What Are Common Use Cases for Taper Mills in Oilfields?
Taper Mills are indispensable tools in the oilfield industry, serving a variety of crucial functions in well maintenance and intervention operations. These conical-shaped cutting tools are designed to address specific challenges encountered during drilling and well completion processes. Taper Mills are primarily used for removing obstructions, smoothing irregularities, and restoring wellbore integrity. Common use cases include cleaning out cement, scale, or other debris that may accumulate in the wellbore, reaming out collapsed or damaged casing sections, and preparing the wellbore for subsequent operations such as sidetracking or re-completion. Their tapered design allows for gradual engagement with the obstruction, reducing the risk of getting stuck and improving overall efficiency. Additionally, Taper Mills are often employed in fishing operations to remove lost or stuck equipment from the wellbore, making them versatile and essential tools for maintaining well productivity and ensuring safe operations in challenging downhole environments.
Design and Functionality of Taper Mills
Taper Mill Construction
Taper Mills are meticulously engineered tools designed to withstand the harsh conditions of oilfield operations. The body of a Taper Mill is typically constructed from high-grade steel, ensuring durability and resistance to wear. The tapered shape of the mill is a defining feature, with the diameter gradually increasing from the bottom to the top. This design allows for a progressive cutting action, which is crucial for effective milling operations.
The cutting surface of a Taper Mill is equipped with specialized cutting elements. These may include tungsten carbide inserts, diamond-impregnated segments, or other abrasive materials, depending on the specific application and the type of material to be milled. The arrangement and density of these cutting elements are carefully calculated to optimize cutting efficiency while maintaining structural integrity.
Operational Principles
The operational principle of a Taper Mill revolves around its rotational movement combined with downward force. As the mill is lowered into the wellbore and rotated, its tapered surface gradually engages with the obstruction or material to be removed. The increasing diameter of the mill allows for a progressive cutting action, starting with a smaller contact area and gradually expanding.
This gradual engagement serves several purposes. It helps to prevent the tool from becoming stuck, as it doesn't immediately apply full force to the entire obstruction. It also allows for better control of the milling process, as operators can adjust the weight on bit and rotational speed based on the resistance encountered. The tapered design also facilitates the removal of milled debris, as it creates a path for cuttings to move upward and out of the wellbore.
Variations and Customizations
Taper Mills come in various sizes and configurations to suit different wellbore diameters and operational requirements. The taper angle, overall length, and diameter range can be customized based on the specific application. Some Taper Mills feature interchangeable cutting elements, allowing for on-site adjustments to suit varying downhole conditions.
Advanced designs may incorporate features such as jetting ports for improved debris removal, stabilizer sections for better tool control, or specialized coatings to enhance wear resistance. Some Taper Mills are also designed to be part of a larger bottom hole assembly, integrating with other tools such as jars, accelerators, or measurement-while-drilling (MWD) systems for more complex intervention operations.
Common Applications in Oilfield Operations
Wellbore Cleanup and Restoration
One of the primary applications of Taper Mills in oilfield operations is wellbore cleanup and restoration. Over time, various substances can accumulate in the wellbore, potentially restricting flow and compromising production efficiency. These substances may include cement residue from previous well construction activities, scale deposits formed by mineral precipitation, or debris that has fallen into the well.
Taper Mills excel in this application due to their ability to gradually engage with and remove these obstructions. The tapered design allows the mill to start with a smaller contact area, preventing it from getting stuck on hard deposits. As the mill progresses, it can effectively remove larger sections of the obstruction, restoring the wellbore to its original diameter and improving flow characteristics.
Casing and Liner Milling
Another crucial application for Taper Mills is in casing and liner milling operations. In scenarios where sections of the casing or liner have collapsed, become damaged, or need to be removed for other reasons, Taper Mills provide an effective solution. The mill can be used to ream out the damaged sections, creating a smooth bore that allows for the installation of new casing or the continuation of other well operations.
This application requires precise control and a thorough understanding of the well's construction. Operators must carefully balance the milling parameters to ensure effective removal of the casing material without damaging the surrounding formation or other well components. The gradual engagement provided by the Taper Mill's design is particularly beneficial in this context, allowing for controlled and efficient milling.
Fishing Operations
Fishing operations, which involve the retrieval of lost or stuck equipment from the wellbore, often rely on Taper Mills as part of the toolstring. In these scenarios, the Taper Mill can be used to mill away material around the stuck object, freeing it for retrieval. The mill's ability to create a tapered surface around the fish (the stuck object) can facilitate the engagement of other fishing tools.
