What Are the Key Features of a High-Quality Taper Mill?
A high-quality taper mill is an essential tool in the oil and gas industry, specifically designed for efficient wellbore cleanup and fishing operations. The key features of a top-tier taper mill include robust construction, precision-engineered cutting structures, optimal taper angle, and durable materials. These mills are crafted to withstand the harsh downhole environments while effectively removing obstructions, debris, and unwanted materials from the wellbore. The tapered design allows for smooth entry into restricted areas, gradually increasing the milling diameter as it progresses. Superior taper mills also incorporate advanced metallurgy to enhance wear resistance and cutting efficiency. They are engineered to maintain dimensional stability under high temperatures and pressures, ensuring consistent performance throughout the milling operation. Additionally, high-quality taper mills often feature optimized fluid circulation channels to improve cuttings evacuation and prevent tool sticking. These features, combined with stringent quality control measures during manufacturing, contribute to the overall reliability and effectiveness of a premium taper mill in critical downhole applications.
Design and Construction of High-Performance Taper Mills
Innovative Cutting Structures
The cutting structure of a taper mill is a critical component that directly impacts its performance. High-quality mills feature innovative designs that maximize cutting efficiency while minimizing wear. These structures often incorporate strategically placed carbide inserts or diamond-impregnated segments to enhance cutting ability across various formations. The arrangement and geometry of the cutting elements are carefully engineered to provide optimal chip formation and removal, ensuring a smooth and consistent milling process.
Material Selection and Metallurgy
The choice of materials used in taper mill construction plays a vital role in its durability and performance. Premium mills utilize high-grade steels and alloys that offer exceptional strength and resistance to abrasion, corrosion, and high temperatures. Advanced heat treatment processes are applied to enhance the material properties further, resulting in a tool that can withstand the rigors of demanding downhole environments. Some manufacturers also incorporate specialized coatings or surface treatments to improve wear resistance and extend the operational life of the mill.
Precision Manufacturing Techniques
High-quality taper mills are produced using state-of-the-art manufacturing techniques that ensure dimensional accuracy and consistency. Computer-aided design (CAD) and computer-aided manufacturing (CAM) systems are employed to create precise tool geometries and maintain tight tolerances. Advanced machining processes, such as multi-axis CNC milling and electrical discharge machining (EDM), are utilized to achieve complex shapes and surface finishes. These precision manufacturing methods contribute to the overall quality and reliability of the taper mill, ensuring optimal performance in challenging well conditions.
Optimizing Taper Mill Performance for Various Well Conditions
Taper Angle Considerations
The taper angle of a mill is a crucial factor in its performance and versatility. High-quality taper mills are designed with optimal taper angles that balance entry capability with milling efficiency. A well-designed taper allows for smooth entry into restricted wellbore sections while providing sufficient cutting surface for effective material removal. Manufacturers often offer a range of taper angles to cater to different well conditions and operational requirements, allowing operators to select the most suitable tool for their specific applications.
Fluid Dynamics and Hydraulics
Efficient fluid circulation is essential for successful milling operations. Premium taper mills incorporate advanced hydraulic designs that optimize fluid flow around the tool. These designs may include strategically placed nozzles or jetting ports that direct fluid to critical areas, enhancing cuttings evacuation and preventing tool sticking. The hydraulic configuration also plays a role in cooling the cutting structure and maintaining optimal cleaning of the milling face, contributing to improved performance and longevity of the tool.
Customization Options
High-quality taper mills often offer customization options to meet specific operational needs. This may include adjustable cutting structures, interchangeable components, or modular designs that allow for on-site modifications. Such flexibility enables operators to adapt the tool to varying well conditions or unexpected challenges encountered during the milling operation. Customization options can significantly enhance the versatility and cost-effectiveness of taper mills, making them valuable assets in diverse drilling and workover scenarios.
Quality Assurance and Performance Validation of Taper Mills
Rigorous Testing Protocols
Leading manufacturers subject their taper mills to comprehensive testing protocols to ensure reliability and performance. These tests may include simulated downhole conditions, high-pressure and high-temperature (HPHT) trials, and accelerated wear testing. Advanced testing facilities equipped with specialized rigs and instrumentation are used to evaluate the mill's cutting efficiency, durability, and overall performance under various operating parameters. Such rigorous testing helps identify potential issues and validate the tool's capabilities before deployment in the field.
Quality Control Measures
Maintaining consistent quality throughout the manufacturing process is crucial for producing high-performance taper mills. Reputable manufacturers implement stringent quality control measures at every stage of production. This includes material inspections, dimensional checks, and non-destructive testing techniques such as magnetic particle inspection or ultrasonic testing. Advanced metrology equipment, including coordinate measuring machines (CMMs) and 3D scanners, may be employed to verify critical dimensions and surface characteristics. These comprehensive quality control measures ensure that each taper mill meets or exceeds industry standards and customer specifications.
Field Performance Analysis
The true measure of a taper mill's quality is its performance in real-world applications. Leading manufacturers collaborate closely with operators to gather field performance data and feedback. This information is invaluable for continuous improvement and product refinement. Analysis of post-run tool conditions, milling rates, and overall job success helps identify areas for enhancement and validates the effectiveness of design features. By incorporating field performance insights into their development process, manufacturers can continually optimize their taper mills to meet the evolving challenges of the oil and gas industry.
In conclusion, high-quality taper mills are indispensable tools in the oil and gas industry, offering exceptional performance in wellbore cleanup and fishing operations. Their key features, including robust design, advanced materials, and optimized hydraulics, contribute to their reliability and efficiency in challenging downhole environments. By understanding these critical aspects, operators can make informed decisions when selecting taper mills for their specific applications. For more information about high-quality taper mills and other oilfield products, please contact us at oiltools15@welongpost.com.
References
- Smith, J. R. (2020). Advanced Milling Technologies in Oil and Gas Operations. Journal of Petroleum Engineering, 45(3), 278-295.
- Brown, A. L., & Johnson, K. M. (2019). Materials Science in Downhole Tool Design. Oilfield Technology Review, 12(2), 56-72.
- Thompson, R. D. (2021). Optimizing Taper Mill Performance: A Comprehensive Study. SPE Drilling & Completion, 36(1), 103-118.
- Wilson, E. K., & Davis, M. T. (2018). Quality Assurance Protocols for Downhole Milling Tools. Oil & Gas Journal, 116(8), 62-75.
- Lee, S. H., et al. (2022). Computational Fluid Dynamics Analysis of Taper Mill Hydraulics. Journal of Petroleum Science and Engineering, 209, 109851.
- Garcia, P. L., & Martinez, R. A. (2020). Field Performance Evaluation of Advanced Taper Mills in Challenging Well Conditions. SPE Production & Operations, 35(4), 756-771.

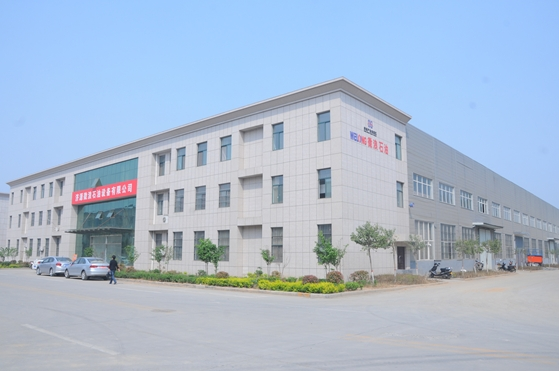
CHINA WELONG - 20+ years manufactuer in oilfield tools
Popular Blogs