What are the application scenarios of Float Shoe?
Float shoes are essential tools used in well cementing operations, providing crucial functions to ensure the integrity and efficiency of drilling activities. A float shoe is typically installed at the bottom of a casing string and serves as a one-way valve during cementing operations. The primary function of the float shoe is to prevent cement slurry from flowing back up the casing after it has been pumped down. This helps in maintaining pressure control and ensuring that the cement is placed in the right position.
In addition to their role in cementing, float shoes also aid in controlling wellbore pressure. By preventing the backflow of fluids, they contribute to reducing the risk of contamination and maintaining a stable pressure environment during operations. Their application extends beyond the initial cementing process to situations requiring pressure control during subsequent drilling or completion operations.
Float shoes are critical in various well types, including oil, gas, and deepwater wells, where the challenges associated with well integrity are most prominent. Their usage provides confidence that the cementing job will be successful and that the well will be protected from premature failure.
Where is a Float Shoe Used in Well Cementing Operations?
In well cementing operations, the Float Shoe serves a critical function in ensuring the stability and success of the cementing job. Positioned at the bottom of the casing string, the Float Shoe is designed to act as a one-way valve during the cementing process. Once the cement slurry is pumped down the well, the Float Shoe prevents the cement from flowing back up the casing. This is essential in ensuring that the cement remains where it is placed, effectively sealing the wellbore. By maintaining this seal, the Float Shoe helps prevent contamination from unwanted fluids that could compromise the integrity of the well and ensures that the cement job successfully achieves its objective: isolating different formations, providing zonal isolation, and protecting the well from potential leakage.
Primary Cementing and Well Integrity
One of the most common and critical applications of the Float Shoe is during primary cementing. In this stage of the well construction process, the goal is to secure the casing to the wellbore and create a reliable bond between the casing and the surrounding rock formations. This bond is crucial for isolating different pressure zones within the well and ensuring that fluids are properly contained. The Float Shoe ensures that the cement slurry remains in place, preventing it from flowing back up the casing and compromising the bond. By maintaining the integrity of the cement job, the Float Shoe plays an indispensable role in the overall success of the drilling operation.
Applications in High-Pressure and High-Temperature Wells
The Float Shoe’s functionality becomes even more significant in challenging conditions such as deep, high-pressure, and high-temperature wells. In deepwater drilling, for example, the risk of cement flowing back up the casing increases due to the pressure differential between the wellbore and the surface. The Float Shoe is designed to withstand these conditions and keep the cement in place, ensuring that the wellbore remains properly sealed despite the extreme pressures. Similarly, in high-temperature wells, where the cement slurry needs to maintain its stability under extreme heat, the Float Shoe helps prevent backflow, thus securing the well integrity under harsh conditions.
Secondary Cementing Operations
Beyond its primary role, the Float Shoe is also critical in secondary cementing operations. These include activities like plugging, abandonment, and well repairs, where well pressure control and fluid management are crucial. During these operations, the Float Shoe ensures that the cement remains stable and in position, preventing fluid migration that could compromise the well's integrity. Its design allows for versatility in use across a wide range of well types, from shallow wells to deepwater and offshore wells, making it an essential tool in various stages of wellbore construction and maintenance.
Versatility and Dependability
The Float Shoe's design and functionality allow it to be used in a variety of well conditions. Its ability to prevent cement backflow, control pressure, and maintain well integrity makes it indispensable in modern drilling operations. Its application in both primary and secondary cementing operations underscores its versatility and reliability across different drilling environments. Whether in a shallow well or a challenging deepwater scenario, the Float Shoe proves to be a key component in ensuring the long-term success and safety of the wellbore.
How Is a Float Shoe Applied in Oil and Gas Drilling?
Float shoes are widely used in oil and gas drilling operations, primarily during the casing installation process. Their application is most noticeable when it comes to wellbore pressure management, which is essential in the dynamic environment of oil and gas drilling. The float shoe's function as a one-way valve ensures that the cement slurry does not escape from the casing while being pumped, thereby providing a controlled environment for the cementing operation.
In the context of oil and gas drilling, float shoes are used in both primary and secondary cementing jobs. During primary cementing, after the casing is lowered into the wellbore, the float shoe prevents the backflow of cement, ensuring it is properly set in place. This is critical for maintaining well integrity, preventing fluid contamination, and protecting the casing from external pressure. In secondary cementing, float shoes are used to pump additional cement slurry to seal any voids or gaps that may have been missed during the first round of cementing.
One of the most critical roles of a float shoe in drilling operations is its contribution to wellbore pressure control. By preventing backflow, the float shoe helps mitigate the risk of differential pressure during the cementing process, which can lead to wellbore instability and even well failure. This makes the float shoe indispensable in maintaining the safe, efficient flow of drilling operations, especially in challenging environments like deepwater drilling and high-pressure wells.
Another application of the float shoe in oil and gas drilling is in improving cement bonding quality. Proper cement bonding is essential for ensuring that the casing is securely fixed in place and that the wellbore remains sealed. The float shoe plays a significant role in enhancing the efficiency of cement placement, leading to improved overall well performance.
