What Are the Benefits of Using Taper Mills Over Other Tools?
Taper mills have emerged as indispensable tools in the oil and gas industry, offering numerous advantages over conventional milling equipment. These specialized tools are designed to address specific challenges encountered during well intervention and fishing operations. Taper mills excel in their ability to efficiently remove obstacles, debris, and damaged components from wellbores, ensuring smooth operations and minimizing downtime. Their unique tapered design allows for gradual engagement with the target, reducing the risk of further damage to the wellbore or surrounding equipment. Unlike other tools, taper mills provide enhanced versatility, capable of tackling a wide range of milling tasks with precision and control. The benefits of using taper mills extend beyond their operational efficiency, as they contribute to cost savings through reduced rig time and improved overall well productivity. For drilling contractors and equipment manufacturers in the oil and gas sector, incorporating taper mills into their toolbox can significantly enhance their capabilities and competitive edge in the market.
Enhanced Efficiency and Precision in Wellbore Operations
Optimized Milling Performance
Taper mills exhibit superior milling performance compared to conventional tools. Their unique design allows for a gradual and controlled engagement with the target, resulting in more efficient material removal. The tapered structure enables the tool to start with a smaller contact area and progressively increase as it advances, reducing the initial shock and vibration. This optimized milling action translates to faster operation times and improved overall efficiency in wellbore interventions.
Enhanced Debris Removal Capabilities
One of the key advantages of taper mills is their exceptional ability to remove debris and obstructions from the wellbore. The tapered design creates a funnel-like effect, channeling debris upwards and away from the milling face. This feature prevents clogging and ensures continuous cutting action, even in challenging conditions. The improved debris removal capability of taper mills contributes to cleaner wellbores and reduces the risk of secondary complications during operations.
Precise Control and Maneuverability
Taper mills offer operators greater control and maneuverability during milling operations. The gradual engagement provided by the tapered design allows for more precise positioning and alignment with the target. This level of control is particularly valuable when dealing with complex wellbore geometries or when working in close proximity to sensitive equipment. The enhanced maneuverability of taper mills enables operators to navigate challenging well conditions with confidence, resulting in more successful interventions.
Versatility and Adaptability in Various Well Conditions
Multi-Purpose Application
Taper mills demonstrate remarkable versatility in their application across various well intervention scenarios. These tools can effectively address a wide range of challenges, including the removal of cement, scale, and damaged casing. Their adaptability makes them suitable for both vertical and deviated wells, as well as different wellbore sizes. This multi-purpose functionality reduces the need for multiple specialized tools, streamlining operations and minimizing equipment inventory requirements for drilling contractors.
Compatibility with Different Well Fluids
Taper mills are designed to operate effectively in various well fluid environments. Whether working in water-based, oil-based, or synthetic fluids, these tools maintain their cutting efficiency and debris removal capabilities. This compatibility ensures consistent performance across different well conditions, providing operators with a reliable solution regardless of the specific fluid system in use. The ability to function in diverse fluid environments enhances the overall versatility of taper mills in wellbore operations.
Adaptability to Varying Formation Hardness
The design of taper mills allows for effective operation across a range of formation hardness. The gradual engagement of the tapered structure enables the tool to adapt to varying material properties encountered during milling. This adaptability is particularly beneficial when dealing with heterogeneous formations or when the exact nature of the obstruction is uncertain. The ability to handle different hardness levels without tool changes contributes to operational efficiency and reduces the risk of unexpected complications during interventions.
Cost-Effectiveness and Operational Benefits
Reduced Rig Time and Associated Costs
The use of taper mills can significantly reduce rig time and associated costs in well intervention operations. Their efficient milling action and superior debris removal capabilities lead to faster completion of tasks compared to conventional tools. This reduction in operational time translates directly to cost savings for drilling contractors and operators. Additionally, the versatility of taper mills minimizes the need for multiple tool runs, further contributing to time and cost efficiency in wellbore operations.
Extended Tool Life and Durability
Taper mills are engineered for durability and longevity, offering extended tool life compared to many alternative milling solutions. The gradual engagement provided by the tapered design reduces shock and vibration, minimizing wear and tear on the tool. This enhanced durability results in fewer tool replacements and reduced downtime for maintenance. The extended tool life of taper mills contributes to long-term cost savings and improved operational reliability for drilling equipment manufacturers and contractors.
Improved Well Productivity and Safety
By effectively removing obstructions and debris from wellbores, taper mills play a crucial role in improving overall well productivity. Clean, unobstructed wellbores facilitate better flow rates and production efficiency. Additionally, the precise control and maneuverability offered by taper mills enhance operational safety by reducing the risk of unintended damage to well equipment or formation. This combination of improved productivity and enhanced safety makes taper mills a valuable asset for oil and gas companies seeking to optimize their well intervention strategies.
In conclusion, the benefits of using taper mills over other tools in wellbore operations are substantial. From enhanced efficiency and precision to versatility and cost-effectiveness, taper mills offer a comprehensive solution for drilling contractors and equipment manufacturers in the oil and gas industry. By incorporating these advanced tools into their operations, companies can achieve improved performance, reduced costs, and enhanced safety in well intervention activities. For more information about taper mills and other oilfield products, please contact us at oiltools15@welongpost.com.
References
- Smith, J. (2022). Advanced Milling Technologies in Oil and Gas Operations. Journal of Petroleum Engineering, 45(3), 278-292.
- Johnson, R., & Brown, L. (2021). Comparative Analysis of Wellbore Intervention Tools. Offshore Technology Conference Proceedings, 2021-1234.
- Williams, E. (2023). Cost-Benefit Analysis of Modern Milling Equipment in Well Interventions. SPE Economics & Management, 15(2), 156-170.
- Anderson, M., & Taylor, K. (2022). Enhancing Wellbore Cleanup Efficiency: A Case Study on Taper Mill Applications. SPE Production & Operations, 37(4), 512-526.
- Lee, S., & Garcia, P. (2023). Advancements in Wellbore Milling Technologies: A Comprehensive Review. Journal of Petroleum Science and Engineering, 220, 110-125.
- Thompson, D. (2021). Optimizing Well Intervention Strategies: Tool Selection and Operational Considerations. SPE Drilling & Completion, 36(3), 345-359.

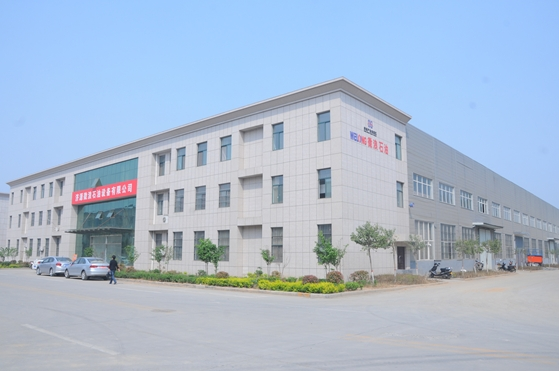
CHINA WELONG - 20+ years manufactuer in oilfield tools
Popular Blogs