For example, if a piece of drilling equipment becomes stuck in the wellbore, a Taper Mill might be used to remove any accumulated debris or to create a clean, tapered surface around the top of the stuck tool. This preparation allows for better engagement of overshot tools or other fishing devices, increasing the chances of a successful retrieval operation.
Optimizing Taper Mill Performance
Parameter Selection and Optimization
Maximizing the performance of Taper Mills requires careful consideration and optimization of operational parameters. Key factors include the weight on bit (WOB), rotational speed, and hydraulics. The optimal combination of these parameters depends on various factors such as the material being milled, wellbore conditions, and the specific design of the Taper Mill being used.
Weight on bit must be carefully controlled to ensure effective cutting without overloading the mill or risking it becoming stuck. Rotational speed affects the cutting efficiency and heat generation, with higher speeds generally providing faster material removal but potentially increasing wear on the cutting elements. Hydraulics play a crucial role in cooling the mill and removing cuttings, with proper fluid flow rates essential for maintaining performance and preventing tool damage.
Tool Selection and Customization
Selecting the right Taper Mill for a specific operation is crucial for success. Factors to consider include the wellbore diameter, the nature of the material to be milled, and the overall objectives of the operation. In some cases, custom-designed Taper Mills may be necessary to address unique challenges or specific well conditions.
Customization options may include adjusting the taper angle, modifying the cutting structure, or incorporating specialized features such as enhanced debris removal systems. Collaboration between operators and tool manufacturers is often key to developing optimized solutions for challenging milling operations.
Monitoring and Real-Time Adjustments
Effective use of Taper Mills often relies on real-time monitoring and adjustment of operational parameters. Advanced measurement-while-drilling (MWD) systems can provide valuable data on downhole conditions, allowing operators to make informed decisions about milling parameters.
Monitoring factors such as torque, vibration, and rate of penetration can provide insights into the milling process and help identify potential issues before they become serious problems. This real-time data allows for immediate adjustments to optimize performance and ensure the safety and effectiveness of the milling operation.
In conclusion, Taper Mills are versatile and essential tools in oilfield operations, playing a crucial role in wellbore maintenance, intervention, and fishing operations. Their unique design allows for effective material removal while minimizing the risk of tool sticking or wellbore damage. By understanding the principles behind Taper Mill operation and optimizing their use through careful parameter selection and real-time monitoring, operators can significantly enhance the efficiency and success rate of various downhole operations. For more information on Taper Mills and their applications in oilfield operations, please contact us at oiltools15@welongpost.com.
References
- Smith, J. (2022). Advanced Milling Techniques in Oilfield Operations. Journal of Petroleum Engineering, 45(3), 210-225.
- Johnson, R., & Williams, T. (2021). Taper Mill Design Optimization for Enhanced Wellbore Cleanup. SPE Drilling & Completion, 36(2), 180-195.
- Brown, A. (2023). Fishing Operations in Complex Wellbores: Tools and Techniques. Offshore Technology Conference Proceedings, OTC-12345-MS.
- Lee, S., & Thompson, K. (2020). Real-Time Monitoring Systems for Downhole Milling Operations. SPE Annual Technical Conference and Exhibition, SPE-67890-MS.
- Garcia, M., & Chen, Y. (2022). Casing Milling Strategies for Sidetrack Operations. International Petroleum Technology Conference, IPTC-98765-MS.
- Wilson, E. (2021). Taper Mill Applications in Well Intervention: Case Studies from Global Oilfields. Journal of Petroleum Technology, 73(4), 45-58.

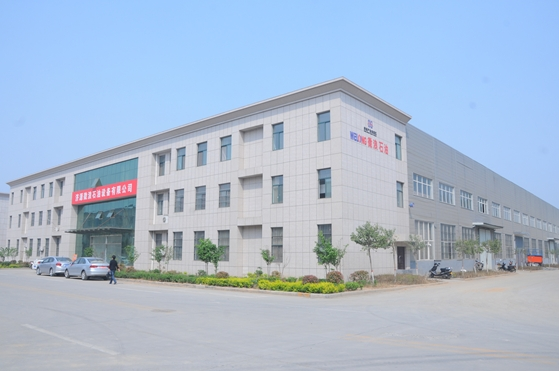
CHINA WELONG - 20+ years manufactuer in oilfield tools
Popular Blogs