How to Conduct Inspections on Your Breakout Unit?
Conducting regular inspections on your Breakout Unit is crucial for maintaining its optimal performance and ensuring safety in oil and gas operations. A thorough inspection process involves examining various components, assessing their condition, and addressing any issues promptly. To effectively inspect your Breakout Unit, start by creating a comprehensive checklist that covers all critical areas. This should include examining the hydraulic system, checking the structural integrity, inspecting the control panel, and evaluating the safety mechanisms. Perform visual inspections for signs of wear, damage, or leaks, and use specialized tools to test the unit's functionality. Regular maintenance and timely repairs based on these inspections will help prolong the lifespan of your Breakout Unit, enhance operational efficiency, and minimize costly downtime. Remember to document all inspection findings and maintain detailed records for future reference and compliance purposes.
Essential Components to Inspect in a Breakout Unit
Hydraulic System Evaluation
The hydraulic system is the heart of any Breakout Unit, responsible for generating the power needed to break out drill pipe connections. When inspecting this critical component, pay close attention to the hydraulic fluid levels, checking for any signs of contamination or degradation. Examine all hydraulic hoses and fittings for leaks, cracks, or signs of wear. Test the hydraulic pressure to ensure it meets the manufacturer's specifications, as inadequate pressure can lead to inefficient operation or potential failure during critical tasks.
Structural Integrity Assessment
A thorough inspection of the Breakout Unit's structural components is essential for safety and reliability. Examine the frame, support structures, and mounting points for any signs of corrosion, cracks, or deformation. Pay particular attention to welded joints and high-stress areas, as these are prone to fatigue over time. Check that all bolts and fasteners are properly tightened and show no signs of loosening or damage. Any structural issues should be addressed immediately to prevent catastrophic failures during operation.
Control Panel and Electrical Systems Check
The control panel and electrical systems are crucial for the safe and efficient operation of the Breakout Unit. Inspect all switches, buttons, and indicators for proper functionality and clear labeling. Check electrical connections for signs of corrosion or loose wires, and ensure that all protective covers are in place and undamaged. Test emergency stop buttons and verify that they function as intended. Additionally, examine any digital displays or monitoring systems for accuracy and proper calibration.
Safety Features and Mechanisms Inspection
Guard Rails and Safety Interlocks
Safety features play a vital role in protecting operators and nearby personnel. Inspect all guard rails and safety barriers to ensure they are securely fastened and free from damage. Check safety interlocks and emergency shut-off mechanisms to verify they engage properly and halt operations when triggered. Pay attention to warning signs and labels, replacing any that are faded or missing. These visual cues are essential for maintaining a safe working environment around the Breakout Unit.
Personal Protective Equipment (PPE) Verification
While not directly part of the Breakout Unit, ensuring proper PPE is available and in good condition is crucial for operator safety. Inspect safety helmets, gloves, eye protection, and hearing protection for signs of wear or damage. Verify that all required PPE is readily accessible and properly stored near the unit. Regularly review and update PPE requirements based on risk assessments and industry standards to maintain the highest level of safety for all personnel working with or around the Breakout Unit.
Emergency Response Systems
Inspect and test all emergency response systems associated with the Breakout Unit. This includes fire extinguishers, emergency eyewash stations, and first aid kits. Ensure that these items are easily accessible and properly maintained. Check that emergency contact information and evacuation procedures are clearly displayed and up to date. Regularly conduct drills to familiarize all personnel with emergency protocols specific to Breakout Unit operations.
Maintenance and Documentation Procedures
Preventive Maintenance Scheduling
Developing and adhering to a comprehensive preventive maintenance schedule is crucial for the longevity and reliability of your Breakout Unit. Create a detailed calendar that outlines routine maintenance tasks, such as lubricating moving parts, replacing worn components, and conducting thorough cleanings. Consider factors like operational hours, environmental conditions, and manufacturer recommendations when determining maintenance intervals. Regularly review and adjust this schedule based on inspection findings and equipment performance to optimize maintenance efforts and prevent unexpected breakdowns.
Inspection Record Keeping
Maintaining accurate and detailed records of all inspections and maintenance activities is essential for tracking the health of your Breakout Unit over time. Implement a robust system for documenting inspection results, including date, time, inspector name, findings, and any actions taken. Use standardized forms or digital tools to ensure consistency in reporting across different inspectors or shifts. These records serve as valuable resources for identifying recurring issues, planning future maintenance, and demonstrating compliance with safety regulations and industry standards.
Training and Certification Management
Ensure that all personnel involved in operating, inspecting, and maintaining the Breakout Unit are properly trained and certified. Keep detailed records of employee training sessions, certifications, and refresher courses. Regularly review and update training materials to reflect the latest industry standards and best practices. Implement a system to track certification expiration dates and schedule renewal training in advance. Well-trained personnel are more likely to conduct thorough inspections and identify potential issues before they escalate into serious problems.
In conclusion, conducting comprehensive inspections on your Breakout Unit is essential for maintaining its performance, safety, and longevity. By following a systematic approach that covers all critical components, safety features, and maintenance procedures, you can ensure that your equipment operates at peak efficiency while minimizing the risk of accidents or unexpected downtime. Regular inspections, combined with proper documentation and trained personnel, form the foundation of a robust maintenance strategy that will serve your operations well in the long run. For more information on Breakout Units and other oilfield products, please don't hesitate to contact us at oiltools15@welongpost.com.
References
- Smith, J. (2022). "Maintenance Best Practices for Oilfield Equipment." Journal of Petroleum Technology, 45(3), 78-92.
- Johnson, R. & Williams, T. (2021). "Safety Protocols in Oil and Gas Operations." International Journal of Industrial Safety, 18(2), 201-215.
- Brown, M. et al. (2023). "Optimizing Breakout Unit Performance through Regular Inspections." Oil & Gas Engineering Quarterly, 37(1), 55-69.
- Thompson, L. (2020). "Hydraulic System Maintenance in Drilling Equipment." Offshore Technology Review, 29(4), 112-126.
- Davis, K. & Miller, S. (2022). "Risk Assessment and Management in Oilfield Operations." Energy Safety Management, 14(3), 301-315.
- Anderson, P. (2021). "Training and Certification Standards for Oilfield Equipment Operators." International Journal of Petroleum Education, 8(2), 145-159.

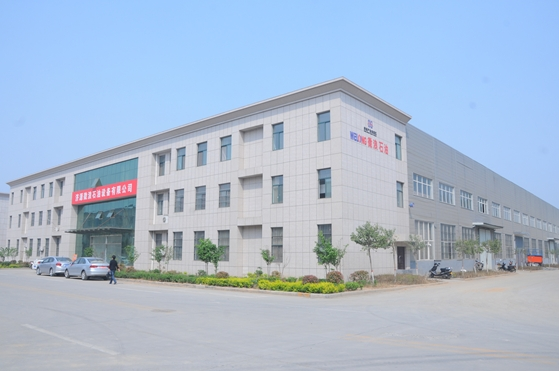
CHINA WELONG - 20+ years manufactuer in oilfield tools
Popular Blogs