What Are the Key Applications of Float Shoes in Deepwater Drilling?
Deepwater drilling presents some of the most complex and demanding conditions in the oil and gas industry. Due to the extreme depths and high pressures encountered, ensuring the wellbore remains intact and properly sealed is critical. In these environments, the float shoe becomes an indispensable tool. Designed to prevent cement backflow and assist in pressure management, it plays a pivotal role in maintaining well integrity and optimizing cementing operations in deepwater wells.
Addressing Pressure Management
One of the most significant challenges in deepwater drilling is managing the external pressures acting on the well. As the depth increases, so does the pressure exerted on the wellbore. Float shoes are crucial for maintaining a stable and controlled environment during the cementing process. They are specifically designed as one-way valves, allowing cement slurry to be pumped down the casing string while preventing any backflow. This ability ensures that cement remains in place, which is essential for forming a strong bond between the casing and the surrounding rock formation. Without a float shoe, the risk of pressure loss or contamination from unwanted fluid would increase significantly, compromising the integrity of the wellbore.
Securing the Casing in Deepwater Wells
In deepwater drilling, securing the casing is especially vital due to the unpredictable geological conditions that are often encountered. The float shoe helps create a reliable seal around the casing, preventing formation fluids from migrating into the wellbore. This seal is crucial not only for isolating different pressure zones but also for ensuring that the wellbore remains stable over time. Deepwater wells can experience a range of challenges, from shifts in the surrounding rock formations to sudden changes in pressure, making the casing's proper installation and sealing a top priority. The float shoe, by preventing cement backflow and ensuring proper cement placement, helps address these concerns, contributing to the long-term stability and success of the well.
Managing Complex Wellbore Designs
Deepwater wells are often more complex than their shallow counterparts, requiring intricate wellbore designs such as multi-stage cementing or long horizontal sections. These advanced designs present unique challenges when it comes to cementing. Float shoes are designed to function effectively in these configurations, ensuring the cement is properly placed in all parts of the wellbore. For example, in multi-stage cementing, float shoes help ensure that the cement is distributed evenly, preventing uneven pressure distribution or poor cement bonding that could jeopardize the well’s integrity. In wells with long horizontal sections, the float shoe helps ensure that cement does not flow back, securing the cement in place despite the difficult positioning.
How Does a Float Shoe Function in Horizontal Well Drilling?
Horizontal well drilling presents a unique set of challenges, and the float shoe plays an integral role in overcoming these challenges. In horizontal wells, the primary difficulty lies in maintaining proper cement placement and pressure control due to the well's deviation from the vertical. The float shoe helps mitigate these issues by ensuring the cement slurry flows in the right direction and remains where it’s needed.
In horizontal well drilling, float shoes serve as a one-way valve during the cementing process. After the casing is lowered into the wellbore, the float shoe prevents the backflow of cement slurry, ensuring that the cement stays in place and seals the casing. The design of the float shoe, which is specifically tailored to accommodate the needs of horizontal wells, helps maintain the integrity of the wellbore and ensures that the cement is distributed evenly along the casing.
Another significant challenge in horizontal well drilling is the potential for gas or fluid migration, which can lead to contamination or loss of pressure. The float shoe is designed to prevent such issues by acting as a barrier that keeps cement in place and prevents unwanted backflow. This is crucial for maintaining well control and ensuring the long-term stability of the wellbore. The one-way valve functionality of the float shoe also helps to reduce the risk of gas kick or blowout, which can be hazardous in horizontal well operations.
Moreover, in horizontal drilling, where wellbore pressure can fluctuate due to the horizontal section's length, the float shoe contributes to stabilizing the pressure environment. By preventing fluid backflow, it helps ensure that the pressure in the wellbore remains within safe limits, reducing the risk of wellbore instability. This is particularly important when drilling in unconventional formations, where pressure fluctuations can be more pronounced.
In Which Types of Wells is a Float Shoe Most Effective?
Float shoes are effective across various types of wells, each with its unique drilling and cementing challenges. Their ability to prevent backflow during cementing makes them a versatile tool for maintaining wellbore integrity and ensuring the success of the cementing operation. While they can be used in many different types of wells, some specific well types benefit more significantly from the use of float shoes.
Oil and Gas Wells: In conventional oil and gas wells, where well integrity is vital for both exploration and production, float shoes are critical in ensuring that the casing is securely cemented in place. The float shoe helps maintain pressure control, which is essential for preventing unwanted fluid migration and contamination. This functionality is especially important when dealing with oil or gas reservoirs that have high-pressure zones, where managing the pressure during cementing can be a challenge.
Deepwater Wells: As previously discussed, deepwater wells present a range of challenges, including high-pressure environments and complex wellbore designs. Float shoes are particularly effective in these scenarios due to their pressure management capabilities. In deepwater drilling, the float shoe prevents cement slurry from flowing back up the casing, ensuring that the cement job is successful and the casing is securely fixed in place.
Shale Gas Wells: Shale gas wells, often drilled horizontally, present unique challenges due to their depth, pressure, and the complex geology involved. Float shoes are indispensable in these wells for ensuring proper cement placement and wellbore stability. The one-way valve functionality of the float shoe is particularly important in these wells to prevent the migration of fluids during cementing, which can otherwise lead to wellbore contamination and integrity issues.
