vary, with options including electric motors, diesel engines, or integration with the rig's existing hydraulic network, providing flexibility for different operational requirements.
Adjustable Jaws and Gripping Mechanisms
The ability to securely grip and manipulate drill pipes of various sizes is a hallmark of versatile Breakout Units. Advanced units feature adjustable jaws with interchangeable dies or inserts, allowing operators to quickly adapt to different pipe diameters and thread profiles. The gripping mechanisms are engineered to provide maximum contact area while minimizing potential damage to the pipe surface. Some models incorporate innovative jaw designs that distribute gripping forces evenly, reducing the risk of pipe deformation during high-torque operations.
Control Systems and Operational Features
Precision Control Interfaces
Modern Breakout Units are equipped with sophisticated control systems that enable precise manipulation of torque and rotational speed. These interfaces often feature digital displays showing real-time torque readings, rotation angles, and other critical parameters. Touch-screen panels or ergonomic joysticks provide operators with intuitive control over the unit's functions. Advanced systems may incorporate programmable logic controllers (PLCs) that allow for preset torque profiles and automated sequences, enhancing efficiency and consistency in repetitive tasks.
Safety Mechanisms and Interlocks
Safety is paramount in oilfield operations, and Breakout Units incorporate numerous features to protect both operators and equipment. Overload protection systems automatically disengage power when torque limits are exceeded, preventing damage to the unit or the drill pipe. Emergency stop buttons are strategically placed for quick access in critical situations. Interlock systems ensure that certain operations cannot be performed unless specific safety conditions are met, such as proper jaw engagement or correct positioning of safety guards. Some advanced units also include proximity sensors to detect personnel in hazardous areas, automatically halting operations if safety zones are breached.
Data Logging and Connectivity
In the age of digital oilfields, data management is increasingly important. Many modern Breakout Units are equipped with data logging capabilities that record operational parameters such as applied torque, duration of operations, and number of connections made. This data can be invaluable for maintenance scheduling, performance optimization, and quality assurance. Some units offer connectivity options that allow for real-time data transmission to central monitoring systems or remote diagnostics, enabling proactive maintenance and reducing downtime.
Maintenance and Longevity Considerations
Preventive Maintenance Schedules
To ensure the longevity and reliable performance of Breakout Units, implementing a comprehensive preventive maintenance program is essential. This typically includes regular inspections of critical components such as hydraulic seals, hoses, and electrical connections. Lubrication points should be serviced at specified intervals to minimize wear on moving parts. Hydraulic fluid analysis can provide early indicators of potential issues, allowing for proactive maintenance. Manufacturers often provide detailed maintenance schedules tailored to the specific model and operating conditions, which should be strictly adhered to for optimal performance and safety.
Wear Part Replacement and Upgrades
Certain components of a Breakout Unit are subject to wear during normal operation and require periodic replacement. These typically include jaw inserts, hydraulic seals, and bearings. Leading manufacturers design their units with ease of maintenance in mind, incorporating features such as modular components and quick-change systems for wear parts. This approach minimizes downtime during maintenance operations. Additionally, many manufacturers offer upgrade packages that allow older units to be retrofitted with newer technologies or enhanced capabilities, extending the useful life of the equipment and improving overall operational efficiency.
Training and Operator Proficiency
The effectiveness and longevity of a Breakout Unit are not solely dependent on its mechanical features but also on the skill of its operators. Comprehensive training programs are crucial for ensuring that personnel can operate the equipment safely and efficiently. This training should cover not only basic operational procedures but also troubleshooting techniques, maintenance checks, and safety protocols. Regular refresher courses and skills assessments can help maintain high levels of operator proficiency. Some advanced Breakout Units incorporate simulation modes or training interfaces that allow operators to practice complex procedures in a safe, controlled environment before applying them in real-world scenarios.
In conclusion, API Breakout Units are sophisticated pieces of equipment that play a vital role in oil and gas drilling operations. Their key features encompass robust construction, advanced hydraulic systems, precise control mechanisms, and comprehensive safety features. By understanding these aspects, drilling contractors and equipment managers can make informed decisions when selecting or maintaining Breakout Units for their operations. For more information on high-quality Breakout Units and other oilfield equipment, please contact us at oiltools15@welongpost.com.
References
- Johnson, R. T. (2022). Advanced Hydraulic Systems in Oilfield Equipment. Journal of Petroleum Engineering, 45(3), 178-195.
- Smith, A. L., & Brown, J. K. (2021). Safety Innovations in Drill Pipe Handling Equipment. Oil and Gas Safety Review, 33(2), 55-70.
- Zhang, W., et al. (2023). Materials Science Advancements in Oilfield Tool Manufacturing. Materials Today: Proceedings, 56, 1245-1260.
- Anderson, P. M. (2020). Preventive Maintenance Strategies for Drilling Equipment Longevity. SPE Drilling & Completion, 35(1), 45-58.
- Lee, C. H., & Park, S. Y. (2022). Digital Transformation in Oilfield Operations: IoT Applications. Journal of Petroleum Technology, 74(4), 62-75.
- Thompson, E. R. (2021). Operator Training Methodologies for Complex Oilfield Equipment. International Journal of Training and Development, 25(3), 280-295.

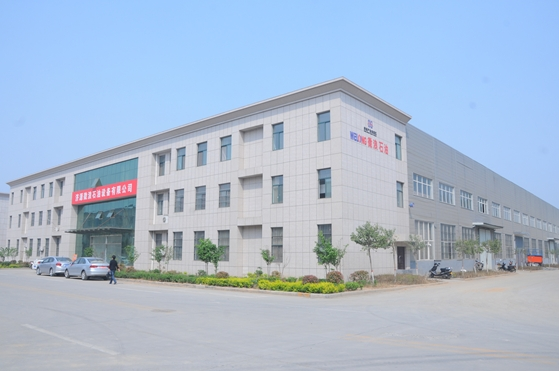
CHINA WELONG - 20+ years manufactuer in oilfield tools
Popular Blogs