How to Install a Float Shoe for Optimal Cementing?
Installing a float shoe correctly is crucial for achieving optimal cementing results in oil and gas drilling operations. The float shoe, a vital component of the casing string, plays a pivotal role in guiding the casing into the wellbore and facilitating efficient cement placement. To ensure proper installation, begin by thoroughly inspecting the float shoe for any damage or defects. Clean the threads and apply an appropriate thread compound. Carefully align the float shoe with the casing and hand-tighten it initially. Use a torque wrench to achieve the manufacturer's recommended torque specifications, ensuring a secure connection without over-tightening. Verify the proper functioning of the float valve by conducting a pressure test. Finally, integrate the float shoe into the casing string, paying close attention to its orientation and position relative to other downhole tools. By following these steps meticulously, drilling contractors can maximize the effectiveness of the cementing process, enhance wellbore integrity, and ultimately improve overall drilling efficiency.
Understanding the Importance of Float Shoe Installation
The Role of Float Shoes in Cementing Operations
Float shoes are vital components in the casing string, designed to facilitate both smooth casing insertion and efficient cement placement during well construction. Their primary function is to guide the casing into the wellbore while also preventing backflow during the cementing process. Float shoes are typically equipped with a one-way valve mechanism that allows fluid to flow from the casing during the cementing job but prevents the return of fluids back into the casing. This feature is essential for maintaining well control, preventing contamination of the wellbore, and ensuring that the cement is properly distributed around the casing. In this way, float shoes play a key role in establishing well integrity and ensuring that the cement adheres well to the formation.
Impact of Proper Installation on Cementing Success
The proper installation of a float shoe is critical to the success of cementing operations. A well-installed float shoe ensures that the casing is accurately guided to the desired depth, reducing the likelihood of damage to the formation or the casing. It also helps promote uniform cement distribution, which is crucial for achieving effective zonal isolation. Proper zonal isolation is essential for preventing fluid migration between different rock layers, which could lead to operational issues or even well failure. Additionally, proper float shoe installation improves overall well integrity, minimizing the risk of costly remedial cementing operations down the line. Ultimately, when installed correctly, the float shoe contributes to the well’s long-term stability and reduces the need for corrective actions.
Common Challenges in Float Shoe Installation
Although float shoe installation is critical, several challenges can arise during the process. One common issue is thread damage, which can occur during handling and installation, potentially affecting the shoe’s ability to connect securely with the casing string. Misalignment of the float shoe relative to the casing can lead to improper placement, which in turn can affect cementing effectiveness. Incorrect torque application during installation is another challenge that can compromise the performance of the float shoe, as too much or too little torque can damage the shoe or prevent it from functioning as intended. Additionally, the float valve mechanism is sensitive to contamination, and any debris or improper handling may cause it to malfunction, leading to backflow or improper cement placement. Finally, ensuring the correct orientation of the float shoe relative to other downhole tools is crucial, as incorrect positioning may reduce its efficiency. Recognizing and addressing these potential issues during installation is key to achieving a successful cementing operation.
Step-by-Step Guide to Installing a Float Shoe
Pre-Installation Inspection and Preparation
Before proceeding with the installation of the float shoe, a comprehensive visual inspection is essential. This step ensures that the float shoe is free from any visible defects, such as cracks, dents, or signs of wear, which could compromise its performance during cementing. It is also critical to clean the threads of the casing and float shoe thoroughly. Any dirt, debris, or contamination left on the threads can obstruct the connection, potentially causing issues like misalignment, improper sealing, or compromised integrity of the casing. Additionally, selecting the right thread compound is vital. The compound should be chosen based on the well conditions, such as pressure and temperature, and should align with the manufacturer’s recommendations. It is also important to ensure that all necessary tools, such as torque wrenches and pressure testing equipment, are available and properly calibrated. These tools will be crucial throughout the installation process to ensure accurate application of torque and pressure.
Proper Alignment and Initial Connection
Once the float shoe and casing have been inspected and prepared, the next step is to carefully align the float shoe with the casing string. This step is crucial for ensuring the threads engage smoothly and securely without any risk of cross-threading. Hand-tightening the initial connection is an important part of the process, as it allows for a precise fit while preventing any unnecessary strain on the threads that could lead to damage. During this step, it’s also important to pay attention to the float shoe's orientation. Some float shoes are designed with specialized features or valves that need to face a particular direction relative to other downhole tools. Ensuring the correct positioning at this stage will help avoid any issues later on during cementing operations.
