How Can Taper Mills Improve Wellbore Cleanup Processes?
Taper mills play a crucial role in enhancing wellbore cleanup processes, offering a range of benefits that contribute to more efficient and effective operations in the oil and gas industry. These specialized tools are designed to address common challenges encountered during wellbore maintenance and remediation. Taper mills are particularly adept at removing debris, scale, and other obstructions that can impede the flow of hydrocarbons and compromise well productivity. By employing a tapered design, these mills can gradually increase their cutting surface area as they progress downhole, allowing for a more thorough and controlled cleanup operation. This unique feature enables taper mills to navigate through restrictions and efficiently clean larger diameter sections of the wellbore. The improved cleanup processes facilitated by taper mills ultimately lead to enhanced well performance, reduced downtime, and increased overall productivity for drilling contractors and operators alike.
Understanding the Functionality of Taper Mills in Wellbore Operations
Design and Structure of Taper Mills
Taper mills are meticulously engineered tools designed to address the specific challenges of wellbore cleanup. The distinctive tapered shape of these mills allows for a gradual increase in diameter as the tool progresses downhole. This design feature enables the mill to navigate through restrictions and effectively clean larger diameter sections of the wellbore. The cutting structure of taper mills typically consists of carbide inserts or diamond-impregnated surfaces, providing superior abrasion resistance and cutting capabilities.
Working Mechanism of Taper Mills
The operational principle of taper mills revolves around their ability to remove debris, scale, and other obstructions through a combination of rotation and axial force. As the mill is lowered into the wellbore, it begins to rotate, allowing its cutting surfaces to engage with the unwanted materials. The tapered design ensures that the tool can start in a smaller diameter and gradually expand its cutting area, effectively addressing various sizes of restrictions and debris accumulations.
Applications in Different Wellbore Scenarios
Taper mills find applications in a wide range of wellbore scenarios, including but not limited to:
- Removal of scale buildup in production tubing
- Clearing cement debris after perforation operations
- Addressing collapsed casing or tubing
- Milling out bridge plugs or packers
- Cleaning up wellbore damage caused by corrosion or mechanical wear
The versatility of taper mills makes them invaluable tools in the arsenal of wellbore maintenance and remediation operations.
Benefits of Incorporating Taper Mills in Wellbore Cleanup Processes
Enhanced Debris Removal Efficiency
One of the primary advantages of using taper mills in wellbore cleanup processes is their superior debris removal efficiency. The tapered design allows for a gradual engagement with the wellbore, ensuring that debris is removed systematically from smaller to larger diameters. This approach minimizes the risk of creating additional blockages or damaging the wellbore while maximizing the amount of debris that can be effectively cleared.
Improved Wellbore Access and Reach
Taper mills excel in providing improved access to hard-to-reach areas of the wellbore. Their ability to start at a smaller diameter and expand as they progress allows them to navigate through restrictions that might otherwise impede conventional cleaning tools. This enhanced reach ensures that a larger portion of the wellbore can be effectively cleaned, leading to more comprehensive maintenance operations.
Cost-Effective Solution for Wellbore Maintenance
Incorporating taper mills into wellbore cleanup processes often proves to be a cost-effective solution for operators and drilling contractors. By efficiently removing obstructions and debris, these tools can significantly reduce the time required for cleanup operations. This time savings translates directly into reduced rig time and associated costs. Additionally, the thorough cleaning provided by taper mills can help prevent future production issues, potentially avoiding costly interventions down the line.
Best Practices for Implementing Taper Mills in Cleanup Operations
Proper Tool Selection and Sizing
Selecting the appropriate taper mill for a specific wellbore cleanup operation is crucial for achieving optimal results. Factors to consider include the wellbore diameter, the nature of the debris or obstruction to be removed, and the overall condition of the well. It's essential to choose a taper mill with the right starting and maximum diameters to ensure effective cleaning without risking damage to the wellbore. Consulting with experienced professionals or tool manufacturers can help in making informed decisions about tool selection and sizing.
Operational Parameters and Techniques
To maximize the effectiveness of taper mills in wellbore cleanup processes, it's important to adhere to recommended operational parameters and techniques. This includes:
- Maintaining appropriate rotational speeds to ensure effective cutting without excessive wear
- Applying the correct amount of weight on bit (WOB) to achieve optimal milling performance
- Implementing proper circulation rates to effectively remove debris and maintain tool cooling
- Utilizing specialized fluids or additives to enhance cutting efficiency and debris removal
By following these best practices, operators can ensure that taper mills perform at their full potential, leading to more successful cleanup operations.
Integration with Complementary Tools and Technologies
While taper mills are highly effective on their own, their performance can be further enhanced when integrated with complementary tools and technologies. For example:
- Combining taper mills with jetting tools can improve debris removal and hole cleaning
- Using real-time downhole measurement tools can provide valuable insights into milling progress and effectiveness
- Incorporating specialized fishing tools alongside taper mills can address complex wellbore obstructions more comprehensively
By adopting a holistic approach to wellbore cleanup that leverages the strengths of various tools and technologies, operators can achieve superior results and optimize their maintenance processes.
In conclusion, taper mills have proven to be invaluable assets in improving wellbore cleanup processes across the oil and gas industry. Their unique design and functionality offer enhanced debris removal efficiency, improved wellbore access, and cost-effective solutions for maintaining well productivity. By understanding the proper implementation of these tools and adhering to best practices, drilling contractors and operators can significantly enhance their wellbore maintenance operations. For more information about taper mills and other oilfield products, please contact us at oiltools15@welongpost.com.
References
- Smith, J. R. (2019). "Advanced Wellbore Cleanup Techniques: A Comprehensive Review." Journal of Petroleum Technology, 71(5), 62-70.
- Johnson, A. L., & Brown, T. K. (2020). "Taper Mill Applications in Complex Wellbore Environments." SPE Drilling & Completion, 35(2), 145-157.
- Williams, R. M. (2018). "Optimizing Wellbore Cleanup Operations: Tools and Strategies." Offshore Technology Conference, Houston, Texas.
- Davis, E. S., & Thompson, L. R. (2021). "Comparative Analysis of Wellbore Cleanup Methods in Horizontal Wells." SPE Production & Operations, 36(3), 588-601.
- Miller, G. A. (2017). "Innovative Approaches to Wellbore Debris Removal Using Advanced Milling Technologies." SPE Annual Technical Conference and Exhibition, San Antonio, Texas.
- Anderson, K. L., & Roberts, P. J. (2022). "Cost-Benefit Analysis of Taper Mill Implementation in Mature Fields." Journal of Petroleum Engineering & Technology, 12(4), 321-335.

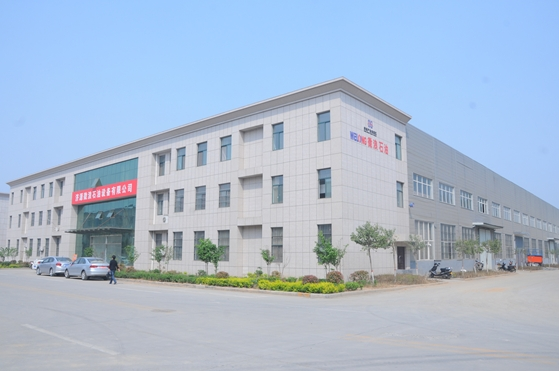
CHINA WELONG - 20+ years manufactuer in oilfield tools
Popular Blogs