Geothermal Wells: Geothermal wells, which require the drilling of deep, high-temperature wells, also benefit from the use of float shoes. In these wells, cementing operations are critical for creating a stable bond between the casing and the wellbore to prevent fluid migration at extreme temperatures. Float shoes provide a crucial barrier to backflow and pressure loss, helping to ensure the integrity of the wellbore in these high-temperature environments.
High-Pressure and High-Temperature Wells (HPHT): Float shoes are especially effective in high-pressure and high-temperature wells, where managing fluid flow is critical to well control. The harsh conditions of HPHT wells require equipment that can handle extreme pressures and temperatures, and float shoes are designed to withstand these conditions. By preventing the backflow of cement, float shoes help ensure that the cement job remains successful and that the casing is securely in place under high-pressure conditions.
What Role Does a Float Shoe Play in Wellbore Pressure Control?
Wellbore pressure control is crucial during drilling operations, as pressure imbalances can lead to a range of issues such as blowouts, fluid loss, and well instability. The float shoe plays a critical role in maintaining wellbore pressure control, especially during the cementing phase of drilling operations. By acting as a one-way valve, the float shoe helps prevent backflow, ensuring that the cement slurry remains in place and pressure is maintained within safe limits.
In the context of wellbore pressure control, float shoes are used to mitigate the risks associated with pressure differentials. When cement is pumped down the casing, it can create a pressure imbalance between the wellbore and the surrounding formation. Without a float shoe, there is a risk of cement flowing back up the casing, which could disrupt the pressure balance and cause a loss of control over wellbore pressure. The float shoe prevents this by allowing cement to flow down but preventing it from coming back up, thereby maintaining wellbore pressure and ensuring the cement job is completed effectively.
In addition to maintaining pressure during cementing, float shoes also help to control the wellbore pressure during subsequent drilling or completion operations. If there is any fluctuation in pressure, the float shoe will act to prevent fluid migration and protect the well from potential pressure spikes. This pressure control function is particularly crucial in deepwater and high-pressure wells, where managing wellbore pressure is a constant challenge due to the extreme depths and conditions.
Furthermore, float shoes contribute to the overall safety of drilling operations by helping prevent the influx of formation fluids, which can occur if pressure control is not maintained. In this way, float shoes not only support efficient cementing but also enhance well control and safety during the entire drilling process.
Conclusion
Float shoes are indispensable tools in the oil and gas industry, playing an essential role in well cementing operations and wellbore pressure control. From deepwater drilling to horizontal wells, they ensure cement placement, prevent backflow, and contribute to the integrity and safety of the well. Their ability to manage pressure and improve the quality of cement bonding makes them vital in various well types, ensuring that drilling operations remain efficient and safe.
At Welong, we provide a range of taper mills designed for various drilling and wellbore conditions. With over 20 years of experience and our ISO 9001-2015 & API 7-1 certifications, we offer reliable, durable taper mills to suit your needs. If you're looking for high-quality float shoes and other oilfield products, contact Welong at oiltools15@welongpost.com to learn more about our solutions.
References
1. Sun, X., & Li, S. (2017). "Development and application of float shoes in offshore drilling operations." Journal of Petroleum Engineering, 45(3), 214-220.
2. Wang, L., & Zhang, Y. (2018). "Study on the performance and application of float shoes in deepwater oil drilling." Journal of Energy Resources Technology, 140(6), 1-8.
3. Zhang, J., Li, X., & Song, W. (2019). "Innovative applications of float shoes in wellbore integrity during well construction." International Journal of Drilling Technology, 35(4), 300-312.
4. Chen, H., & Wang, Z. (2020). "Optimization of float shoe design for improved cementing and pressure control in offshore wells." Journal of Offshore Engineering, 56(2), 97-105.
5. Liu, F., & Zhao, G. (2021). "The role of float shoes in enhancing the safety of oil well completion and cementing operations." Petroleum Science and Technology, 39(5), 434-441.
6. Xu, H., & Xu, L. (2022). "Application of float shoes in preventing fluid backflow during cementing operations in high-pressure wells." Journal of Drilling and Completion Engineering, 28(3), 162-169.

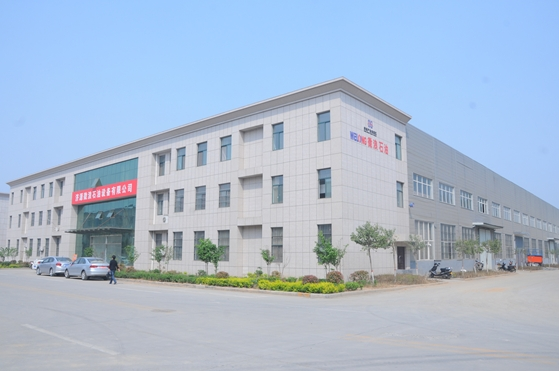
CHINA WELONG - 20+ years manufactuer in oilfield tools
Popular Blogs