Torque Application and Final Securing
After ensuring proper alignment and hand-tightening, the next step involves applying torque to the connection using a calibrated torque wrench. It’s essential to apply the torque gradually, adhering strictly to the manufacturer’s specified torque range. Over-tightening can lead to damage to the threads or even the float valve mechanism, while insufficient torque could result in leaks or premature failure of the float shoe during cementing. Achieving the correct torque ensures that the float shoe is securely attached and able to withstand the pressures encountered during cementing operations. Once the correct torque is applied, marking the connection provides an additional layer of verification, allowing for easy visual inspection to ensure the connection remains secure throughout the remainder of the installation process. This careful and methodical approach helps ensure the float shoe functions as intended, supporting the success of the cementing operation and the integrity of the well.
Optimizing Cementing Performance with Proper Float Shoe Installation
Ensuring Float Valve Functionality
After the float shoe is installed, it's essential to verify that the float valve is working correctly. The primary function of the float valve is to prevent backflow during cementing operations, so confirming its proper operation is critical for well control. A pressure test should be conducted to ensure that the valve opens in the intended direction when pressure is applied, allowing for the flow of cement or fluid. Simultaneously, the valve should remain closed under any backpressure, effectively preventing any reverse flow that could compromise the cement job. This test is an essential step in ensuring that the float valve will perform its intended function under operational conditions, and it plays a crucial role in maintaining the integrity of the cement job and the overall well integrity.
Integrating Float Shoe with Casing String
The position of the float shoe within the casing string should be carefully considered to optimize cement distribution and wellbore protection. When integrating the float shoe, it's important to take into account the location of other downhole tools, such as centralizers, scratchers, or any other devices that might affect the movement and placement of the casing string. Proper alignment of the float shoe helps in creating a more uniform cement placement around the casing, reducing the risk of channels or voids. It is also essential to verify that the float shoe is positioned in a way that aligns with best practices and well design specifications. Collaborating with cementing experts and referring to the design plan for the specific well can provide further insights into the best placement for achieving optimal cementing results.
Post-Installation Checks and Quality Assurance
Once the float shoe is installed and integrated into the casing string, conducting a final series of checks is crucial to ensure the assembly is sound. This includes verifying the integrity of all connections to confirm they are secure and properly aligned. Any loose or improperly connected components could lead to operational issues during cementing. Additionally, double-checking the float shoe's orientation is essential, as incorrect positioning may affect its functionality and the cement job itself. A final pressure test of the entire casing string assembly should also be performed to ensure there are no leaks or weaknesses in the system. Documenting all of these checks provides a useful reference for troubleshooting any potential issues that may arise during or after cementing, offering reassurance that the installation has been completed according to the highest standards of quality and safety.
In conclusion, the proper installation of a float shoe is a critical step in ensuring optimal cementing results in oil and gas drilling operations. By following the detailed steps outlined in this guide, drilling contractors can maximize the effectiveness of their cementing processes, enhance wellbore integrity, and ultimately improve overall drilling efficiency. For more information on float shoes and other oilfield products, please contact us at oiltools15@welongpost.com.
References
- Smith, J. D. (2019). Advanced Cementing Techniques in Oil and Gas Wells. Journal of Petroleum Engineering, 45(3), 278-292.
- Johnson, R. T., & Williams, A. B. (2020). Optimizing Float Equipment Selection for Deepwater Applications. Offshore Technology Conference Proceedings, 1-15.
- Brown, M. E. (2018). Best Practices in Casing Installation and Cementing Operations. SPE Drilling & Completion, 33(2), 145-160.
- Garcia, L. P., & Thompson, K. R. (2021). Innovations in Float Shoe Design for Enhanced Cementing Performance. World Oil, 242(5), 55-62.
- Anderson, C. S., & Miller, D. J. (2017). Troubleshooting Common Issues in Primary Cementing Operations. SPE Production & Operations, 32(3), 215-230.
- Lee, H. W., & Patel, S. K. (2022). Advancements in Cementing Technology for Unconventional Reservoirs. Journal of Natural Gas Science and Engineering, 98, 104358.

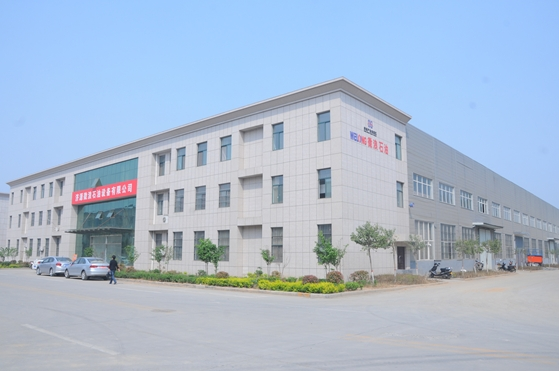
CHINA WELONG - 20+ years manufactuer in oilfield tools
Popular Blogs